جمعه, ۷ اردیبهشت, ۱۴۰۳ / 26 April, 2024
مجله ویستا
فرایند بلوری کردن مستقیم چیپس پلیاستر
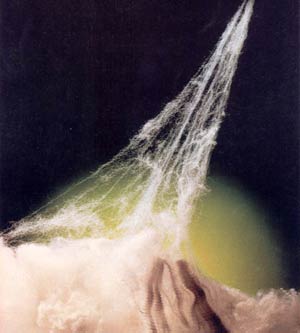
در طی چند دهه اخیر تولیدکنندگان پلیاسترها مخصوصاً پلی اتیلن ترفتالات (PET) و کوپلیمرهای آن، همواره با افزایش تقاضای مصرف از سوی تولیدکنندگان بطری و ظروف بستهبندی تولید شده به روش قالبگیری دمشی مواجه بودهاند و این مسئله باعث شده است که بهطور مستمر در حال بهیهسازی فرایند تولید و کاهش هزینههای آن باشند.
یکی از راههای کاهش هزینههای تولید، افزایش ظرفیت تولید است، اما این مسئله همواره جهت کارخانههای جدیدالاحداث مطرح بوده است و دارای محدودیتهائی نیز میباشد. به همین دلیل تنها راه حل عملی جهت کاهش هزینه تولید در کارخانههای موجود بهینهسازی فرایند تولید و مخصوصاً بهینهسازی مرزهای تماسی (۱) فرایندهای مختلف با هم میباشد.
یکی از مرزهای تماسی بسیار مهم در فرایند تولید چیپس بطری، نقطه تولید چیپس پلیاستر آمورف و نقطه ورود این چیپس به فرایند بلوری شدن است. این مرز تماسی در حقیقت ارتباط دهنده فرایند پلیمری شدن در فاز مذاب با عملیات بلوری شدن (۲) در فاز جامد میباشد. یکی از راههای بهینهسازی این فرایند ادغام مراحل تولید چیپس و فرایند بلوری شدن با یکدیگر میباشد که این تکنیک به نام فرایند بلوری کردن مستقیم (۳) چیپس مشهور است.
توجه به تکنیک بلوری کردن مستقیم یک مسئله جدید نیست و از سالها پیش مورد توجه محققان بوده است (حق ثبت USـ۳۵۴۴۵۲۵ آقای لودویگ در مورد DRR۲۱۳۰) اما این تکنیک تا چند سال قبل تنها در فاز تحقیقاتی قرار داشت و به تازگی با تلاشهای صورت گرفته از سوی چند سازنده تجهیزات مرتبط، این تکنیک از حالت تحقیقاتی به حالت صنعتی درآمده است.
● توسعه
فرایند بلوری کردن مستقیم یک پیشرفت بسیار قابل ملاحظه در فرایند تولید پلیاستر است که منجر به کاهش قابل ملاحظهای در میزان مصرف انرژی در فرایند گذشته است. به کمک این تکنیک جدید میتوان انرژی نهان مذاب پلیاستر را حفظ نمود و از آن در مرحله بلوری کردن استفاده کرد. علاوهبر این، استفاده از این فرایند منجر به حذف مرحله نگهداری میانی (انبار)، پس از فرایند فاز مذاب پلیمری شدن و قبل از فرایند فاز جامد بلوری شدن میشود. هرچند که این فرایند از لحاظ اقتصادی دارای مزایائی میباشد ولی افزایش پیچیدگی کنترل فرایند به دلیل ادغام دو فرایند با عملکردی مجزا با یکدیگر از نقاط ضعف آن میباشد، به همین دلیل ایجاد حلقه ارتباطی مستلزم آمادهسازی و ارتقاء تکنیکهای کنترل فرایند تولید پلیاستر نیز هست.
هرچند که تکنیک بلوری کردن مستقیم را میتوان در مورد انواع پلیاسترها و یا حتی سایر انواع پلیمرهای بلوری شونده به کار برد، اما در این مقاله تنها پلیمر پلی اتیلن ترفتالات (PET) موضوع بحث میباشد.
هرچند که تعدادی از محققان آزمایشاتی جهت بلوری کردن PET در فاز مذاب، قبل از تولید چیپس انجام دادهاند (حق ثبت US ۵۶۲۸۹۴۷، کیلرت)، اما امروزه همچنان ترجیح داده میشود که فرایند بلوری کردن پس از فرایند تولید چیپس انجام شود.
