جمعه, ۱۴ اردیبهشت, ۱۴۰۳ / 3 May, 2024
مجله ویستا
شکل دادن به فلزات در مقیاس نانو
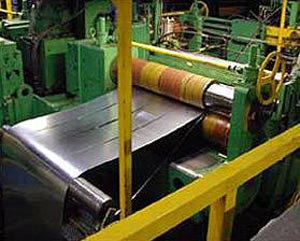
آیندهنگاریها نشان میدهند که علوم مختلف در ده تا پانزده سال آینده زیر چتر نانو قرار میگیرند. در واقع، فناوری نانو رشتههای گوناگون علمی و فنی را به یکدیگر نزدیک میکند. یکی از این رشتهها مهندسی مکانیک است.
امروزه کمتر زمینهٔ تولیدی و پژوهشی یافت میشود که از مهندسی مکانیک بینیاز باشد. زمینههایی نظیر خودروسازی، هواپیماسازی، رُباتیک، آبرسانی، پالایشگاههای نفت و گاز، هوش مصنوعی، بیومکانیک و بسیاری دیگر از این فنون و صنایع، با مهندسی مکانیک درآمیختهاند. در دنیای مکانیک، فرایند «شکلدهی» جایگاه ویژهای دارد. به عنوان مثال، قطعات مختلفِ خودروهای سواری با روشهای مختلفِ شکلدهی مانند کشش، خمش و... ساخته شدهاند. با استفاده از فناوری نانو میتوان بر کیفیت شکلدهی افزود و محصولات باکیفیتتری تولید کرد. این محصولات جدید یک ویژگیِ عمده دارند که همانا یکدستی در تمام محصولات است.
در مجموعهٔ مقالاتی که ارائه خواهد شد، به موضوع شکلدهی در مقیاس نانو خواهیم پرداخت.
● مفاهیم و موضوعات
در این مجموعه مقالات، عناوین مختلفی مورد بحث قرار میگیرند، مناسب است که در شروع کار، اولویتها و عناوین مورد بحث را با هم مرور کنیم تا به چشماندازی از مسیر و هدف نهایی برسیم. البته ممکن است در ابتدا با مفاهیمی روبهرو شوید که قدری ناآشنا هستند، اما سعی شده است تا حد ممکن مطالب ساده بیان شوند و با کمک مثالها و تصاویر مختلف درک آنها سریعتر و بهتر صورت گیرد.
● شکلدهی و مفاهیم مرتبط با آن؛
مایکروشکلدهی به عنوان فرایندی صنعتی که در نزدیکترین مقیاس به حوزهٔ نانو صورت میگیرد؛
نانوشکلدهی.
اگر با این سلسله مقالات همراه شوید، در انتها پاسخ این سؤال اساسی را درخواهید یافت: نانوشکلدهی چیست؟
▪ شکلدهی
در طول روز با محصولات بسیاری روبهرو میشوید که با تغییر شکل ایجاد شدهاند. وقتی این تغییر با کشیدن ورق فلزی ایجاد شود، به آن «کشش» میگویند؛ وقتی تغییر شکل با خم نمودن صورت بگیرد، «خمش» نامیده میشود، و البته در بسیاری از فرایندها از هر دو روش به طور همزمان استفاده میشود، مثلاً در تولید بدنهٔ خودروهای سواری.
عملیات شکلدهی فلزات بسیار متنوع است. ما در ابتدا به دو نمونهٔ ساده اشاره کردیم، اما هدف اصلی از انجام همهٔ آنها ایجاد تغییر شکل مطلوب است. در شکل دادن به فلزات، نیروهای لازم برای شکلدهی و خواصّ مادهٔ تحت شکلدهی از اهمیت زیادی برخوردارند، زیرا باید از ابتدا بدانیم چه مقدار نیرو باید در چه جهتی وارد شود تا مثلاً یک کابل فلزی با روش کشش تولید گردد. شاید در فیزیک به تعریف نیرو دقت کرده باشید. حتماً به یاد دارید که جهت و مقدار از نکات اصلی آن هستند. از طرف دیگر باید بدانیم جنس مادهٔ تحت شکلدهی چیست تا بر اساس خواص آن نیروی لازم را وارد سازیم. مثلاً بین آلمینیوم، فولاد، مس یا چوب تفاوتهای زیادی وجود دارد و اگر از آنها در جای مناسب استفاده نکنیم، هرگز به هدف مورد نظر نمیرسیم.
