جمعه, ۷ اردیبهشت, ۱۴۰۳ / 26 April, 2024
مجله ویستا
سیستمهای ERP وفرآیندپیاده سازی آن
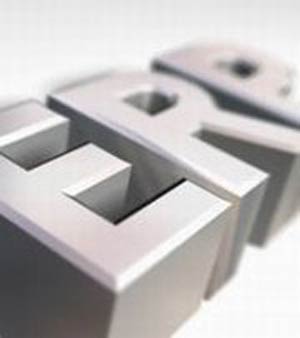
با کوتاه شدن دوره عمر محصولات ، سازمانها قادر نخواهند بود در این محیط رقابتی و همراه با تغییرات شدید در فناوری ، منابع زیادی را برای تولید محصولات جدید صرف نمایند و به عبارتی باید به فکر استفاده بهینه از منابع باشند . بر همین اساس و در جهت استفاده بهینه از منابع سازمان ، مشکل اصلی مدیران کمبود اطلاعات راجع به منابع سازمان نیست بلکه مسئله اصلی همان چگونگی استفاده از حجم زیاد اطلاعات در سازمان میباشد . امروزه استفاده از سیستمهای اطلاعاتی که یکی از دستاوردهای فناوری اطلاعات در سازمانها میباشد به یک ضرورت تبدیل گشته و سازمانها را در جهت استفاده هر چه بیشتر از این فناوری جدید که بستگی به تفکر مدیران ارشد سازمان و شناخت و درک آنان از اهمیت این سیستمها در امورسازمان دارد ، ترغیب خواهد کرد . فناوری اطلاعات به عنوان ابزاری قوی در جهت آمادگی سازمانها برای رقابت در عرصه جهانی و افزایش کارایی سازمان و همچنین تغییر ساختارسازمان از حالت هرمی و مقاوم در برابر تغییر به ساختار مسطح با سطوح کمتر مدیریت و درجه بالای تغییر و انعطاف پذیری مورد استفاده قرار خواهد گرفت . به عبارت دیگر فناوری اطلاعات در سازمانها با حذف فواصل زمانی و مکانی با استفاده از سیستمهای تحت وب ، شبکه های داخلی و خارجی و معماری مبتنی بر Client/Server ، مدیران را در جهت استفاده بهینه از منابع سازمان یاری خواهد کرد یعنی هر شخص قادر است بر اساس حق دسترسی تعریف شده برای وی به اطلاعات مورد نیاز خود دست یافته و بر اساس آن تصمیم گیریهای لازم را انجام دهد .
با استفاده از فناوری اطلاعات سازمانها قادرند وظایف مختلف طراحی ، تولید و خدمات پس از فروش را بطور جداگانه و در نقاط مختلف دنیا انجام دهند و در هر زمان اطلاعات لازم و مورد نیاز خود را بصورت Online دریافت کنند .برای پیاده سازی چنین مکانیزمی استفاده از سیستمهای یکپارچه که قادر باشد تمامی واحدهای سازمان از قبیل مالی، تولید ، انبار ، اداری ، عملیات و... را تحت کنترل داشته باشد ضروری بنظرمیرسد . به چنین سیستمی که بعنوان یکی از فرآورده هاو کاربردهای فناوری اطلاعات در سازمانها به شمار میرود و وظیفه برنامه ریزی منابع سازمانی را برعهده دارد سیستم ERP[۱] (برنامه ریزی منابع موسسه ) گفته میشود . این سیستم از یک بانک اطلاعاتی واحد تشکیل شده و همه بخشهای سازمان از اطلاعات واحد موجود در این بانک اطلاعات بطور مشترک استفاده میکنند .منظور از یکپارچگی در این نرم افزارها استفاده اشتراکی دو یا تعداد بیشتری از برنامه های کاربردی موجود دراین سیستمها از اطلاعات یکسان میباشد و کاربران سیستمها این اطلاعات یکسان را همواره و در همه این برنامه ها مشاهده و مورد استفاده قرار میدهند .