در حین فرایند تولید چیپس (گرانولسازی) سطح دانههای چیپس پلیاستر بر اثر تماس با مایع خنککننده که معمولاً آب است، بهصورت جامد در میآید. با توجه به اینکه چیپسهای داغ و آمورف پلیاستر دارای قدرت چسبندگی بسیار بالائی هستند، خنک شدن سطح آنها باید به اندازهای باشد که در حداقل حالت از ایجاد کلوخه و چسبیدن چیپسها به هم جلوگیری نماید، اما به منظور حفظ حرارت مورد نیاز جهت فرایند بلوری شدن، خنک کردن چیپسها باید در حداقل مقدار ممکن صورت پذیرد. همانطور که مشخص است فرایند بلوری شدن مستقیم باید بتواند به گونهای توازنی میان این دو نیاز متضاد (خنک کردن و گرم کردن) ایجاد نماید. علاوهبر این، فرایند بلوری کردن مستقیم تحت تأثیر پارامترهای دیگری نظیر دمای جریان مذاب، دمای مایع خنککننده، مدت ماندگاری در مایع خنککننده، ابعاد چیپسها، نوع مایع خنککننده و فشار آن نیز قرار دارد.
نتایج تحقیقات نشان داده است که اتیلن گلایکول یک مایع خنککننده بسیار عالی جهت PET میباشد (WO ۰۰/۲۳۴۹۷، ماتائی)، علاوهبر این، جریان آب با فشار زیاد نیز از قدرت خنککنندگی خوبی برخوردار است (WO ۰۴/۰۳۳۱۷۴، کرینبورگ). با توجه به هزینههای عملکردی نسبتاً پائین آب، استفاده از جریان آب جهت خنک کردن بسیار به صرفهتر از اتیلن گلایکول میباشد. در صورتیکه بتوان مشکل چسبیدن چیپسها به یکدیگر را حل نمود (و یا آنرا کاهش داد) میتوان مشکل موازنه بین خنک کردن سطح چیپسها و حفظ حرارت نهان آنها را نیز به راحتی حل نمود. بدین منظور میتوان فرایند بلوری کردن نسبی سطحی را پیشنهاد داد و یا از افزایش هستهگذاری بلورینگی سطحی جهت کاهش چسبندگی سطحی استفاده نمود (WO ۰۰/۲۳۴۹۷ ماتائی و WO ۰۳/۰۳۱۱۳ کولبرت).
● آغاز فرایند
فرایند بلوری کردن مستقیم از حدیدهای (اسپینرت یا رشتهساز) که در آن جریان مذاب پلیمر بهصورت چندین رشته با قطر یکسان تبدیل میشود، آغاز میگردد. با توجه به نوع فرایند تولید چیپس (گرانولسازی) رشتههای تولید شده مسیر کوتاهی را طی میکنند و قبل از بریده شدن بهصورت چیپس، مقداری خنک میشوند و یا اینکه رشتهها بلافاصله پس از خروج از منافذ حدیده بریده و پس از آن خنک میشوند.
معمولاً در این فرایند آب خنککننده را در دمای ۶۰ الی ۹۵ درجه سانتیگراد حفظ میکنند. جریان آب خنککننده در قسمت خروجی دستگاه تولیدکننده چیپس به وسیله خشککن سانتریفیوژ از چیپسها جدا میشود و سپس چیپسها به سمت قسمت بلوریکننده ارسال میشوند. در کارخانجات با ظرفیت تولید بالا معمولاً چندین سیستم گرانولساز مسئول تغذیه یک دستگاه بلوریکننده میباشند. کل زمان تماس آب با چیپسهای PET در این دستگاه ۱ تا ۴ ثانیه میباشد. غالباً در این سیستم از یک فیلتر با اندازه حفرات معین جهت جدا نمودن چیپسهای درشت، ذرات ریز، گرد و ... از چیپسهای استاندارد استفاده میشود (EP ۱۲۰۳۰۴۰، بورر). پس از این مرحله یک سیستم انتقالدهنده چیپس، کاملکننده حلقه ارتباط فرایند تولید چیپس با فرایند بلوری کردن در حالت جامد (SSP)ـ (۴) است.
