جمعه, ۱۴ اردیبهشت, ۱۴۰۳ / 3 May, 2024
مجله ویستا
افزایشپذیری در انعطاف تولید PET
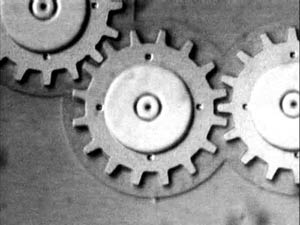
خانواده پلیاسترها مخصوصاً PET یکی از مهمترین خانوادههای مواد پلیمری هستند که بیشترین کاربرد آنها (PET در نساجی و جهت تولید الیاف مصنوعی میباشد. در چند دهه گذشته پیشرفت بسیار قابل ملاحظه سیستمهای تولید PET منجر به گسترش و توسعه طیف خصوصیات این پلیمر و در نتیجه افزایش کاربرد آن در صنایعی نظیر تولید بطری و تولید فیلم گشته است به گونهای که امروزه در بسیاری از کاربردهای خاص نظیر صفحات نوری و مغناطیسی ناگزیر به استفاده از فیلمهای PET میباشیم.
در حال حاضر (سال ۲۰۰۷ میلادی) میزان تولید جهانی پلیاتیلن ترفتلات (PET) بیش از ۳۵ میلیون تن تخمین زده میشود و به نظر میرسد که این میزان در سالهای آتی رشد پیوسته و مداوم خود را حفظ کند.
افزایش ظرفیت واحدهای تولید پلیمر PET منجر گشته است که رقابت بین تولیدکنندگان بسیار شدیدتر شود، به همین دلیل صنایع تولید PET بهطور عام و صنایع تولید الیافت مصنوعی PET بهطور خاص، مجبور به استفاده از روشهای سادهسازی و بهینهسازی فرآیند میباشند تا بتوانند وضعیت فعلی و قدرت رقابتپذیری خود را حفظ نمایند.
با توجه به اینکه هزینه مواد اولیه بیش از ۸۰% قیمت تمامشده محصول PET را تشکیل میدهد، به راحتی میتوان متوجه شد که تولید در مقیاسهای بزرگ صنعتی و افزایش تنوعپذیری فرآیند، تنها راههای حفظ قدرت رقابتپذیری در بازار جهانی میباشد. با مروری بر روی ظرفیت تولید خطوط تولید PET میتوان به راحتی متوجه تمایل تولیدکنندگان جهت افزایش ظرفیت هر خط پلیمری شدن پلیاتیلن ترفتالات شد به گونهای که امروزه خطوط تولید با ظرفیت ۶۰۰ تن در روز نیز عرضه میشوند. افزایش ظرفیت اقتصادی خطوط تولید PET منجر به افزایش قدرت رقابتپذیری از لحاظ قیمت تمامشده گشته است، اما بهطور همزمان با کاهش قدرت تنوعپذیری خطوط تولید و افزایش هزینه تعویض محصول در آنها (حجم بسیار زیاد ضایعات) مشکلاتی را نیز برای تولیدکنندگان ایجاد نموده است، زیرا هرچند که قیمت تمامشده در بازار بسیار اهمیت دارد ولی توانائی پاسخگوئی به نیازهای متنوع مصرفکنندگان نیز از جمله شروط بقا در بازار جهانی است.
محصول PET جهت استفاده در صنایع مختلف به غیر از تفاوت در مشخصات بسیار ویژه پلیمری، به وسیله تنظیم میزان ذرات افزودنی که میتواند بین صفر تا ۲۰ درصد متغیر باشد نیز کنترل میشود. در واحدهای تولید PET مواد افزودنی را غالباً در مراحل اولیه فرآیند تولید پلیمر به سیستم اضافه مینمایند.