● فرآیند شکل گیری سیستمهای ERP :
همانگونه که میدانیم واژه عملیات برای توصیف همه فعالیتهایی که در رابطه مستقیم با تولید کالا و خدمات انجام میشود ، بکار میرود و مدیریت عملیات نیز فرایند تولید کالا و خدمات را مدیریت کرده و ارزش ایجاد شده را به مشتریان منتقل میکند . بطورکلی فرایندهای اصلی موجود در یک سازمان را میتوان به پنج گروه اصلی تقسیم بندی کرد که عبارتند از :
▪ فرایند توسعه : ازپیدایش یک ایده برای تولید محصول یا خدمتی جدیدآغاز و تا مرحله نمونه سازی[۲] آن محصول ادامه می یابد .
▪ آماده سازی تسهیلات : این مرحله از نمونه سازی محصول یا خدمت جدید تا تکمیل مراحل طراحی ، ساخت و اجرا و تست محصول تولیدی را شامل میشود .
▪ فروش : شامل مطالعه بازار و نیازهای آن تا دریافت یک سفارش از مشتری میباشد .
▪ انجام سفارش : از مرحله دریافت یک سفارش تا تحویل کالا و خدمت درخواست شده به مشتری و پرداخت مبلغ سفارش توسط مشتری را در برمیگیرد .
▪ خدمات : از درخواست مشتری برای خدمات بعد از فروش تا رفع مشکل و راضی نگهداشتن مشتری طی دوره استفاده از محصول را شامل میشود .
بر اساس این نگرش نقش جدیدی از مدیریت تولید و عملیات ظهور پیدا میکند که مدیریت فرایند انجام سفارش از زمان دریافت سفارش از مشتری تا زمان تحویل کالاو خدمات درخواستی به مشتری و کسب رضایت وی را در بر میگیرد . این فرایند ، فرایندی یکپارچه است که حوزه های مختلف سازمان ازجمله بازاریابی (ارتباط با مشتریان ) ، خرید(ارتباط با تامین کنندگان و پیمانکاران ) وعملیات سنتی تولید (مدیریت منابع لازم برای تولید واقعی محصول یا خدمت ) را شامل میشود . این فرایندازپویایی بسیار بالایی برخوردار است زیرا سفارشات مشتریان هر لحظه و در مورد هر ترکیبی از محصولات تولیدی ممکن است از راه برسد . از سوی دیگر این سفارشات بدلیل عدم اطمینان و تغییراتی که در طول زمان درفرایند دریافت مواد اولیه لازم از تامین کنندگان رخ میدهد ، ممکن است با تغییراتی مواجه شود . بنابراین این نقش که در ادبیات مدیریت تولید و عملیات تحت عنوان IPOM یا مدیریت سفارشات و تولید یکپارچه مطرح میگردد ، بسیار مهم و حیاتی به شمار میرود .
در بیان اهمیت مدیریت سفارشات و تولید یکپارچه باید گفت محیط دائما متغیر امروزی که در آن چرخه عمر محصولات بسیار کوتاه بوده و رقابت جهانی نیز بسیار شدت گرفته است ، سازمانها را مجبور میکندکه برای بقا و دوام خود در این محیط سیاستها، استراتژیها وسیستمهای اطلاعاتی لازم و مناسب را بکار گیرند . در برخی از صنایع مدلهای جدید محصولات حتی هر یک یا دو سال یکبار وارد بازارمیشوند و از سوی دیگر تکنولوژی و نیازهای مشتریان نیز دائما در حال تغییر میباشد . بنابراین در چنین بازارهایی انعطاف ، کیفیت ، قیمت و زمان ابعاد کلیدی و اصلی هستند که موجبات دستیابی یک سازمان به موفقیت و بقا را فراهم میکنند .