دو رشتهٔ مهندسی که به طور مستقیم به موضوع شکل دادن فلزات میپردازند، عبارتند از مکانیک و متالورژی.
● شکلپذیری
یکی از نگرانیهای مهم در شکل دادن آن است که آیا میتوان بدون خراب شدن فلز، شکل مطلوبی به آن بخشید یا نه؟ در فرایندی مفروض از تغییر شکل معیّن، محدودیتهای شکل دادن، از مادهای به مادهٔ دیگر تغییر میکند.
حتماً مقاطع فلزی را که در ساختمانسازی به کار گرفته میشوند دیدهاید. برای تولید این مقاطع، فرایند تغییر شکل شامل تبدیل آهن خام به مقاطع مستطیلی یا لانه زنبوری است. هندسهٔ تغییر شکل، آخرین وضعیتی است که از ابتدا به دنبال آن بودهایم؛ یعنی مقطع فلزی مستطیلی یا لانهزنبوری .
بهتر است پیش از پرداختن به تعاریف مرتبط با شکلدهی و فرایندهای وابسته به آن، به مواد مهندسی و خواص آنها بپردازیم.
● مواد مهندسی و مصالح صنعتی
ادوار زندگی بشر را با توجه به عناصر و موادی که در آن اعصار کشف شدهاند، تقسیمبندی کردهاند. در هر دوره، محدوده و تنوع این یافتهها افزایش یافت و در نهایت، مهمترین و مفیدترین یافتهٔ بشر در آن دوره، نام آن عصر را به خود گرفت: عصر حجر، عصر برنز، عصر آهن... در حال حاضر، بعد از اینکه مواد پلاستیک و کامپوزیتها (مواد مرکب از چند مادهٔ مختلف که به آنها «چندسازه» میگویند) به وجود آمد، در «عصر مواد کامپوزیتی» هستیم و با تحولات سریع فناوری انتظار میرود که در آیندهای نهچندان دور به «عصر مواد هوشمند» وارد شویم؛ عصری که اکنون در گامهای آغازین ورود به آن هستیم.
در استفاده از مواد مورد نیاز برای ساخت دستگاهها، ابزارآلات و محصولات صنعتی و غیرصنعتی، باید خواص مورد نیاز هر محصول یا دستگاه توسط مادهٔ آن تأمین شود، زیرا ماده، خوراک اولیه برای شروع کار است؛ مانند سوخت خودرو که باید از ویژگیهای خاصی برخوردار باشد، وگرنه ماشین دچار مشکلات فراوان میشود.
خواص مواد بسیارند. مانند خواص مکانیکی، فیزیکی، سطحی، تولیدی و زیباییشناسانه. به عنوان مثال، خواص فیزیکی مربوط به ویژگیهای ذاتی ماده مثل مقاومت الکتریکی و حرارتی و خواص مغناطیسی است و از مادهای به مادهٔ دیگر فرق میکند و مثلاً مس یا آلمینیوم هادی خوبی برای الکتریسیته و حرارت به شمار میروند.
خواص مکانیکی نیز به جنس ماده وابستهاند. اینکه هر ماده چقدر در مقابل نیروی واردشده مقاومت میکند یا اینکه چقدر باید بر هر ماده نیرو وارد کرد تا از هم گسیخته نشود، به خواص مکانیکی آن مربوط میشود.
مواد و مصالح صنعتی بهطور کلی به دو دسته تقسیمبندی میشوند:
(۱) فلزات و آلیاژهای فلزی، و
(۲) مواد غیرفلزی.
۱) فلزات و آلیاژهای فلزی
فلزات و آلیاژهای فلزی جزء پُرمصرفترین موادی به شمار میروند که در صنعت کاربرد دارند. این مواد به علت خواص متنوعشان، در بخشهای مختلف صنعت به کار میروند. فلزات از مواد معدنی استخراج میشوند و از عناصر فلزی نظیر آهن، آلمینیوم و مس تشکیل میگردند.
ویژگیهایی نظیر مقاومت، قابلیت شکلپذیری، قابلیت جوشکاری، قابلیت رسانایی الکتریکی و حرارتی که در حد بسیار بالایی در فلزات و آلیاژهای فلزی قابل دسترسیاند، جایگاه ویژهای به این مواد در صنعت داده است.
