سه شنبه, ۱ خرداد, ۱۴۰۳ / 21 May, 2024
فراگیری رهبری در تویوتا
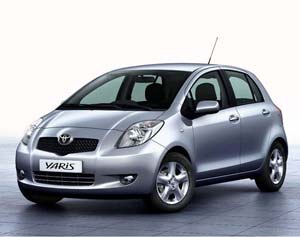
سیستم تولید معروف تویوتا همراه با خودروهای باشكوه، مدیرانی بزرگ نیز تربیت میكند. در این مقاله بخوانید چگونه میتوان دی.اِن.اِی تویوتا را تقلید كرد. تویوتا یكی از پرحكایتترین شركتهای جهان است كه توجه روزنامهنگاران، محققان و مدیرانی را جلب میكند كه در جستوجوی بهینهكاوی سیستم تولید معروف آن هستند. دلیل روشن است: تویوتا از نظر كیفیت، اطمینان، بهرهوری، كاهش هزینه، رشد سهم فروش و بازار و جمعآوری سرمایه بازار، همواره از رقبا پیش بوده است. تویوتا نه فقط از نظر فروش، بلكه از نظر میزان تولید نیز از اواخر سال گذشته به دایملركرایسلر (سومین شركت عظیم خودروسازی در امریكایشمالی) نزدیك شد. برحسب سهم بازار جهانی، اخیراً نیز از فورد (دومین شركت بزرگ خودروسازی) سبقت گرفته است. درآمد خالص و جمع سرمایه بازار آن تا پایان سال ۲۰۰۳ بیش از تمام رقبا بوده است. اما این موفقیتهای بزرگ پرسشی را برمیانگیزد: اگر تویوتا چنین گسترده بررسی و تقلید شده است، چرا فقط چند شركت توانستهاند از نظر عملكرد همتای آن شوند؟
در مقاله سال ۱۹۹۹ خود در هاروارد بیزنس ریویو، با عنوان «كشفرمز دی.اِن.اِی سیستم تولید تویوتا » من و كِنت باون استدلال كردیم بخشی از مشكل آن است كه بیشتر غریبهها بر ابزارها و تاكتیكهای تویوتا (سیستمهای كانبان ، پیوندها، سلولهای تولیدی و غیره) متمركز شدهاند، نه بر مجموعه بنیادین اصول عملیاتی آن. ما در مقاله خود در مجموع چهار اصل یا رویه را مشخص كردیم كه رویهم باعث اطمینان از همبستگی امور جاری با یادگیری چگونه بهتر انجامدادن كارها میشود. این اصول منجر به بهبود مستمر قابلیت اطمینان، انعطافپذیری، ایمنی و كارایی و بهتبع آن، سهم بازار و سودآوری میشود. همانطور كه در آن مقاله توضیح دادهایم، موفقیت واقعی تویوتا فقط ایجاد و استفاده از خود این ابزارها نیست، بلكه در تبدیل كار خود به تجربههایی نهادینه و جاری است.
حال اینكارها كارهایی روزمره مانند نصب صندلی در خودروها باشند یا كارهای پیچیده، ویژه و گسترده مانند طراحی و راهاندازی یك مدل یا كارخانه جدید. ما بحث كردیم تعهد ویژه تویوتا برای استانداردسازی برای صِرف كنترل یا حتی دستیابی به بهترین روش كار نیست. بلكه این استانداردسازی (یا دقیقتر، مشخصههای شفاف چگونگی انجام كار قبل از اجرای آن) با آزمودن كار بهشكلی كه صورت میگیرد، توام شده است. نتیجه نهایی این است كه شكاف بین چیزی كه انتظار میرود و چیزی كه در حقیقت انجام میشود، بلافاصله مشخص میشود. بدین شكل، نهتنها مشكلات كنترل میشوند و از گسترش آنها و آسیبزدن به كار دیگران جلوگیری میشود، بلكه شكاف میان انتظارات و واقعیت نیز بررسی میگردد و شناختی عمیق از محصول، فرایند و افراد حاصل میشود.
این درك و شناخت هم مشخصه جدیدی میشود كه تبدیل به یك «عملكرد برتر» موقت میگردد تا وقتی كه مشكل تازهای مشاهده شود. (به مطلب جنبی «قدرت اصول» مراجعه شود.) داشتن این درك از سیستم تولید تویوتا بهعنوان سیستمی از تجارب نهادینهشده كه از طریق آن عملیات مرتباً بهبود مییابد، یك چیز است و داشتن سازمانی كه در آن كاركنان و مدیران در تمام سطوح با آن اصول زندگی كرده و به دیگران نیز نحوه استفاده آن را یاد میدهند، چیزی دیگر. كشفرمز دی.اِن.اِی تویوتا به این معنا نیست كه میتوان آن را تقلید كرد. بنابراین، چگونه یك شركت میتواند دقیقاً این سیستم را كپیبرداری كند؟ در صفحات بعدی سعی میكنم به این سوال با توضیحدادن نحوه ورود یك جوان بااستعداد (كه برای تصدی پستی ردهبالا در یكی از كارخانههای تویوتا در امریكا استخدام شده بود) به سیستم تولید تویوتا پاسخ دهم. با توجه به موفقیتهای قبلی او، آموزشی كه به او داده شد نمیتوانست با انتظاراتش منطبق باشد. وی چندین مدرك تحصیلی عالی از بهترین دانشگاهها در دست داشت و پیش از آن نیز مدیر چند كارخانه یكی از رقبای تویوتا در امریكای شمالی بود.
