جمعه, ۱۰ اسفند, ۱۴۰۳ / 28 February, 2025
مجله ویستا
هزینه واقعی روانکاری در صنعت سیمان
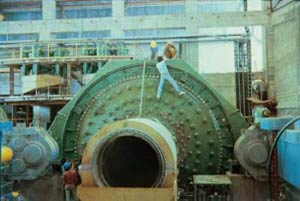
● توانائی چرخدندهها برای تحمل بارهای سنگین را میتوان با روشهای زیر بیشتر کرد:
ـ با تنظیم مسیر انطباق آنها بهطوری که نیروی جانبی به هم وارد نکنند.
ـ تنظیم مسیر انطباق یاتاقانها.
ـ روانکاری کافی و صحیح پینیونها و چرخدندهها.
● روانکاری چرخدندههای باز (بدون حفاظ):
هدف از روانکاری این نوع چرخدندهها جلوگیری از خوردگی سطح پینیون و چرخدنده در اثر سایش میباشد. این امر با استفاده از دستورالعمل روانکاری مصوب او ای ام (OEM)، بین اجزاء در حال تماس صورت میگیرد. تحت شرایط صحیح عملیات روانکاری، چرخدندههای تحت بار بدون اینکه تماس فلز به فلز داشته باشند با یکدیگر درگیر میشوند (یعنی یک لایه از ماده روانساز بین سطح تماس آنها وجود خواهد داشت). از جمله شرایط عملیاتی مطلوب میتوان به بار ثابت چرخدنده، کار پیوسته دستگاه (بدون توقف و استارت پیدرپی)، مسیر انطباق صحیح چرخدندهها و عدم آلودگی روانساز (Lubricant) اشاره کرد، که البته در صنعت سیمان بهندرت این شرایط وجود دارد. چرخدندههای باز و بدون حفاظ که بر روی کورههای دوار و آسیابها نصب میشوند بهطور معمول در محیطهائی با گرد و غبار و رطوبت زیاد کار میکنند. این عوامل باعث میشوند که روانسازهای چرخدندههای بدون حفاظ تحت یکی از سه رژیم جریان روانکاری زیر کار کنند.
● رژیمهای جریانی در روانکاری:
رژیم روانکاری عبارت است از شرایط عملیاتی روانسازی ناشی از حضور ماده روانساز در بین سطوح در حال تماس، هنگامی که سیستم در حال کار میباشد، رژیمهای اصلی عبارتند از:
ـ رژیم لایه مرزی
ـ رژیم لایه مختلط
ـ رژیم لایه پر از سیال
▪ رژیم لایه مرزی:
در این رژیم لایه رواساز بین سطوح در حال تماس با هم خیلی کم است و بار اعمالی به چرخدندهها توسط سطوح فلزی در حال تماس با هم تحمل میشود. اگر مقدار روانساز ناکافی باشد و یا اینکه بار اعمالی به چرخدنده بیشتر از بار قابل تحمل روانساز باشد، این رژیم به وجود میآید. خوردگی بسیار زیاد چرخدندهها در این رژیم به چشم میخورد.
▪ رژیم لایه مختلط:
در این رژیم ضخامت جزئی از لایه روانساز را بر روی چرخدندهها داریم، بهطوری که در بخشهائی از سطح در حال تماس ضخامت روانساز خیلی کم است. اگر سرعت چرخش کاهش یابد یا بار اعمالی افزایش یابد، این رژیم به وجود میآید. همانطور که اشاره شد لایه روانساز به حدی نیست که در تمامی سطوح در حال تماس پخش شود، به همین دلیل بخشی از تنش اعمالی توسط روانساز و بخش دیگر توسط سطوح فلزی در حال تماس تحمل میشود. بنابراین در این رژیم هم خوردگی داریم.
▪ رژیم لایه پر از سیال:
بهترین حالت از نظر کنترل خوردگی، در این رژیم ایجاد میشود. در این رژیم لایه روانساز بهطور کامل تمامی سطوح در حال تماس با هم را پوشش میدهد و تمام تنشهای وارده توسط لایه روانساز تحمل میشود.
▪ ضحامت لایه ماده روانساز:
ضخامت این لایه بستگی به ویسکوزیته روانساز دارد. طبق تعریف ویسکوزیته عبارت است از مقاومت سیال در برابر جریان یافتن. ویسکوزیته یک عامل مهم در روغنکاری آزاد (در معرض محیط) میباشد. روانسازهای مورد استفاده در روانکاوی براساس ویسکوزیتهشان به سه دسته تقسیم میشوند:
ـ گریسها
ـ روغنهای مصنوعی
ـ سیالات باقیمانده از تقطیر نفت که ویسکوزیته بالائی دارند.
