جمعه, ۱۲ بهمن, ۱۴۰۳ / 31 January, 2025
مجله ویستا
رشد اقتصادی پایین، تولید بیش از اندازه؟!
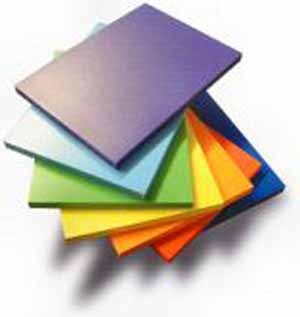
۱ وجود تقاضای كم برای محصولات متنوع در بازارهای پراكنده.
۲ وجود رقابت فشرده.
۳ قیمتهای ثابت یا رو به کاهش.
۴ تغییرات سریع تکنولوژی.
۵ هزینه بالای سرمایه.
۶ تقاضای کارگران تواناتر برای مشارکت در سطوح کاری بالاتر.
۲- اصول اساسی جی آی تی
تویوتا در دهه JIT ۱۹۵۰ را معرفی كرد و در جهت بهبود آن تلاش های بسیاری انجام داد. JIT اولین بار در آمریكای شمالی در دهه۱۹۸۰و همراه با دوایر كیفیت ، كنترل فرایند آماری (SPC) و نوآوریهای دیگری از سوی ژاپنی ها معرفی شد. این سیستم در آمریکای شمالی در مدت زمان اندکی به شکوفایی رسید ولی بواسطه نامناسب بودن شرایط، به سرعت کارایی خود را از دست داد.
JIT از چند قانون ساده زیر پیروی می كند كه عبارتند از:
۱- چیزی نباید تولید شود، مگر اینكه مشتری آنرا سفارش داده باشد.
۲- باید تسطیح تقاضا انجام شود، بطوریكه جریان تولید در سراسر کارخانه یكنواخت باشد.
۳- تمامی فرآیند ها از طریق ابزارهای دیداری ساده (مانند كانبان ها) به تقاضای مشتری مرتبط باشد.
۴- قابلیت انعطاف پرسنل و ماشین آلات به حداكثر برسد.
۳- سیستم جی آی تی
JIT در تویوتا عبارت است از ایجاد جریان ارزش به نحوی كه مشتری جذب شود. اجزاء سیستم JIT عبارتند از:سیستمی از ابزارهای دیداری )معمولا کارت های راهنما( است كه دستورالعمل کار را فراهم کرده و بین مشتریان و تامین كنندگان در داخل و خارج از كارخانه هماهنگی ایجاد می نماید.
سیستمی كه از كار استاندارد شده و كایزن پشتیبانی می كند. هدف این است كه، تولید روزانه با سرعتی یكنواخت صورت گیرد، به طوری كه نوسانات به حداقل برسد. هیجونكا بطور متناقض از هماهنگی سریع با نوسانات تقاضا نیز پشتیبانی می كند.
كانبان و هیجونكا به نوبه خود بستگی به عوامل زیر دارند:
۱. تغییر سریع خطوط كه به سرعت صورت گرفته و منجر به پاسخگویی سریع به سفارش های روزانه مشتری و به حداقل رساندن مودای انتظار می شود.
۲. مدیریت دیداری از طریق سیستم ۵S كه شرایط تولید را بطور شفاف برای تمامی کارکنان نمایان می سازد و باعث هماهنگی بین فعالیتها می شود .
۴- استفاده از فرآیندهایی با قابلیت بالا كه شامل روش ها، اپراتورها و ماشینهای با قابلیت بالا میباشد :
روشهای با قابلیت بالا، به معنای كار استاندارد شده است بطوری كه زیرساخت مورد نیاز كایزن را فراهم میآورد. همچنین به معنای اعمال جیدوكا در حداقل ساختن و جلوگیری از بروز خرابی است.
كارگران دارای قابلیت بالا، به معنای افراد دارای مهارتهای گوناگون در حل مسائل میباشند. كه توانایی انجام كارهای متفاوت را داشته و در فعالیتهای بهبود مشاركت می نمایند .
ماشین آلات دارای قابلیت بالا، به معنای انجام فعالیتهای نگهداری بهرهور جامع TPMو ۵Sبرای مقابله با اتلافات ۶ گانه بزرگ است که عبارتند از خرابی ماشین آلات، تاخیر در تنظیم و راه اندازی، بیكاری و توقفهای جزئی، كاهش سرعت، نقص های فرآیند و كاهش بازده فرایند.
۴- كانبان
كانبان ابزاری تصویری است كه برای دستیابی به تولید به هنگام بكار برده می شود. كانبان معمولاً كارتی مستطیلی شکل، دارای پوشش پلاستیكی است. یك كانبان اجازه تولید یا دستور توقف را صادر کرده و ممكن است حاوی اطلاعات زیر نیز باشد:
تأمین كننده قطعه یا محصول.
مشتری.
محل انبار كردن.
نحوه حمل ونقل (برای مثال اندازه حامل ها و روشهای جابه جایی.