البته فلزات مختلف دارای خواص یکسانی نیستند و همین امر سبب شده است که هر فلز کارآیی خاصی داشته باشد. از جمله مهمترین عناصر فلزی که در صنعت مورد استفاده قرار میگیرند (بر حسب اهمیت) عبارتند از: آهن و آلیاژهای آن نظیر فولاد و چدن و نیز آلمینیوم، مس، برنج، و برنز.
از آنجا که بخش عمدهٔ کاربرد فلزات و آلیاژهای فلزی از آهن و آلیاژهای آن است، گروه فلزات را به دو زیرگروه تقسیم میکنند:
الف) فلز آهن و آلیاژهای آهنی (Ferrous & Alloys)
ب) فلزات غیرآهنی و آلیاژهای آنها (Nonferrous & Alloys)
۲) مواد غیرفلزی
مواد غیرفلزی به علت طبیعت، خواص، مزایا و ویژگیهای خاص خود، همواره مورد توجه در ساخت و تولید اجزای ماشین بودهاند. صنعتگران بر اساس تجربه، انواع مختلف چوب، پلاستیکها و سرامیکها را در اجزای مختلف ماشین، با هدف حذف فلز و سبکسازی آن مورد استفاده قرار میدهند تا در نهایت انرژی کمتری مصرف شود و هزینهٔ تولید محصول کاهش یابد. به طور کلی، مواد غیرفلزی شامل این مواردند:
الف ) پلاستیکها
ب ) الاستومرها
ج) سرامیکها
د ) مواد مرکب (کامپوزیتها)
پلاستیکها گروهی از موادند که مولکولهای بزرگ دارند و از اتصال مولکولهای کوچک حاصل میشوند.
▪ ویژگیهای عمدهٔ این مواد عبارتاند از:
الف) چگالی کم
ب ) مقاومت کافی در برابر خوردگی
ج ) هزینهٔ تولید پایین
از نظر علم شیمی، بیشترِ این مواد، ترکیبات آلی و شامل عناصری نظیر هیدروژن، اکسیژن، کربن و نیتروژناند. پلیمرها دستهٔ بزرگی از مواد آلی هستند که به چند گروه و خانواده تقسیم میشوند. تنوع این مواد به حدی است که در حال حاضر حدود چهار هزار نوع مواد پلیمری با فرمولهای مختلف سنتز و ایجاد شدهاند. از این میان، ۴ یا ۵ نوع پلیمر بیشترین استفادهٔ تجاری و صنعتی را دارند.
پلیمرها را میتوان به دو دستهٔ عمده تقسیم کرد. گروه اول پلاستیکهای «گرمانَرم» (ترموپلاستیک) هستند. به این معنا که قابلیت ذوب مجدد و بازیابی دارند و همانطور که از نام آنها پیداست با وارد کردن مقدار مناسبی حرارت نرم و در انتها ذوب میشوند. در مقابل، دستهٔ دوم، پلاستیکهای «گرماسخت» (ترموست)اند که پس از شکلگیریِ اولیه دیگر نمیتوان آنها را مورد استفادهٔ مجدد قرار داد، یعنی در مقابل حرارت و گرما بسیار مقاوماند.
● خواص مکانیکی مواد
منظور از خواص مکانیکی، واکنش مواد در برابر نیروها و بارهاست. عکسالعمل مواد در برابر نیروهای واردشونده، به ساختمان مولکولی آنها بستگی دارد. آن قسمت از علم مکانیک که صرفاً به بررسی نیروها و واکنشها میپردازد «استاتیک» نامیده میشود و بخشی از آن که واکنش ماده به نیروهای اعمالشده و تغییر شکلهای جزئیِ ناشی این از نیروها را مورد بررسی قرار گیرد، «مقاومت مصالح» نام دارد.
قطعات بر اثر اِعمال نیرو نباید از بین بروند؛ بنابراین برای اینکه مطمئن بشویم قطعه مورد نظر خواص فیزیکی لازم را دارد، باید هنگام انتخاب جنس، شکل، اندازه و طرز ساخت، محاسبههایی انجام دهیم. مثلاً برای تولید رینگهای خودرو، باید محاسبات اولیهای انجام دهیم تا شرایط مادهٔ مورد نیاز بر حسب نوع خودرو، حداکثر سرعت و حداکثر بار قابل حمل توسط آن، مشخص شود.