به اغلب روانسازها به شکل گریس افزودنیهائی برای افزایش تحملشان در برابر فشارهای بالا اضافه میشود. این افزودنیها باعث ایجاد لایه جامد در سطوح میشود. در این نوع روانسازها تخلیه گریس از چرخدنده بعد از آزاد شدن سطح بسیار مهم است، چراکه در غیر این صورت آلودگیهای همراه گریس به چرخدندهها منتقل میشود. روغنهای مصنوعی از ترکیب مواد مختلف شیمیائی ساخته میشوند و این دسته از روانسازها تقریباً خواص قابل پیشبینی خوبی دارند. روغنهای مصنوعی در دماهای بالا از بقیه انواع دیگر عملکرد بهتری دارند. سیالات باقیمانده برج تقطیر سابقه استفاده زیادی دارند. علاوهبر ویسکوزیته بالا، دارای قابلیت چسبندگی خوب به سطوح و جدا شدن آزادانه از سطوح چرخدنده میباشند. همانطور که اشاره شد جدا شدن آزادانه، برای جلوگیری از پخش آلایندههای روی سطوح دندهها بسیار مهم است. روشهائی که برای روانکاری چرخدندههای باز وجود دارند، میتوانند تأثیر زیادی روی کارائی آنها بگذارند.
● نحوه بهکارگیری روانساز:
روشهای مختلف برای رساندن روانساز به چرخدندههای باز وجود دارد. این روشها بستگی به مشخصات ماده روانساز دارد. از معمولترین این روشها میتوان به موارد زیر اشاره کرد:
ـ روش پیوسته
ـ روش پاشش متناوب
در روش پیوسته بخشی از چرخدنده در حوضچه کوچکی از روغن پر شده غوطهور میشود. در این روش همیشه چرخدنده آغشته به روغن است و مشکلات کنترلی روش پاشش متناوب را ندارد.
البته از آنجائی که روغن مدت زیادی (یک سال) در حوضچه باقی میماند، احتمال آلودگی آن زیاد است.
در روش پاشش متناوب مقدار معینی از روغن در بین فواصل زمانی کنترل شده به چرخدندهها پاشیده میشود. از این روش اغلب بهعنوان روغنکاری متمرکز یاد میشود و در صنعت سیمان و آهک کاربرد فراوانی دارد. هنگام کاهش روغن، یک کنترل کننده الکترونیکی به پمپ نیوماتیکی سیگنالی فرستاده و این کاهش جبران میشود. هندسه نازلها باید به گونهای باشد که روغن را به شکل مخروطی با قطر ۳ الی ۵ اینچ پاشش نمایند. همچنین فاصله افشانههای پاشنده از چرخدندهها ۸ الی ۱۲ اینچ (۲۰۰ الی ۳۰۰ میلیمتر) است، چراکه در این شرایط روغن بهصورت قطرات بسیار ریز (اتمیزه شده) بر روی سطوح پاشیده میشوند. تعداد نازلها بستگی به پهنای چرخدنده دارد و بهطور معمول در هر ۴ الی ۵ اینچ (۱۰۰ الی ۱۲۵ میلیمتر) یک نازل قرار تعبیه میشود.
● مطالعه یک مورد خاص هزینه واقعی روانکاری:
هزینه واقعی روانکاری مسلماً بیشتر از هزینه روانساز مورد استفاده است، ولی به هر حال مقدار روانساز مصرفی و هدر رفته دو عامل مهم تشکیل دهنده هزینه روانکاری است. شرکت سیمان ام تی (MT) واقع در لارامی (Laramie) آمریکا، اخیراً تغییراتی در ضخامت لایه روانساز و رژیم روانکاوی انجام داده است. در حال حاضر تولیدات این کارخانه عبارت است از سیمان پرتلند نوع ۲، سیمان پرتلند نوع ۵، و سیمان چاه نفت نوع جی برای فروش در کلرادو، نبراسکا، اتا و ویومینگ. شرکت ام تی دارای ۵ سری چرخدندههای بزرگ از نوع آزاد میباشد. در ماه اکتبر سال ۲۰۰۵، مدیریت کارخانه طرحی را برای حفاظت بیشتر از چرخدندهها تعریف نمود. هدف دیگر این طرح کاهش مصرف و هدررفت روانساز بود. متعاقب آن، دورههای کاری سیستم پاشنده هم کاهش مییافت. روغن مورد استفاده در شروع پروژه روغن مصنوعی بود. با این نوع روانساز و سیستم پاشش مقدار مصرفی سالانه روغن برای یک کوره پخت و یک آسیاب معادل ۵۸۰۰ پوند بود. در تحقیقی مطالعه بر روی روانسازهای متفاوت و مقدار مصرف آنها برای حفاظت کافی از چرخدندهها صورت پذیرفت. بدین منظور از روغن باقیمانده برج تقطیر که ضخامت کافی لایه روغنکاری را ایجاد میکرد، انتخاب شد. بعد از برآورد ۱۲ ماهه نتایج زیر حاصل شد:
ـ کاهش مصرف روغن برای چرخدنده کوره تا میزان ۳۵۵۰ پوند در سال
۱۵ بار پاشش در هر ۶۰ دقیقه (۴ پوند در روز) در مقابل ۸۰ بار پاشش در هر ۶۰ دقیقه (۸۴/۱۵ پوند در روز) برای یک دوره ۳۰ روز کاری.