مهمترین هدف از ابداع بلوری کردن مستقیم، انتقال مقدار بهینهای از انرژی موجود در فاز مذاب به فرایند بلوری کردن میباشد. میزان بهینه این انتقال انرژی نهتنها تحت تأثیر میزان صرفهجوئی در انرژی بلکه سایر فاکتورها نظیر پایداری فرایند، کیفیت محصول و انعطافپذیری عملکرد قرار دارد.
در صورتیکه مقدار بهینهای از انرژی (حرارت) به همراه چیپس وارد سیستم دستگاه بلوریکننده شود دیگر نیازی به تأمین انرژی حرارتی اضافی از سایر منابع خارجی نیست. در اینچنین فرایندی میزان صرفهجوئی در انرژی حداکثر میباشد، زیرا که تنها انرژی مورد نیاز در این سیستم انرژی مکانیکی همزن است که مانع از تولید کلوخه و بههم چسبیدن چیپسها میشود.
در این فرایند دمای سطحی چیپس تحت تأثیر گرمای نهان چیپس بلوری شده است و به همین دلیل با تغییر شرایط فرایند این دما نیز دستخوش تغییر میشود. بهعبارت دیگر حتی تغییر نرخ ورود و خروج جریان مواد موجب تغییر تنظیمات فرایند میگردد. تغییر دمای چیپس منجر به تغییر سایر پارامترها نظیر میزان بلورینگی، استالدهید و یا حتی رطوبت محتوی چیپس نیز میشود. در صورتیکه هیچ اقدامی جهت تثبیت دمای چیپس در حین فرایند صورت نپذیرد، این تغییرات بسیار کوچک در دمای چیپس در حین انجام فرایندهای پائیندستی تغییراتی به مراتب بزرگتر و شدیدتر را ایجاد مینماید.
● ارتقاء فرایند
جهت حصول شرایط پایدارتر فرایندی در بلوری کردن باید مقدار کمی حرارت خارجی نیز به سیستم اعمال شود. این حرارت را میتوان بهصورت ایدهآل به وسیله یک گاز فرایندی گرم به سیستم اضافه نمود، در عین حال از جریان این گاز میتوان جهت هم زدن چیپسها و جلوگیری از بههم چسبیدن آنها نیز استفاده نمود. بدینوسیله دمای چیپسها را میتوان به وسیله دمای گاز ورودی به سیستم تنظیم نمود. این سیستم نسبت به سیستم استاندارد فرایند بلوری کردن، که یک راکتور بستر سیال است، بسیار کوچکتر میباشد (شکل ۱). نتیجه استفاده از این فرایند حصول بیش از ۹۰% صرفهجوئی در مصرف انرژی در یک شرایط پایدار و تولید یک محصول مناسب با بلورینگی همگن و یکنواخت است.
با توجه به اینکه فرایند ایجاد بلورینگی ذاتاً یک فرایند گرمازا است و میزان افزایش دمای چیپس به ازاء ۱۰% افزایش بلورینگی در حدود ۳ درجه سانتیگراد است، به همین دلیل دمای چیپس خروجی از سیستم معمولاً مقداری از دمای محاسبه شده از طریق فرمولهای موازنه انرژی و جرم بیشتر است.
یکی دیگر از مزایای استفاده از سیستم حرارتی خارجی امکان تغذیه چیپسهای خنک به این سیستم میباشد. در اینحالت با توجه به میزان و دمای مواد ورودی و میزان چیپسهای خنک اضافه شده به سیستم، میتوان اندازه دستگاه بلوریکننده، نسبت گاز به چیپس و ظرفیت حرارتی نصب شده را انتخاب نمود. در اینحالت نیز با اجرای عملیات نرمال میزان صرفهجوئی انرژی در حدود ۹۰% میباشد.
شرکتهای ریتر و بوهلر سوئیس که از بهترین تولیدکنندگان دستگاههای تولید چیپس و سیستم بلوری شدن در فاز جامد PET در جهان میباشند به تازگی مشترکاً سیستم جدیدی را با عنوان PET - CC) PET-Crystal-Combi) به بازار عرضه نمودهاند که برمبنای تکنیک بهینه بلوری شدن مستقیم کار میکند و علاوهبر صرفهجوئی در مصرف انرژی، حداکثر میزان پایداری در فرایند را نیز تضمین میکند. از این دستگاه میتوان در هر دو تکنیک چیپسسازی رشته در زیر جریان آب (USG(۵) که منجر به تولید چیپسهای استوانهای میشود و چیپسسازی مستقیم در زیر جریان آب (۶) (UWG) که منجر به تولید چیپسهای کروی میشود استفاده نمود. هر دوی این دستگاهها را میتوان بهطور مستقیم به دستگاه بلوریکننده Q∆ ساخت شرکت بوهلر سوئیس متصل نمود (شکل ۲).