اصولاً در سیستمهای تولید پلیمر هر چهقدر ظرفیت خط تولید بیشتر باشد (افزایش ظرفیت هر راکتور) تغییر نوع محصول بسیار مشکلتر میشود و ریسک آن نیز بیشتر میشود. به همین دلیل جهت پاسخگوئی به این چالش سیستم مات کردن مستقیم (یا اصلاح مذاب) طراحی و ابداع شد. به کمک این سیستم حتی خطوط بسیار بزرگ تولید PET نیز میتوانند با حداکثر میزان انعطافپذیری به نیازهای متنوع مشتریان خود پاسخ دهند. اولین خط تولید مجهز به سیستم مات کردن مستقیم در گذشتهای نهچندان دور در حدود سال ۲۰۰۰ میلادی توسط شرکت مهندسی اودهاینونتا ـ فیشر آلمان در چین راهاندازی شد. البته باید اذعان داشت که عدم دسترسی به دیاکسید تیتانیوم (TiO۲) مناسب در کنار تعدادی از مسائل فنی از گسترش سریع این تکنولوژی در سالهای انتهائی قرن بیستم جلوگیری نمود، اما با توسعه و پیشرفت تکنولوژی در چند سال اخیر، اهمیت استفاده از این تکنولوژی در آینده صنعت تولید PET بیش از پیش آشکار گردید.
● اختلاط مواد افزودنی غیر آلی با پلیمر PET
مهمترین ماده افزودنی در پلیمر PET مورد استفاده در صنایع تولید الیاف مصنوعی، دیاکسید تیتانیوم است که بهعنوان ماتکننده نقش بسیار مهمی در تنظیم خصوصیات زیباشناختی الیاف دارد. در حالیکه PET مورد استفاده در صنایع تولید فیلم نیازمند مواد افزودنی دیگری است که از لحاظ خصوصیات فرآیندپذیری فیلم بسیار مهم تلقی میشوند و PET مورد استفاده در صنایع تولید بطری باید از لحاظ رنگ ظاهری و میزان نفوذپذیری گازها اصلاح شود. این مواد عموماً بهصورت پودرهای بلوری بسیار ظریفی هستند که فرآیندپذیری آنها در حالت جامد بسیار چالش برانگیز است. در این تکنولوژی جدید مواد افزودنی در یک مخزن دوغابی چند فازی آماده میشوند، بدین ترتیب این ذرات بلوری را میتوان با کمترین مشکل به پلیمر PET اضافه نمود و خواص مطلوب ماتکنندگی و ... را در محصول نهائی که میتواند منسوج باشد ایجاد نمود.
توزیع یکنواخت ذرات TiO۲ در پلیمر PET یک پیشنیاز جهت فراهم آوردن شرایط مناسب به منظور حصول راندمان و خواص نوری مناسب در پلیمر است. فرآیند دیسپرسیون (توزیع) یکنواخت و تثبیت ذرات TiO۲ در پلیمر PET یکی از مسائل بسیار مهم فرآیندی است که در تکنولوژی متداول تولید به خوبی به آن توجه شده است.
با توجه به پیشرفت بسیار سریع تکنولوژی فرآیندهای پلیمری شدن، ابداع یک روش جدید جهت اضافه نمودن مواد افزودنی به پلیمر با کمترین هزینه بسیار مطلوب و مورد نیاز میباشد. به منظور حصول حداکثر میزان انعطافپذیری در واحدهای با ظرفیت بسیار زیاد، اضافه نمودن مواد افزودنی باید در آخرین مرحله از فرآیند انجام پذیرد. بهعنوان مثال در سیستم ریسندگی مستقیم جهت تولید الیاف با جلا و براقیت متفاوت بهتر است این مواد افزودنی پس از راکتور فینیشر (آخرین راکتور واحد پلیمرساز) و دقیقاً قبل از انتقال مذاب پلیمر به قسمت ریسندگی و یا دستگاه تولید چیپس به مذاب پلیمری اضافه شوند.
● اصول تکنولوژی سیستم مات کردن مستقیم
در سیستم مات کردن مستقیم، جریان مذاب خروجی از آخرین راکتور فرآیند مداوم تولید پلیمر (فینیشر) به دو یا چند جریان مذاب تقسیم میشود. یکی از این جریانهای جانبی پلیمر با عبور از یک اکسترودر دو مارپیچه به خوبی با پودر دیاکسید تیتانیومی که بهطور خاص جهت این کاربرد طراحی و تولید شده است مخلوط میشود.