▪ در اینجا به برخی از اصطلاحات رایج میپردازیم که مؤلفههای مؤثر در بررسی خواص مکانیکی را توضیح میدهند.
۱) تنش - stress :
عبارت است از «مقدار نیروی وارد بر واحد سطح». مقدار تنش از تقسیم نیروی وارد بر جسم بر مساحت سطح مقطع جسم به دست میآید. شاید فکر کنید این تعریف به مفهوم فشار در فیزیک دبیرستان خیلی نزدیک است، اما همانطور که دقت کردهاید، در اینجا شرط عمود بودن مؤلفهی نیروی وارد بر سطح، وجود ندارد.
۲) خستگی - fatigue :
گاهی در قطعهای از یک ماشین کارخانه، شکستگیهایی به وجود میآید. ولی پس از بررسی مشخص میشود که میزان تنش وارد بر قطعه، از حد مجاز کمتر بوده. اما چرا گسیختگی ایجاد شده است؟ علت این پدیده آن است که بطور پیوسته مقدار بار معینی بر قطعه وارد میشود. یعنی مقدار تنش خاصی، بهدفعات بر آن وارد شده است. به این گسیختگیها، «گسیختگی خستگی» میگویند.
۳) کُرنش - strain:
به طور کلی، تمام مواد بر اثر نیرویی هرچند ناچیز، دچار تغییر شکل (تغییر ابعاد) میشوند. به تغییر ابعاد یا اندازههای جسم، بر اثر تنش «کُرنش» میگویند؛ مثل فنری که بهواسطه وارد کردن نیرو بر آن کشیده یا فشرده می شود.
تعریفهای ذکر شده، اصلیترین مفاهیمِ خواص مکانیکیاند. گروهی دیگر از اصطلاحات هستند که از این تعریفها ناشی میشوند. مثلاً به مقاومت ماده در برابر تغییر شکل «استحکام» میگویند و یا مقاومت ماده در برابر خراشیدن، ساییدگی، بُرادهبرداری و بُرش را «سختی» مینامند.
● فرایندهای شکلدهی
پیش از آنکه به فرایندهای شکلدهی بپردازیم، باید به این سؤال پاسخ دهیم که اصلاً چرا از شکلدهی استفاده میکنیم؟
از زمانی که بشر به فکر ساختن ابزار افتاد، راههای بسیاری را تجربه کرد. مثلاً گاهی با بُرادهبرداری از چوب، کمان ساخت تا به شکار بپردازد. زمانی قطعات چوب را بُرید یا آنها را سوراخ کرد. اما در نهایت، لازم داشت از مادهٔ موجود - بدون آنکه از مقدار آن بکاهد – حداکثر استفاده را بکند. فکر اولیهی شکلدهی از اینجا ناشی شد. البته به مرور زمان این تعریف تغییر کرده است، بطوریکه گاهی طول فرایند شکلدهی به مقدار ماده کم میشد.در زیر به طور خلاصه به تعدادی از مشهورترین و متداولترین فرایندها در شکلدهی فلزات میپردازیم:
۱) خمکاری
همهٔ عملیات ورقکاری، شامل خمکاری هم میشود. در اغلب موارد، خمکاری ویژگی اصلی ورقکاری به شمار میرود و به همین دلیل است که جنبههای مختلف آن قابل توجه است. اگر در سپرهای فلزی خودروهای قدیمی دقت کرده باشید، میتوانید آثار خمکاری در محل اتصال سپر با بدنه را ببینید.
۲) کشش
فرایندی است برای کاهش سطح مقطع در ورق، سیم یا مفتول و دیگر مقاطع استاندارد. کشش از پایهایترین فرایندها در شکلدهی به شمار میرود. در طول فرایند کشش، ماده از یک جهت کشیده میشود. در نتیجه، از ابعاد دیگر آن کاسته میگردد.