نمونه ای از کارت کانبان
صورت های دیگر كانبان عبارتند از :
فضای باز ایجاد شده در محوطه تولید، این علامت نشان می دهد كه تولید متوقف شده و شكاف ایجاد شده، میبایست پر شود.
در نظر گرفتن خطی بروی نقاله و یا قفسه انبارش، هنگامی كه موجودی از این خط پایین تر میرود، تولید قطعات جایگزین آغاز می گردد.
فضایی باز در وسیله حمل و نقل ایجاد شده ، در این حالت تا تكمیل نمودن فضاهای موجود تولید می كنیم.
جعبه های خالی از قطعات كه می بایست از تعداد مشخصی پر باشد.
ارسال سیگنال الكترونیكی از یك كلید به یك ماشین اتوماتیك، این فرمان نشان می دهد که ماشین تا برطرف کردن تقاضای مشتری به تولید قطعات بپردازد.
روشن شدن یک چراغ بروی صفحه كنترل تولید.
(ضایی روی كارت قطعات )که برای مونتاژ كیت های قطعات مفید است.
یك توپ رنگ شده پینگ پونگ، وقتی مشتری قطعه ای را برمی دارد،یك توپ از طریق مجرای در نظر گرفته شده به محل تولید می رسد و از طرف مشتری به ما می گوید "یك عدد از این قطعه تولید كنید".
یك پیغام الكترونیكی بروی صفحه مانیتور كامپیوتر نیز می تواند به عنوان كانبان در نظر گرفته شود، در صورتی كه تكنولوژی كامپیوترها پیشرفته تر شده و مانیتورهای بزرگی در دسترس باشد تا همه بتوانند بطور همزمان پیغام را ببینند وضعیت تغییر خواهد كرد.
▪دو نوع كارت كانبان وجود دارد:
کانبان تولید؛ كه نوع و تعداد محصولی را كه فرآیند بالا دستی (تأمین كننده) میبایست تولید كند مشخص میسازد.
كانبان برداشت؛ كه نوع و تعداد محصولی را كه فرآیند پایین دستی )مشتری) ممكن است بر دارد مشخص مینماید.
۵- قواعد شش گانه كانبان
کارکنان، مسئولین و سرپرستان، علاوه بر مهارت خوب در حل مسائل، می بایست درك عمیقی نیز از این قوانین داشته باشند. قوانین مورفی در طی پیاده سازی كانبان عبارتند از:
▪قانون اول: اقلام معیوب را به هیچ وجه ارسال نكنید.
تولید اقلام معیوب یعنی سرمایه گذاری كار، زمان و مواد در چیزی كه نمی توان آنرا فروخت. اقلام معیوب بطور جدی توانایی ما را در به حداقل رساندن هزینه ها یعنی آنچه که هدف اولیه به شمار می آید، تحت تاثیر قرار می دهد. الزامات قانون یكم عبارتند از:
رد یابی و تشخیص سریع خرابی كه در اصطلاح كنترل منطقه ای نیز نامیده میشود.
استفاده از سیستم صدور فرمان خودکار (مثل توقف خودكار ماشین آلات در هنگام ایجاد خرابی).
حل كردن سریع مشكلات.
در جایی كه كالاهای سالم با كالاهای خراب مخلوط شده اند، می بایست سریعاً تمامی كالاهای خراب با كالاهای سالم تعویض گردند.
▪قانون دوم: مشتری تنها آنچه را كه نیاز دارد برمی دارد.
در مورد این مفهوم قبلاً تحت عنوانJIT بحث كرده ایم. ذهنیت ما باید از اینكه ما مشتری را تأمین می كنیم، به اینكه مشتری در زمان لازم، به تعداد مورد لزوم از محصول مورد نیاز خود برداشت می كند کاملاً تغییر یابد. چنین شیوه تفكری می تواند مشكلات بحرانی تولید را حل نماید.
چه چیزی تولید می كنیم؟
به چه تعداد تولید می كنیم؟
چه موقع تولید می کنیم؟
پیامدهای قانون دوم عبارتند از:
برداشت هیچ كالایی بدون كانبان صورت نمی پذیرد.
همراه با هر یك از اقلام، یك كانبان نیز وجود دارد.
فقط قطعات مشخص شده و به تعداد معین برداشته می شوند.
به این ترتیب از موداهایی كه در نتیجه تولید بیش از اندازه و زودتر از موعد مقرر و نیز تولید محصولاتی كه مورد سفارش و درخواست مشتری نیست، اجتناب كرده ایم. این موارد شامل افزایش اضافه كاری، موجودی و ظرفیت ساخت میشود، با توجه به این که نمی دانیم آیا ظرفیت موجود كافیست یا خیر.
▪قانون سوم: تولید فقط به تعدادی كه مشتری برداشت كرده انجام میشود.
این قانون از قانون دوم منتج شده و به فرایندهای تولیدی اجازه تولید به صورتی هماهنگ را می دهد، به گونهای که این فرآیندها نظیر اجزای خط مونتاژ عمل كرده و با سرعتی یكنواخت مشغول به كار می باشند. كانبان ها نیز نظیر چرخ دندههایی هستند كه فرآیندهای تامین كننده و مشتری را به هم مرتبط می سازند. پیامدهای این قانون عبارتند از:
بیش از تعداد كانبانهای در دسترس، تولید نكنید.