ـ کاهش مصرف روغن برای آسیاب تا مقدار تقریبی ۵۲۵ پوند در سال
بیست بار پاشش در هر ۶۰ دقیقه (۸۱/۱ پوند در روز) در مقابل ۳۶ بار پاشش در هر ۶۰ دقیقه (۵۶/۳ پوند در روز) برای یک دوره کاری ۳۰ روزه.
ـ کاهش هزینه واقعی روانکاوی به میزان ۲۶۰۰۰ دلار به علت هزینههای کمتر مصرف روغن باقیمانده برج تقطیر بهجای روغن مصنوعی.
این نتایج نشان میدهد که هزینه واقعی روانکاری مستقیماً تحت تأثیر ضخامت روانساز، رژیم روانکاری و میزان مصرف روانساز قرار دارد.
● نتیجهگیری:
کورههای دوار و آسیابها اساسیترین بخش در صنعت سیمان میباشند. اندازه چرخدندههای این دستگاهها در طی دو دهه گذشته بزرگتر شده و بنابراین تنشهای اعمالی به آنها نیز افزایش یافته است. هدف از روانکاری جلوگیری از سایش دندههای پینیون و چرخدندهها میباشد و روانسازهای مورد استفاده از استاندارد او ای ام (OEM) تبعیت میکنند. ضخامت لایه روانساز بستگی به ویسکوزیته آن دارد و این ضخامت مشخص کننده رژیم روانکاری است و رژیم روانکاری نیز مستقیماً روی مقدار سایش اثرگذار است. بنابراین هزینه واقعی برای روانکاری یک سیستم چرخدنده باز بهطور مستقیم تحت تأثیر ضخامت فیلم ماده روانساز، رژیم جریانی روانکاری، نحوه روانکاری و هزینه خود روانساز مصرفی قرار دارد.
مترجمین: دکتر علی الهوری، استادیار دانشکده مهندسی شیمی، دانشگاه علم و صنعت ایران
مهندس مهدی امجدی، دانشجوی کارشناسی ارشد دانشکده مهندسی شیمی، دانشگاه علم و صنعت ایران
مرجع
Karl Bruno, Petron Corp, USA, The Real Cost of Lubrication, WORLD CEMENT January ۲۰۰۷
مهندس مهدی امجدی، دانشجوی کارشناسی ارشد دانشکده مهندسی شیمی، دانشگاه علم و صنعت ایران
مرجع
Karl Bruno, Petron Corp, USA, The Real Cost of Lubrication, WORLD CEMENT January ۲۰۰۷
منبع : ماهنامه صنعت سیمان
ایران مسعود پزشکیان دولت چهاردهم پزشکیان مجلس شورای اسلامی محمدرضا عارف دولت مجلس کابینه دولت چهاردهم اسماعیل هنیه کابینه پزشکیان محمدجواد ظریف
پیاده روی اربعین تهران عراق پلیس تصادف هواشناسی شهرداری تهران سرقت بازنشستگان قتل آموزش و پرورش دستگیری
ایران خودرو خودرو وام قیمت طلا قیمت دلار قیمت خودرو بانک مرکزی برق بازار خودرو بورس بازار سرمایه قیمت سکه
میراث فرهنگی میدان آزادی سینما رهبر انقلاب بیتا فرهی وزارت فرهنگ و ارشاد اسلامی سینمای ایران تلویزیون کتاب تئاتر موسیقی
وزارت علوم تحقیقات و فناوری آزمون
رژیم صهیونیستی غزه روسیه حماس آمریکا فلسطین جنگ غزه اوکراین حزب الله لبنان دونالد ترامپ طوفان الاقصی ترکیه
پرسپولیس فوتبال ذوب آهن لیگ برتر استقلال لیگ برتر ایران المپیک المپیک 2024 پاریس رئال مادرید لیگ برتر فوتبال ایران مهدی تاج باشگاه پرسپولیس
هوش مصنوعی فناوری سامسونگ ایلان ماسک گوگل تلگرام گوشی ستار هاشمی مریخ روزنامه
فشار خون آلزایمر رژیم غذایی مغز دیابت چاقی افسردگی سلامت پوست