۳) نوردکاری
نوردکاری از جمله فرایندهای پُرکاربرد در تولید مقاطع استاندارد، مثل ورق، است. در نوردکاریِ صفحهها، ورقها و تسمهها، پهنای قطعهٔ کار فقط اندکی افزایش مییابد. از عوامل تأثیرگذار در این فرایند، میتوان به ارتفاع اولیه و ثانویهٔ قطعه، پهنای آن، سرعت چرخش غلتک، جنس غلتک و نیز دمای کار و جنس قطعهٔ کار اشاره کرد. این فرایند را میتوان با چند غلتک و در چند مرحله تا زمانِ رسیدن به ارتفاع و وضعیت مطلوب ادامه داد.
مثلاً اگر ورقی با ضخامت ۵ میلیمتر در اختیار دارید و میخواهید ضخامت آن را به ۱.۵ میلیمتر برسانید، میتوانید از یک یا چند غلتک که در یک ردیف قرار گرفتهاند استفاده کنید. باهر بار عبور هر یک از غلتکها، اندکی از ضخامت ورق کاسته میشود تا اینکه ضخامت به مقدار دلخواه برسد.
۴) فورجینگ یا آهنکوبی
فورجینگ که در ادبیات غیرفنی به آهنگری نیز ترجمه شده است، به فرایندی گفته میشود که در آن، فلز در فضای بین قالب و ضربهٔ محکمِ پرس قرار میگیرد و پس از خارج شدن اضافهها به شکل دلخواه درمیآید.
نگاه اجمالی ما به فرایند شکلدهی و مسائل مرتبط با آن، در اینجا به پایان میرسد. فراموش نکنید که هنوز سخنی از مقیاس به میان نیاوردهایم. در واقع، مطالبی که تا کنون خواندید مربوط به مقیاسهای رایج در صنعتاند و در صنایعی نظیر خودروسازی، قالبسازی و لولهسازی مطرحاند.
● مایکروشکلدهی
مایکرومتر برابر است با یکهزارم میلیمتر، یعنی هزار برابر بزرگتر از ابعاد نانو. این ابعاد مورد توجه صنایع مدرنی است که میخواهند تا جایی که میشود، به کوچکسازی بپردازند. منظور از کوچکسازی، یا ریزسازی، کاهش ابعاد به مقیاسهایی کمتر از میلیمتر است. این هدف در علوم مختلف، مانند شیمی، فیزیک، مکانیک، متالورژی، پزشکی، رایانه، زیستفناوری و زیستمکانیک مورد توجه و کاوش قرار گرفته و از سوی دانشمندان این علوم در آزمایشگاهها در دست بررسی و تحقیق است.
وقتی میخواهیم نظریهای ارائه کنیم، ابتدا باید در حوزههای مشابه اطلاعاتی به دست آوریم و با دستهبندی آنها حدسهایی بزنیم و سپس با انجام آزمایش صحت آنها را بیازماییم. بنابراین، برای اینکه با جهانی در مقیاس یک میلیونیُم میلیمتر (نانو) آشنا شویم، ابتدا از مقیاسی که دانش بیشتری در زمینهٔ شکلدهی در آن داریم، یعنی مقیاس مایکرو، آغاز میکنیم.
در مایکروشکلدهی به دنبال ایجاد فرایندهای امکانپذیر برای صنعت و تولید انبوه هستیم. آیا تا به حال به این موضوع فکر کردهاید که برای صنعتی شدنِ یک فرایند و تولید انبوه آن چه مراحلی باید طی شود؟
اگر همین امروز اراده کنید که پزشک جراح شوید، نمیتوانید با پوشیدن لباس اتاق عمل دانش مورد نیاز جراحی را به دست آورید. شما باید پس از دوازده سال تحصیل در دبستان، راهنمایی و دبیرستان و سپری کردن دورهٔ هشتسالهٔ پزشکی عمومی و سپس طی دورهٔ تخصص و اخذ مجوز لازم از مراکز معتبر، به فکر پوشیدن لباس جراحی بیفتید. چنین وضعی در دنیای مهندسی هم وجود دارد: ممکن است دانش یا مهارتی در خصوص شکلدهی داشته باشید. اما تنها پس از طی مراحلی مانند محاسبات، آزمایش، مُدلسازی و... میتوان ساختار مشخصی برای ماده تعریف کرد.