از این فرایند در سیستمهای با ظرفیت بالا نیز میتوان استفاده نمود. در فرایندهای اکستروژن مواد ضایعاتی یا ترکیبات کامپاند، این ظرفیت میتواند در حد ۵۰۰ کیلوگرم در ساعت باشد، در حالیکه در فرایندهای پلیمری شدن مداوم این ظرفیت میتواند تا حد ۵۰ تن در ساعت نیز افزایش یابد. همانگونه که مشخص است اکسترودر را به راحتی میتوان در هر لحظه متوقف نمود در حالیکه سیستمهای بسیار بزرگ پلیمری شدن مداوم ممکن است چندین سال بدون توقف در حال تولید باشند، به همین دلیل فرایند تعمیر و نگهداری سیستمهای تولید چیپس باید بدون توقف خط تولید انجام شود.
● تعمیر و نگهداری
جهت کنترل فرایند در حین انجام عملیات تعمیر و نگهداری بهتر است که از ابتدا یک دستگاه تولید چیپس اضافی در خط تولید پیشبینی و نصب گردد. همانگونه که گفته شد تعداد دستگاههای تولید چیپس که بهصورت موازی کار میکنند بیانگر میزان اضافه ظرفیت و یا سوپاپ اطمینان خط تولید است. بهعنوان مثال در صورتیکه در خط تولید از دو دستگاه تولید چیپس با ظرفیت ۵۰% استفاده نمائیم، اضافه ظرفیت در نظر گرفته شده در خط تولید دقیقاً برابر ۱۰۰% خواهد بود، در حالیکه اگر از سه یا چهار دستگاه تولید چیپس موازی بهطور همزمان استفاده کنیم، ظرفیت کاربردی هر دستگاه در شرایط نرمال به ترتیب برابر ۶۷% و ۷۵% خواهد بود. در تمام این حالتها در صورتیکه یکی از این دستگاهها از مدار خارج شود ظرفیت کارکردی تمام دستگاهها به ۱۰۰% خواهد رسید.
این مثالها همگی بیانگر مزایای استفاده از یک سیستم بلوری کردن مرکزی که قابلیت تغذیه همزمان از چندین سیستم تولید چیپس را دارا است میباشد و تضمینی است جهت حفظ ظرفیت تولید در یک مقدار معین. از طرف مقابل در صورتیکه بخواهیم به هر دستگاه تولید چیپس یک سیستم بلوری کردن را اختصاص دهیم باید حداقل و حداکثر ظرفیت تولیدی را در طراحی سیستم در نظر بگیریم تا با تغییر شرایط فرایند هیچ مشکلی از لحاظ کیفیت محصول ایجاد نشود.
در صورت انجام هرگونه توقف در خط تولید به منظور تعمیر و نگهداری ویا تغییر نوع محصول، سیستم PET-CC میتواند به راحتی به عملکرد نرمان خود ادامه دهد، به عبارت دیگر در اینحالت میتوان از چیپسهای موجود در انبار جهت تغذیه به این سیستم استفاده نمود. جهت افزایش ضریب ایمنی در خط تولید میتوان از یک سیستم انتقال موازی و انتخاب گزینه عملکرد نرمال سیستم تولید چیپس استفاده نمود. در این حالت سیستم تولید چیپس، چیپسهای آمورف سرد به سیستم بلوری کردن تغذیه خواهد کرد.
● کاربرد فرایندی
از سیستم PET-CC در هنگام تولید پلی اتیلن ترفتالات (PET) با میزان کم تا متوسط کومنومر و ویسکوزیته ذاتی ۵۵/۰تا۹۰/۰ g/dl میتوان استفاده نمود. جهت پلیمرهای با ویسکوزیته کمتر و یا میزان کومنومر بیشتر باید یک مرحله آمادهسازی میانی در یک مایع خنککننده استفاده نمود. این مرحله آمادهسازی موجب افزایش هستهگذاری بلوری در سطح چیپس، در هنگام تبادل و همسانسازی دمائی چیپس با مایع خنککننده میشود. هرچند که در اینحالت خاص میزان صرفهجوئی رد مصرف انرژی کم میباشد ولی باز هم میتوان گفت که نسبت به فرایند متداول، استفاده از این روش موجب تولید محصول عاری از هرگونه کلوخه در یک زمان کمتر از بابت بلوری شدن میشود. جهت تولید محصولاتی با تمایل چسبندگی بسیار زیاد، انجام عملیات کواکستروژن هر رشته منفرد با رزین سریع بلوریشونده بهعنوان یک گزینه جهت رسیدن به حداکثر میزان صرفهجوئی در مصرف انرژی با کمترین زمان ماندگاری در فرایند بلوری کردن مطرح میباشد.