برای برخورد موثر با چنین شرایطی رویکردهای مدیریتی جدیدی درطول زمان توسعه یافته و بکارگرفته شده اند که این روشها در ادامه بطور گذرا مورد بررسی قرار میگیرند :
▪ فرایند مهندسی همزمان[۳] : در فرایند توسعه محصول ، سازمانها با توسعه محصولات جدید ، نیاز دائما متغیر مشتریان را در زمان کوتاه و با بکارگیری فرایند مهندسی همزمان که یک رویکرد پویا و یکپارچه در توسعه محصول جدید میباشد ، برآورده میکنند . این شیوه رویکردی پویا ، منسجم و مبتنی بر تیمهای توسعه محصول جدید و شامل متخصصانی از حوزه های مختلف سازمان از قبیل بازاریابی (آگاه به نیاز مشتریان و سطح انتظارات آنان ) ، مهندسان و طراحان ( آگاهی از چگونگی تبدیل نیازهای مشتریان به برنامه ها و رویه های تولید محصول) ، متخصصان عملیات و نگهداری ( آگاه به چگونگی توسعه یک محصول با کیفیت و موثر از نظر هزینه ) و... میباشند که با اهداف مشترک ، موجبات توسعه یک محصول جدید را فراهم می آورند . چنین رویکردی را میتوان در مورد فرایند ارضای سفارش و نیاز مشتریان بکار گرفت بطوریکه با یک عکس العمل سریع نسبت به بازار، با زمان تاخیر بسیار کوتاه و جریان نقدینگی بهبود یافته در سازمان بتوان این وظیفه را انجام داد .
▪ تولید بهنگام[۴] : استراتژی دیگر سازمانها برای مواجهه با این محیط جدید ، پذیرش فلسفه هایی از جمله تولید بهنگام است که مبتنی بر موجودی در جریان با حجم کم ، آموزش کارکنان برای دستیابی به انعطاف نیروی کار و انعطاف بالای ماشینها و تجهیزات برای تغییر از یک محصول به محصول دیگر در زمان بسیار کم میباشد . اما این روش در همه سازمانها و صنایع نمیتواند موفق عمل کند و موفقیت آن بستگی به نوع صنعت ، تکنولوژی مورد استفاده و رقابت موجود در بازار خواهد داشت .
▪ روش مورد استفاده دیگر در بهبود فرایند انعطاف پذیری عملیات ، مبتنی بر اصل پارتو[۵] میباشد که بر اساس آن فقط تعداد محدودی از منابع در سازمانهای تولیدی دارای ظرفیت محدود و در نتیجه انعطاف کم میباشند . بنابراین مدیریت باید بر روی منابع محدودو نقاط گلوگاهی(Bottlenecks) تمرکز کند و ظرفیت موجودرا به بهترین روش برای حداکثرکردن عملکردکل سازمان بکارگیرد . این رویکرد تحت عنوان[۶]DBR در سال ۱۹۸۶ شکل گرفت که بعدها با عنوان "تئوری محدودیتها"[۷] توسعه یافت .
▪ رویکرد دیگر، تقسیم سازمانهای تولیدی بصورت تعدادی سلول بود که هر یک از این سلولها درتولید تعداد محدودی از محصولات مشابه تخصص داشتند . این روش تحت عنوان تکنولوژی گروهی[۸](GT ) شناخته میشود و مبتنی بر این فرضیه است که میتوان با مدیریت یک واحد عملیاتی کوچکتر ، عملکرد بهتری را بدست آورد . در این روش همه تجهیزات و نیروی انسانی مورد نیاز برای انجام فرآیند انجام سفارشات مشتریان را در یک محل منتقل میکنند تا محصولاتی ازیک خانواده را تولید کنند . مشکل ایجاد شده در این روش انتقال تجهیزات و سخت افزار مورد نیاز به یک محل مشخص و جابجایی مجدد آنها هنگامی که خانواده محصولات تغییر میکند ، میباشد .
▪ روشهای دیگری همچون تولید چابک[۹] ، CONWIP[۱۰] ، تولید همزمان [۱۱] و... نیز در ادبیات موضوع مورد بحث قرار گرفته است که بطور کلی همه این روشها گامی بسوی انسجام و همزمانی فرایند برآوردن سفارشات مشتریان میباشد .