مجموع این ساختار مشخص را فناوری میگوییم که نحوهٔ استفاده از دانش را به ما میآموزد. برای صنعتی شدن هم باید برای فناوری مورد نظر دستگاههای مختلف، وسایل اندازهگیری و... تهیه کرد. مهندسان به این قسمتها سامانه (یا سیستم) میگویند. پس اولین گام برای صنعتی کردنِ فناوری، تعریف سیستم و اجزای آن است. دربارهٔ مایکروشکلدهی نیز ابتدا به سیستم آن میپردازیم تا با عناصر تشکیلدهندهٔ آن بیشتر آشنا شوید.
مایکروشکلدهی از نظر علمی «ساخت و تولید ساختارهای دوبُعدی در مقیاس میلیمتری» است. محصولات مایکروشکلدهی، در اجزای الکترونیکی ریزسیستمها و سیستمهای مایکروالکترومکانیکی مثل مایکرورُباتها کاربرد دارند. این محصولات باعث شدهاند که عملیات ریزسازی بهسرعت جلو برود.
● مروری بر تاریخ مایکروشکلدهی
رشد فناوریها و بهخصوص فناوری شکلدهی مایکرو در دههٔ ۱۹۹۰، این سؤال را به وجود آورد که چرا به جای استفاده از تراشکاری در ساخت قطعات ازشکلدهی فلزات استفاده نشود؟
مهندسان و صنعتگران دریافتند که باید قطعه را با روشهای شکلدهی و بدون بُرادهبرداری تغییر شکل دهند. این کار برای تأمین دو هدف اساسی صنعتی و اقتصادی صورت میگیرد: تولید انبوه، و نرخ تولید بالا. تولید انبوه یعنی تولید محصول در تعداد بسیار زیاد، مانند تولید خودرو یا ساخت وسایل خانگی. البته تعداد محصول در صنایع مختلف در تولید انبوه متفاوت است. نرخ تولید بالا نیز به تولید محصول در حداقل زمان ممکن گفته میشود. در این کار آنها با چند مشکل اساسی مواجه بودند که در دو سطح عمدهٔ زیر خلاصه میشدند:
الف) نبودِ دانش پایهای؛ چون در آن زمان دانش بشر در زمینهٔ مایکرو کافی نبود.
ب ) نبودِ کاربرد مشخص و نمونهٔ اولیه؛ زیرا آنها نمیدانستند باید به دنبال ساخت چه محصولی باشند. مثلاً اگر شما به دنبال ساخت هلیکوپتر باشید، با دیدن نمونههای قبلی و طرز کار آن میتوانید به ایدههایی برای ساخت نوع جدید آن برسید.
اولین حرکت در این زمینه توسط یک دانشمند ژاپنی در سال ۱۹۸۹ میلادی آغاز شد. او در گزارش اولیهٔ خود در انجمن فناوریِ شکلدهی ژاپن، طرح اولیهٔ خود را با عنوان «پیشطرح ساخت و توسعهٔ ماشین پرسِ سوپرمایکرو» ارائه کرد و در سال ۱۹۹۰ این ایده را به چاپ رساند.
با شروع حرکت، بهسرعت مسائل و مشکلات پایهای زیادی در مقابل دانشمندان به وجود آمدند. کاهش مقیاس در رسیدن به ابعاد مایکرو در فلزات دشوار است. علاوه بر آن، مشکلات دیگری نیز در مقابل این فناوری جدید قرار دارند، نظیر ابزارآلات و ماشینابزار لازم. از اینرو کاوشها، پژوهشها و تحرکات گستردهٔ علمی و صنعتی برای حل معضلات و یافتن راه حلهای مناسب آغاز شدند که تاکنون نیز ادامه دارند.
● سیستم مایکروشکلدهی
سیستم شکلدهی مایکرو را میتوان مانند سیستم شکلدهی ماکرو به چهار بخش اساسی تقسیم کرد:
الف) مواد (material)
ب) ابزار (tools)
ج ) فرایند (process)
د ) ماشینآلات و تجهیزات (machines & equipment)
علاوه بر مشکلات موجود در شکلدهی ماکرو، مانند طراحی ابزار، فرسایش، خوردگی و عملیات مناسب بر روی مواد، مشکلات جدید ناشی از کاهش ابعاد هم به آنها افزوده میشود. این مشکلات، خود را در هر چهار بخش سیستم شکلدهی نشان میدهند. مثلاً در زمینهٔ مواد در حوزههای شکلپذیری، محدودهٔ شکلدهی، تنشها و کُرنشها؛ در مورد فرایند در خصوص نیروهای شکلدهی، دقت اجزای تولیدی، اصطکاک و مدلسازی؛ و در زمینهٔ ابزار در مورد تولید ابزار به وسیلهٔ فناوریهای جدید، جنس و مواد بهکار رفته در آنها و دقت لازم و مورد نیاز ابزار.