یکی دیگر از مزایای استفاده از فرایند PET-CC امکان تولید چیپس با سطح زبر و ناهموار است که سبب کاهش چسبندگی جهت فرایندهای بعدی نظیر بلوری شدن در فاز جامد میشود و منجر به افزایش قدرت انتخاب پارامترها میشود. در اینحالت زبری سطحی چیپسها بدون تولید گرد و غبار حاصل میشود و به همین دلیل نسبت به هم زدن مکانیکی در فرایند بلوری شدن بهتر است. با توجه به این مسائل میتوان گفت که این فرایند دارای یک مرحله نهان گردگیری داخلی میباشد.
در یک جمعبندی کلی میتوان گفت که استفاده از فرایند بلوری کردن مستقیم موجب صرفهجوئی در هزینههای فرایندی PET و یا سایر پلیمرها میشود و فرایند ایجاد بلورینگی PET-CC مزایائی از قبیل انعطافپذیری و قابلیت اطمینان که در کارخانجات مدرن تولید پلیمرها مورد نیاز است را در یک فرایند با کیفیت پایدار بدون ایجاد هرگونه گرد و غبار فراهم میکند.
ترجمه: مهندس شاهین کاظمی، کارشناس ارشد مهندسی شیمی نساجی و علوم الیاف، دانشگاه صنعتی امیرکبیر
ماخذ:
Christel, A., "Direct crystallization for today۰۳۹;s polyester market", International Fiber Journal, December ۲۰۰۷,pp. ۳۶-۳۹
زیرنویسها:
۱) Interface
۲) Crystalization
۳) Direct Crystalization
۴) Solid State polymerization
۵) Underwater Strand Granulation
۶) Under Water Granulation
ماخذ:
Christel, A., "Direct crystallization for today۰۳۹;s polyester market", International Fiber Journal, December ۲۰۰۷,pp. ۳۶-۳۹
زیرنویسها:
۱) Interface
۲) Crystalization
۳) Direct Crystalization
۴) Solid State polymerization
۵) Underwater Strand Granulation
۶) Under Water Granulation
منبع : ماهنامه نساجی امروز
همچنین مشاهده کنید
نمایندگی زیمنس ایران فروش PLC S71200/300/400/1500 | درایو …
دریافت خدمات پرستاری در منزل
pameranian.com
پیچ و مهره پارس سهند
خرید میز و صندلی اداری
خرید بلیط هواپیما
گیت کنترل تردد
ایران حجاب دولت رئیسی رئیس جمهور دولت سیزدهم سریلانکا توماج صالحی پاکستان کارگران مجلس شورای اسلامی سید ابراهیم رئیسی
کنکور تهران سیل آتش سوزی قم هواشناسی سازمان سنجش فضای مجازی پلیس شهرداری تهران سلامت اصفهان
قیمت خودرو خودرو قیمت طلا دلار تورم قیمت دلار بازار خودرو بانک مرکزی ارز ایران خودرو مسکن سایپا
خانواده موسیقی رهبر انقلاب تلویزیون فیلم ترانه علیدوستی سینمای ایران مهران مدیری بازیگر شعر تئاتر
کنکور ۱۴۰۳ عبدالرسول پورعباس
فلسطین رژیم صهیونیستی غزه اسرائیل آمریکا جنگ غزه روسیه حماس اوکراین طوفان الاقصی ایالات متحده آمریکا طالبان
پرسپولیس فوتبال استقلال آلومینیوم اراک جام حذفی بازی بارسلونا لیگ برتر انگلیس ژاوی باشگاه استقلال باشگاه پرسپولیس فوتسال
هوش مصنوعی بنیاد ملی نخبگان ربات تیک تاک ناسا فیلترینگ
مالاریا کاهش وزن زوال عقل سلامت روان داروخانه