همزمان باتوسعه این رویکردهای مدیریتی ، سیستمهای اطلاعاتی که بتواند این رویکردهای جدید را پشتیبانی نماید نیز توسعه می یافت . سیستمهای پردازش مبادلات[۱۲] اولیه به شکل سیستمهای MRP[۱۳] رشد یافت که برنامه ریزی و کنترل تولید را مورد پشتیبانی قرار میداد . انطباق و یکپارچگی منطق MRP با سیستمهای مدیریت پایگاه داده رابطه ای (DBMS)[۱۴] ، سیستمهای پشتیبان تصمیم (DSS) و سیستمهای اطلاعات مدیریت (MIS) ، نسل جدیدی از سیستمها را به نام سیستمهایERP ارائه نمود که وظیفه مدیریت نیازمندیهای داده و اطلاعات در سرتاسر یک سازمان را برعهده داشت .
سیستمهایERP ، پشتیبانی تصمیم گیری و اطلاعاتی را که مدیریت سعی میکرد از طریق ابزار دیگری همچون کارتهای کانبان درسیستمهای JIT یا توانایی کنترل کل فرایند دررویکردGT به آن دست یابد ، فراهم میسازد . با استفاده از ERP میتوان مفاهیم GT را بدون آنکه نیاز باشد ماشینها و تجهیزات از محل خود به سلولهای اختصاصی انتقال یابند بکار برد و سیستم JIT را بدون نیاز به کارتهای کانبان اجرا کرد . پس میتوان چنین نتیجه گرفت کهIPOM سیستمی مبتنی بر یک رویکرد تیمی میباشد که این تیم وظیفه اداره کردن و مدیریت فرآیند ارضای سفارشات مشتریان را بوسیله یک سیستم پیشرفته ERP بر عهده دارد .
همانگونه که میدانیم در فرایند ارضای سفارشات ، سه حوزه اصلی بازاریابی ،تدارکات و تولید درگیر هستندکه در هر یک از این حوزه ها ، کاربر سیستمهای اطلاعاتی نقش مهمی را ایفا میکند . برای مثال سیستم اطلاعات مدیریت بازاریابی ، برنامه های کاربردی[۱۵] از قبیل پیش بینی تقاضا و مدیریت سفارشات مشتری را شامل میشود . سیستم اطلاعات مدیریت تدارکات ، مدیریت عرضه کنندگان و سفارشات خرید را در بر میگیرد و نهایتا سیستم اطلاعات مدیریت تولید ، اطلاعاتی در مورد ردیابی محصولات و قطعات و منابع مورد نیاز برای تولید را شامل میشود . نکته مهمی که درواقعیت با آن روبرو هستیم آن است که دو یا بیش از دو بخش از این حوزه های وظیفه ای نیازمند تسهیم و به اشتراک گذاری اطلاعات با یکدیگر هستند . برای مثال اطلاعات در مورد سفارشات تولید و موجودیهای جاری بطور همزمان بوسیله بخشهای بازاریابی ، تدارکات و تولید مورد استفاده قرار میگیرند . در این حالت اگر هر بخش کار خود را با سیاست مستقل و جداگانه ای دنبال کند ، اهداف کلی و کلان سازمان کمرنگ شده و مدیران ارشد و اجرایی سازمان نمیتوانند گزارشات مختلف از عملکرد و وظایف متعدد سازمان خود را بطور یکجا و مرتبط با هم مورد تجزیه و تحلیل قرار دهند . بنابراین به راه حلی نیاز است تا وظایف و فرآیندهای مختلف در یک سازمان را بصورت یکپارچه و به شکل زنجیره ای واحد تبدیل کند . در نتیجه مدیران قادر خواهند بود با استفاده از داده های بدست آمده از کل سازمان در زمان مناسب و بموقع تصمیم گیریهای لازم را انجام دهند . استفاده از این روش برای مشتریان نیز موجب کاهش زمان و هزینه دستیابی به کالا و خدمات مورد نیازشان میگردد . در عمل توانایی و قابلیت سیستمهای اطلاعاتی سنتی برای پشتیبانی از سفارشات پویا و یکپارچه کافی نمیباشد از طرف دیگر مشکل دوباره کاری در ورود داده یکسان به این سیستمها توسط بخشهای مختلف وجود دارد . در نتیجه ، این امرتلاشها را در جهت ایجاد یک سیستم اطلاعات مدیریت یکپارچه سوق داد . این سیستمها بطور ایده آل نه فقط برای پشتیبانی از فرآیند تصمیم گیری بلکه بعنوان ابزاری ارتباطی بین اعضای حوزه های مختلف کاری سازمان مورد استفاده قرار میگیرد .