به همان ترتیبی كه كانبان ها را دریافت می كنید توالی تولید را نیز مراعات كنید.
همچنین میبایست جدول زمانبندی و برنامه ریزی تولید به گونه ای طراحی شود كه در آن توالی و تعداد، بصورت روشن و مشخص ذکر شده باشد.
▪قانون چهارم: هموارسازی تولید
برای اینكه فرآیندها بتوانند قطعه مناسب را در زمان مناسب و به تعداد مناسب تولید نمایند، میبایست سفارشات تولید پایدار شوند. به عبارت دیگر نمی توان یك ساعت۵۰ قطعه سفارش داده و در ساعتی دیگر۲۵۰ قطعه را سفارش داد. چنین امری نیازمند حفظ ظرفیت اضافه و یا تولید جلوتر از برنامه است. در حقیقت به هر میزان كه یك فرآیند در توالی تولید، جلوتر قرار بگیرد، نیاز به ظرفیت بیشتری برای حفظ توان عملیاتی مورد نیاز خود خواهد داشت. برداشت محصول نیز بایستی در زمان ثابت، به تعداد ثابت و در توالی ثابتی انجام شود. هموارسازی تولید با تفصیل بیشتری در ادامه این فصل مطرح خواهد شد.
▪قانون پنجم: از كانبان برای تنظیم دقیق تولید استفاده كنید.
سیستم كانبان نمی تواند پاسخگوی تغییرات اساسی تولید باشد. از این رو كلیه این تغییرات می بایست در برنامه تولید در نظر گرفته شود. كانبان وسیله ای برای تنظیم دقیق است. برای مثال اگر مشتری قطعات را با نرخ ناپایدار نظیر۱۰۰ قطعه در ساعت اول، ۲۰۰ قطعه در ساعت دوم و ۷۵ قطعه در ساعت سوم برداشت كند، احتمالاً می بایست بصورت موردی، تولیدات و مقادیر موجودی را انبار كرده و در افزایش ظرفیت نیز سرمایهگذاری كنیم )یعنی سرمایه گذاری در پرسنل و ماشین آلات( كه این امر در نهایت منجر به سقوط سیستم كانبان خواهد شد.
▪قانون ششم: تقویت و تثبیت فرآیند.
بدون فرآیند های توانا و مستحکم نمی توان قوانین۱تا۵ را اجرا نمود. در نتیجه باید اصول جیدوكا را برای ارتقاء قابلیت فرآیند ها اعمال كرد. لذا باید بطور پیوسته بدنبال حذف مودا، مورا و موری باشیم که انجام آن به طریق زیر امکانپذیر است:
- پیادهسازی سیستم های پوكا ـ یوكه برای ردیابی خطاهایی كه منجر به خرابی خواهد شد.
- كاهش زمانهای تردد و نیز حالات فیزیکی نامناسب كه فشار زیادی را به اپراتورها وارد می کند.
چیدمان منطقی به نحوی كه مثلاً فرآیند ها U شكل بوده و اپراتورها بتوانند بر كل فرآیند نظارت داشته باشند.
ـفراهم کردن سیستم های تصویری و دیداری، به طوریكه فشارهای كاری شناخته شده را كاهش دهند.
دکتر عباس سقایی – مهندس نیما عظیم
منبع : مجله گسترش صنعت
ایران مسعود پزشکیان دولت چهاردهم پزشکیان مجلس شورای اسلامی محمدرضا عارف دولت مجلس کابینه دولت چهاردهم اسماعیل هنیه کابینه پزشکیان محمدجواد ظریف
پیاده روی اربعین تهران عراق پلیس تصادف هواشناسی شهرداری تهران سرقت بازنشستگان قتل آموزش و پرورش دستگیری
ایران خودرو خودرو وام قیمت طلا قیمت دلار قیمت خودرو بانک مرکزی برق بازار خودرو بورس بازار سرمایه قیمت سکه
میراث فرهنگی میدان آزادی سینما رهبر انقلاب بیتا فرهی وزارت فرهنگ و ارشاد اسلامی سینمای ایران تلویزیون کتاب تئاتر موسیقی
وزارت علوم تحقیقات و فناوری آزمون
رژیم صهیونیستی غزه روسیه حماس آمریکا فلسطین جنگ غزه اوکراین حزب الله لبنان دونالد ترامپ طوفان الاقصی ترکیه
پرسپولیس فوتبال ذوب آهن لیگ برتر استقلال لیگ برتر ایران المپیک المپیک 2024 پاریس رئال مادرید لیگ برتر فوتبال ایران مهدی تاج باشگاه پرسپولیس
هوش مصنوعی فناوری سامسونگ ایلان ماسک گوگل تلگرام گوشی ستار هاشمی مریخ روزنامه
فشار خون آلزایمر رژیم غذایی مغز دیابت چاقی افسردگی سلامت پوست