اگرچه روشهای نوینِ ساخت با هدف حل این معضلات توسعه یافتهاند، اما گامهای زیادی در این راه باقی است. یکی از مثالهای این توسعه، ساخت ابزار برجستهکاری (embossing tools) است. این وسایل در یک فرایند حککاری با پرتودهی الکترونی، ابزاری با ابعاد ۲۰۰ نانومتر را میسازند.
در خصوص ماشینآلات و تجهیزات نیز جابهجایی مواد و اجزا دشوار است، زیرا سطح گیرهٔ نگهدارندهٔ قطعه بسیار کوچک است و نیروهای چسبندگی و کشش سطحی بسیار قویتر از نیروی وزن عمل میکنند. توضیح بیشتر اینکه وزن قطعه در مقیاس مایکرو بسیار ناچیز است، در حالی که نیروهای بین مولکولی، که نام برده شدند، چندین برابر بزرگتر از آن هستند. از این رو، قطعه به خودی خود از گیره جدا نمیشود.
در کنار سیستم مایکروشکلدهی، ساختارها و فناوریهای پشتیبان دیگری نیز مورد نیازند. از جمله، فناوریهای مناسبِ اندازهگیری قطعات و ابزار کوچک و همچنین اتاق تمیز. اتاق تمیز، اتاقی است که هوای آن تخلیه شده باشد. زیرا ذرات گرد و غبار و آلودگیها از لحاظ ابعاد در حد مقیاس مورد نظرند و موجب ایجاد خطا در تولید محصول و آزمایشها می شوند.
● فرایندهای مایکرو شکلدهی
مقایسهٔ فرایندهای شکلدهی مایکرو و ماکرو نشان میدهد که دستهای از عوامل، علیرغم کاهش ابعاد ثابت میمانند. به عنوان مثال، ساختار مایکروی مواد مستقل از ابعاد است، یا عوارضنگاری سطح (پستی و بلندی سطح) در طول فرایندِ کاهش ابعاد بدون تغییر باقی میماند. بررسیها نشان میدهند که روشهای مرسوم در شکلدهی ماکرو، در شکلدهی مایکرو غیرقابل انجاماند. بنابراین، باید تحقیقات و بررسیهای کاملی برای نمایش این موضوع به اعداد و ارقام صورت گیرد. برای این کار فرایندهای شکلدهی را به صورت سامانمند (سیستماتیک) به مقیاس پایینتر تبدیل میکنیم. در این صورت، لازم است در زمینهٔ تئوری دانش ابعاد کوچک پیشرفتهایی صورت گیرد، آزمایشهای پایهای با هدف جلوگیری از ایجاد پیچیدگی در ابزار و ساخت آنها اجرا شود و کاربرد مواد گوناگون بررسی گردد.
ت● حقیقات در حال پیشرفت در زمینهٔ فرایندهای مایکروشکلدهی
گرایش به سمت تولید محصولات کوچکتر، منجر به تحقیقات پایهای فراوانی شده است. بر اساس فرضیاتی که در دههٔ ۱۹۵۰ میلادی در آزمایشگاههای بِل مورد آزمایش قرار گرفتند، تغییر شکل پلاستیک (تغییر شکل دائمی مواد؛ در این حالت ماده به حالت قبلی خود باز نمیگردد) باید بر اساس کُرنش و نیز تغییرات کُرنش تحلیل شود، بهخصوص در شرایطی که ابعاد ناحیهٔ تغییر شکل در حدود ۱۰ میکرومتر یا کمتر باشد.
جابهجایی اجزای مایکرو نیز از دیگر موضوعاتی است که مورد بررسی و در دست پژوهشاند. دانشمندان میخواهند از این بررسیها به دو هدف اساسی زیر برسند:
۱) جابهجایی قطعات در مراحل چندگانه همراه با دقت، سرعت و دقت در مکانیابی اجزای کوچک؛
۲) جلوگیری از آثار نامطلوبِ چسبندگی بین اجزا و گیرهٔ نگهدارنده.