این جریان مذاب مستربچ مانند، دوباره به جریان مذاب اصلی اضافه میشود و پس از همگنسازی و فیلتر شدن به سمت مرحله بعد که میتواند فرآیند تولید چیپس یا ریسندگی مداوم باشد انتقال مییابد. استفاده از این تکنولوژی تأثیر قابل ملاحظهای در کاهش هزینه تولید، بهبود راندمان و افزایش کیفیت محصول دارد، به همین دلیل استفاده از این تکنولوژی جدید میتواند منجر به افزایش انعطافپذیری خطوط تولید بسیار بزرگ گردد. از جمله مزایای این تکنولوژی میتوان به موارد زیر اشاره نمود:
ـ تولید همزمان محصولات مختلف در یک خط تولید مداوم پلیمری شدن
ـ افزایش انعطافپذیری در انتخاب نوع محصول با اضافه نمودن مقادیر مختلف ماده ماتکننده جهت تولید محصول براق، نیمهمات و کاملاً مات
ـ کاهش میزان تولید محصول میانی در حین تعویض نوع محصول (شکل ۲)
ـ افزایش راندمان فرآیندهای تولید الیاف استیپل و فیلامنت با افزایش زمان عمر فیلتر به کمک بهبود ساختار ماده ماتکننده
ـ افزایش یکنواختی محصول، از آنجائیکه در این تکنولوژی جدید، پلیمر بستر جهت اضافه نمودن TiO۲ و تولید جریان مذاب مستربچ با حریان اصلی مذاب پلیمر کاملاً یکسان است توزیع ذرات TiO۲ یکنواختتر انجام شده و در نتیجه کیفیت الیاف تولیدی نیز بهتر میشود.
ـ کاهش میزان پارامتر رنگی B در مقایسه با محصولات تولید شده توسط تکنولوژی متداول (اضافه نمودن TiO۲ در مراحل اولیه بهصورت سوسپانسیون منواتیلن گلایکول) به دلیل کاهش زمان ماندن مواد ماتکننده در فرآیند.
● مشخصههای مواد افزودنی به روش مات کردن مستقیم
موفقیت تکنولوژی مات کردن مستقیم در تجاری شدن سریع، ارتباط مستقیمی با کیفیت و خصوصیات مواد افزودنی مورد استفاده در این تکنولوژی دارد. بهطور کلی میتوان گفت پودرهای خشکی که در تکنولوژی متداول مورد استفاده قرار میگیرند به گونهای اصلاح شوند که بتوانند دیسپرسیون مناسبی حتی در هنگام اضافه شدن در مراحل انتهائی فرآیند حاصل نمایند. یکی از پارامترهای بسیار مهم در این رابطه حصول عملکرد ریسندگی مناسب است که غالباً بهوسیله تکنولوژی اختلاط دوغابی TiO۲ با کیفیت بالا حاصل میشود.
▪ بهمنظور حصول اطمینان از عملکرد ریسندگی مناسب باید به موارد زیر توجه نمود:
ـ کل سیستمهای مرتبط با انتقال پودر افزودنی، از مرحله باز نمودن بستهبندی آن تا قسمت تزریق به جریان مذاب باید به گونهای طراحی شود که هیچگونه لطمهای به خصوصیات دیسپرسشوندگی آن وارد نشود.
ـ زمان در دسترس جهت انجام تزریق و همگنسازی مواد افزودنی در این سیستم، تنها یک کسر بسیار کوچک از زمانی است که در فرآیندهای متداول در دسترس میباشد.
ـ این مواد افزودنی جدید (جایگزین مواد متداول) نباید هیچگونه تغییری در خصوصیات پلیمر نظیر ویسکوزیته و خواص مکانیکی محصول نظیر استحکام و ازدیاد طول داشته باشند.
ضرورت دستیابی به حداکثر میزان انعطافپذیری در خطوط تولید PET و عرضه تکنولوژیهائی نظیر تکنولوژی مات کردن مستقیم، تولیدکنندگان مواد افزودنی نظیر دیاکسید تیتانیوم را نیز مجبور به انجام تحقیقاتی جهت بهبود خصوصیات مواد تولیدی خود نمود. در این رابطه تطبیق فازهای طراحی محصول و مهندسی ماشینآلات بسیار ضروری است. در اولین قدم تمام فعالیتها جهت اصلاح خصوصیات مواد افزودنی PET بر روی دیاکسید تیتانیوم (بهعنوان مهمترین و پرمصرفترین ماده افزودنی) متمرکز گردید و نتایج حاصل از این آزمایشات منجر به عرضه نوع جدیدی از دیاکسید تیتانیوم گردید. آزمایشات صورت گرفته بر روی الیاف تولید شده توسط تکنولوژی مات کردن مستقیم که از این نوع جدید دیاکسید تیتانیوم استفاده میکردند نشان داد که میزان پراکندگی ذرات افزودنی در الیاف PET در حد بسیار مطلوبی قرار دارد.