اولین تلاشی که برای دستیابی به این نیاز صورت پذیرفت در قالب یک گروه از نرم افزارها بنام پردازنده های صورت مواد[۱۶]( (BOMPsبمنظور استفاده بهینه از مواد ، تجهیزات و نیروی انسانی مورد استفاده قرار میگرفت . روش کار در این برنامه ها بدین صورت بود که مقدار مورد نیاز محصول به همراه اجزاء و قطعات مورد نیاز برای تولید آن محصول به سیستم وارد میشد و سیستم میتوانست بر اساس آن ، همه مواد مورد نیاز برای تولید آن مقدار محصول را محاسبه و ارائه کند . بر اساس این نتایج ، پرسنل تدارکات قادر بودند برای خرید و تدارک مواد مورد نیاز ، برنامه ریزی لازم را بعمل آورند . ولی مشکل عمده ای که این نرم افزارها داشت آن بود که مقادیر مواد و قطعات موجود در خط تولید و یا مقادیر موجودی مانده در انبار که از تولیدهای قبلی باقی مانده بود را در نظر نمیگرفت ، بنابراین میزان موجودی انبار به مقدار قابل توجهی افزایش می یافت . از سوی دیگر زمان تاخیر در سفارش مواد و تهیه آن نیز در محاسبات مد نظر قرار نمیگرفت . بنابراین سعی در تولید نرم افزارهایی برای کنترل موجودی انبار گسترش یافت و توجه مدیران به سمت سیستمهای برنامه ریزی مواد مورد نیاز[۱۷](MRP) سوق یافت .
در این دیدگاه جدید که شکل پیشرفته BOMPs بود ، با در دست داشتن اطلاعات لازم در مورد میزان تقاضا برای محصولات و همچنین ساختار محصولات مورد نیاز میتوان براحتی مقدار مورد تقاضا برای هر محصول و اجزای آن را محاسبه کرد و این کار باعث کاهش خطای موجود در زمان پیش بینی میگردد . در این روش، مشکلات موجود در نرم افزارهای پردازشگر صورت مواد نیز حل شده بود . بعبارت دیگراین سیستم، میزان موجودی در گردش و زمان تهیه مواد را نیز در نظر میگرفت و بر این اساس برنامه زمانبندی شده ای برای خرید و تولید مواد ارائه میداد .سیستمهای MRP اولیه که با MRP I شناخته میشدند اطلاعات بازاریابی موجود در برنامه کلان تولید[۱۸] (MPS) را با اطلاعات مربوط به سطوح جاری موجودیها و سفارشات تولید ، خرید ، اطلاعات تکنولوژیک در مورد ساختار محصول و فرایندهای تولید آن محصول ترکیب میکند . نتایج بدست آمده به این صورت خواهد بود که از هر قطعه ، ماده اولیه ، محصول و ... چه میزان خریداری ، تولید و یا مونتاژ شود و چه موقع سفارش خرید یا تولید صادر شود ؟
برنامه کلان تولید(MPS ) ، اطلاعات مربوط به سفارشات مشتریان شرکت و پیش بینی های تقاضای انجام شده را در هر دوره ترکیب میکند . این اطلاعات با حجم موجودیهای جاری مقایسه میشود و زمان دریافت اقلام مورد نیاز نیز با توجه به زمان تاخیر دریافت اقلام از عرضه کنندگان یا در سطح کارخانه (از سایر دپارتمانها ) منظور میگردد . بعدها سیستم برنامه ریزی نیازمندیهای مواد برای سازمانهای خدماتی نیز طراحی و مورد استفاده قرار گرفت[۱۹]. با گذشت زمان قابلیتهای جدیدتری به این سیستمها اضافه شد که از آن میان میتوان به ماجولهای[۲۰] برنامه ریزی ظرفیت[۲۱] و کنترل سطح کارخانه [۲۲] که به بهره برداری کارا از ظرفیتهای محدود منجر میشد اشاره کرد .