نتایج اولیهٔ آزمایشها و پروژههای تحقیقاتی مختلف منجر به ساخت نمونهٔ اولیهٔ سیستم انتقال شده است. این سیستم گیرههای مکندهای دارد که میتوانند در هر ثانیه ۳ قطعه را درفاصلهٔ ۲۵ میلیمتری و با دقت مکانیابی در حدود ۵ میکرومتر جابهجا کنند.
خوب است در انتهای این بخش به این سؤال پاسخ بدهیم که دورنمای کاربرد ماشین پِرِس سوپرمایکرو که در آغاز به آن اشاره کردیم، چیست؟
در سال ۲۰۰۰ میلادی گروهی از پژوهشگران ژاپنی، کارخانهٔ ماشینکاریِ رومیزیِ مایکرو را ساختند که شامل ماشینابزارهایی نظیر ماشینتراش، دستگاه دریل، وسایل جابهجاکننده و پرس بود و میتوانست قطعات مینیاتوری تولید کند. اگرچه این دستگاه هنوز شرایط لازم برای تولید انبوه را ندارد، اما دورنمایی را ترسیم میکند که در آن فناوریهای مایکرو به خصوص فناوریهای شکلدهی در مقیاس مایکرو توسعهٔ چشمگیری یافتهاند.
پژوهشهای ده سال اخیر، فرایندهایی را به دانشمندان نشان داده است که پایه و اساس تحقق فرایندهای صنعتیاند. با تمام این تلاشها فناوری مورد نظر به مراحل توسعهٔ نهایی خود نرسیده است و نیاز به تلاشهای گستردهتری دارد تا به حداقلهای مورد انتظار برای حل مسائل پیشِ رو در آینده برسد.
علیرغم تکاپوی سریع جهانی، در برخورد با مشکلات موجود نیاز به دستیابی به راهحلهای فوری وجود دارد. البته مجموعهٔ مهندسی کنونی میتواند از پسِ حل این مسائل برآید، اما ایدههای زیادی هم وجود دارند که در یک بازهٔ زمانی کوتاه قابل صنعتی شدن نیستند. این ایدهها و طرحها نیازمند زمان زیاد، صرف بودجههای کلان و تحقیقات پایهای فراوانی هستند و زمانی به موفقیت ختم میشوند که همراه با تلاش گستردهٔ دانشمندان و حمایتهای مالی باشند. در عین حال، احتیاج به توسعهٔ روابط میان رشتههایی گوناگونی از قبیل شیمی، فیزیک، رایانه، متالورژی، صنایع و مکانیک نیز دارند.
منبع : باشگاه دانشآموزی نانو
نمایندگی زیمنس ایران فروش PLC S71200/300/400/1500 | درایو …
دریافت خدمات پرستاری در منزل
pameranian.com
پیچ و مهره پارس سهند
تعمیر جک پارکینگ
خرید بلیط هواپیما
غزه ایران روسیه مجلس شورای اسلامی نیکا شاکرمی دولت سیزدهم روز معلم معلمان رهبر انقلاب مجلس بابک زنجانی دولت
سلامت یسنا آتش سوزی قوه قضاییه تهران بارش باران پلیس شهرداری تهران سیل آموزش و پرورش فضای مجازی
قیمت خودرو قیمت طلا قیمت دلار خودرو بازار خودرو دلار سایپا بانک مرکزی ایران خودرو
نمایشگاه کتاب سریال کتاب مسعود اسکویی تلویزیون سینما سینمای ایران دفاع مقدس موسیقی
اسرائیل رژیم صهیونیستی فلسطین جنگ غزه حماس نوار غزه چین اوکراین ترکیه انگلیس نتانیاهو ایالات متحده آمریکا
فوتبال استقلال پرسپولیس علی خطیر سپاهان باشگاه استقلال لیگ برتر ایران تراکتور لیگ برتر رئال مادرید لیگ قهرمانان اروپا بایرن مونیخ
هوش مصنوعی تماس تصویری گوگل اپل آیفون همراه اول تبلیغات اینستاگرام ناسا
خواب بیمه فشار خون کبد چرب کاهش وزن دیابت