● جمعبندی
یافتهها حاکی از آن است که تکنولوژی مات کردن مستقیم یک ابزار بسیار جذاب در مهندسی کارخانجات تولید PET مدرن میباشد. این ابزار به شرکتهای مهندسی این امکان را میدهد که مزایای تولید در حجم بسیار بالای واحدهای پلیمری شدن مداوم را به همراه مزایای حداکثر میزان انعطافپذیری که تنها در واحدهای پلیمری شدن به روش بسته (غیر مداوم یا بچ) وجود دارد را بهطور همزمان در یک کارخانه در اختیار تولیدکننده قرار دهد. در این رابطه شرکتهای تولیدکننده مواد افزودنی نیز توانستهاند به خوبی خود را با این تکنولوژی تطبیق دهند و نوع جدیدی از محصولات خود را منطبق با نیاز این فرآیند جدید به بازار عرضه کنند. این سیستم یک مثال خوب در حمایت توأم شرکتهای مهندسی قطعات و شرکتهای تولیدکننده مواد شیمیائی از تولیدکننده محصول نهائی میباشد. موفقیت تولیدکننده در بازار ناشی از تجهیزات پیشرفته تولید و مواد افزودنی مناسب است. در صورت حمایت سایر تولیدکنندگان مواد افزودنی نظیر مواد افزودنی خاص سیستمهای تولید بطری، فیلم و ... میتوان امید داشت که در آیندهای نهچندان دور تمام واحدهای تولید پلیمر پلیاتیلن ترفتالات (PET) بهطور همزمان توانائی تولید پلیمر نوع الیاف، بطری، فیلم و ... را تنها در یک خط تولید داشته باشند.
تهیه و تنظیم: مهندس عبدالمهدی یوسفیانپور
پینوشت:
شرکت ملی صنایع پتروشیمی ایران، پتروشیمی شهید تندگویان، مرکز پژوهش و توسعه
مأخذ:
Kastner, J., Meyers, F., "Highest flexibility in PET production". Chemical Fibers International, ۵/۲۰۰۷, pp.۲۷۰-۲۷۱
پینوشت:
شرکت ملی صنایع پتروشیمی ایران، پتروشیمی شهید تندگویان، مرکز پژوهش و توسعه
مأخذ:
Kastner, J., Meyers, F., "Highest flexibility in PET production". Chemical Fibers International, ۵/۲۰۰۷, pp.۲۷۰-۲۷۱
منبع : ماهنامه نساجی امروز
نمایندگی زیمنس ایران فروش PLC S71200/300/400/1500 | درایو …
دریافت خدمات پرستاری در منزل
pameranian.com
پیچ و مهره پارس سهند
تعمیر جک پارکینگ
خرید بلیط هواپیما
ایران انتخابات احمد وحیدی حسن روحانی حجاب پاکستان مجلس شورای اسلامی دولت دولت سیزدهم رهبر انقلاب نیکا شاکرمی مجلس
سیل هواشناسی تهران آتش سوزی یسنا شهرداری تهران قوه قضاییه پلیس روز معلم معلم آموزش و پرورش فضای مجازی
قیمت خودرو سهام عدالت قیمت طلا سازمان هواشناسی مالیات طلا بازار خودرو قیمت دلار خودرو حقوق بازنشستگان بانک مرکزی ایران خودرو
مهران غفوریان موسیقی تلویزیون سریال عمو پورنگ ساواک سینمای ایران نمایشگاه کتاب مهران مدیری مسعود اسکویی سینما عفاف و حجاب
رژیم صهیونیستی اسرائیل فلسطین غزه آمریکا جنگ غزه روسیه ترکیه حماس نوار غزه انگلیس اوکراین
استقلال فوتبال پرسپولیس سپاهان علی خطیر باشگاه استقلال لیگ برتر جواد نکونام بازی لیگ برتر ایران تراکتور رئال مادرید
هوش مصنوعی فناوری اپل گوگل ناسا مدیران خودرو تلفن همراه
طب سنتی خواب فشار خون کبد چرب