در نیمه دوم دهه ۱۹۸۰ میلادی سیستم MRP II[۲۳] که شکل توسعه یافته MRP بود توسط شخصی بنام اولیور وایت[۲۴] ارائه شد . در این سیستم علاوه بر اطلاعات مواد مورد نیاز ، برای سایر منابع از جمله ماشین آلات و تجهیزات ، پرسنل ، ابزار ، ظرفیت انبار و... نیز برنامه ریزی انجام میشد . بدین ترتیب بهره وری منابع و کارایی سازمان به شکل چشمگیری افزایش یافت . با گذشت زمان ، عملیات مربوط به برنامه ریزی توزیع نیز در مجموعه نرم افزارهای MRP II به نام DRP [۲۵] وارد شد و بصورت یکپارچه ای با عملیات تولید مرتبط گردید .
بطور کلی از اوایل دهه ۱۹۶۰ که استفاده از کامپیوترها بطور گسترده در فرایندهای تجاری افزایش یافت از این کامپیوترها برای اتوماتیک کردن وظایف ساده و معمولی تجاری استفاده میشد .در آن زمان در هر شرکت ، نرم افزارهای مورد استفاده بر حسب نیاز آن شرکت توسط متخصصان بخش سیستمهای اطلاعاتی ، تهیه و برنامه نویسی میشد . بنابراین هر شرکتی نرم افزارهای کاربردی تجاری از قبیل حقوق ، حسابداری ، انبارو... مخصوص به خود را دارا بود ولی از آنجا که این متخصصان سابقه کارهای تجاری و مالی را دارا نبودند ، اغلب ، نرم افزارهای تولید شده نمیتوانست جوابگوی نیازهای شرکتها به نحو مطلوب و بهینه باشد . بنابراین در دهه ۱۹۷۰ بعضی از مشاوران و برنامه نوسان کامپیوتر به فکر ارائه راهکار بهتری افتادند تا از این طریق بتوانند نرم افزارهای مورد نیاز شرکتهای تجاری را نه بصورت خاص و ویژه برای هر شرکت بلکه بصورت نرم افزاری استاندارد[۲۶] ارائه کنند . از این طریق شرکتها نیاز به اختراع دوباره چرخ[۲۷] نداشتند و از طرفی بکارگیری این نرم افزارها باعث کاهش در زمان تولید ، بکارگیری ، تست و حتی رفع اشکال[۲۸] میشد . زیرا همه این کارها اغلب یکبار و در شرکت سازنده انجام میگرفت .
نوشته شده توسط احسان ثقه ای
منبع : پایگاه اطلاع رسانی مدیران ایران
همچنین مشاهده کنید
نمایندگی زیمنس ایران فروش PLC S71200/300/400/1500 | درایو …
دریافت خدمات پرستاری در منزل
pameranian.com
پیچ و مهره پارس سهند
خرید میز و صندلی اداری
خرید بلیط هواپیما
گیت کنترل تردد
غزه آمریکا طالبان توماج صالحی حجاب رئیسی رهبر انقلاب سریلانکا کارگران پاکستان مجلس شورای اسلامی دولت
آتش سوزی کنکور سیل هواشناسی تهران سازمان سنجش شهرداری تهران پلیس سلامت فراجا قتل وزارت بهداشت
خودرو دلار ارز قیمت خودرو قیمت دلار قیمت طلا بازار خودرو ایران خودرو بانک مرکزی قیمت سکه مسکن سایپا
ترانه علیدوستی تلویزیون فیلم سینمای ایران کتاب مهران مدیری تئاتر شعر سینما
کنکور ۱۴۰۳
اسرائیل رژیم صهیونیستی جنگ غزه فلسطین روسیه حماس اوکراین طوفان الاقصی جنگ اوکراین اتحادیه اروپا ترکیه انگلیس
فوتبال پرسپولیس استقلال بارسلونا بازی ژاوی باشگاه پرسپولیس باشگاه استقلال فوتسال تراکتور لیگ برتر انگلیس تیم ملی فوتسال ایران
تیک تاک همراه اول بنیاد ملی نخبگان تسلا فیلترینگ ناسا تبلیغات ایلان ماسک اپل
مالاریا سلامت روان کاهش وزن استرس داروخانه پیری دوش گرفتن