اما به جای اینكه یك دوره كوتاه آشنایی را كه معمولاً در انتظار یك مدیر تازهوارد است با سرعت طی كند، وی با تحمل مرارت و در مدتی طولانیتر و به صورت عملی با سیستم آشنا شد و این شیوه آموزشی است كه تویوتا برای هر كارمند جدید بدون توجه به سطح یا وظیفه او در نظر میگیرد. این دوره آموزشی قبل از اینكه او مدیریت كارخانهای را كه قرار بود بهعهده گیرد، بیش از سه ماه طول كشید.این امریكایی مستعد كه او را باب دالیس مینامیم، وقتی وارد تویوتا شد تصور میكرد با كلیات سیستم تولید آن آشنا است (زیرا از ایدههای تویوتا برای بهبود شغل قبلیش كمك میگرفت) و فقط باید معلومات خود را برای بهبود عملیات در شغل جدید تنظیم كند. بعد از خاتمه آموزش، دریافت بهبود عملیات اجرایی وظیفه او نیست، بلكه مسئولیت خود كارگران است. نقش ایشان فقط كمك به درك این مسئولیت و انجام آن بود. آموزش فوق به او یاد داد چگونه مبنای كار را آزمودن و تجربهكردن قرار دهد كه نتیجه آن، یادگیری و بهبود مستمر و یاددادن آن به دیگران است.
● برنامه
در یك صبح زمستانی در ژانویه سال ۲۰۰۲، دالیس وارد دفتر مركزی تویوتا در شهر كنتاكی شد. در آنجا مایك تاكاهاشی (اسم واقعی نیست) به استقبال او آمد. تاكاهاشی از مدیران ارشد مركز پشتیبانی تامینكنندگان تویوتا بود. این مركز مسئولیت ارتقا شایستگی كارخانههای تویوتا و تامینكنندگان را برعهده دارد. بههمین ترتیب، تاكاهاشی مسئول آشناسازی با شركت بود. بعد از پایان تشریفات معارفه، تاكاهاشی، دالیس را با خودرو خود نه به جایی كه قرار بود در آنجا كار كند، بلكه به یكی دیگر از كارخانههای موتورسازی تویوتا برد. قرار بود در این كارخانه هماهنگی دالیس با شركت جدیدش صورت پذیرد. این برنامه هماهنگسازی شامل دوازده هفته كار در كارخانه موتورسازی امریكا و ده روز كار و مشاهده در كارخانههای تویوتا و تامینكنندگانش در ژاپن بود. محتوای برنامه آموزش دالیس (مثل هر مدیر دیگری) بستگی به نیازهای وی بر اساس نظر تاكاهاشی داشت.
▪ شروع از ابتدا
اولین تكلیف باب دالیس در كارخانه موتورسازی امریكا، كمك به گروهی كوچك از نوزده كارگر مونتاژ موتور بود. هدف، بهبود بهرهوری، دسترسی عملیاتی به ماشینآلات و تجهیزات و ایمنی ارگونومیك بود. برای شش هفته اول، تاكاهاشی، دالیس را درگیر چرخههای مشاهده و تغییر فرایندهای كاری افراد و بهتبع آن، تمركز بر بهرهوری و ایمنی كرد. بهطور مثال، دالیس باید با همكاری رهبران گروه، رهبران و اعضای تیم، نحوه انجام وظایف مختلف، مسئول هر وظیفه در شرایط گوناگون و نحوه انتقال اطلاعات، مواد و خدمات را مستندسازی میكرد. او باید تغییرات لازم را جهت حل مشكلاتی كه مشاهده میكرد صورت میداد و سپس به ارزیابی آن تغییرات میپرداخت. علیرغم تجربه و موفقیتهای قبلی، دالیس بهحال خود رها نشد. طی جلساتی با تاكاهاشی، كار هفتگی دالیس تنظیم میشد.
دوشنبهها باید به شرح موارد ذیل میپرداخت: نظر وی در مورد نحوه كار فرایند مونتاژ بر مبنای مشاهدات و تجارب هفته گذشته و برداشت وی از مسائل و مشكلات خط مونتاژ و تغییراتی كه وی یا سایرین برای حل این مشكلات صورت داده بودند یا در ذهن داشتند و تاثیرات احتمالی توصیههای وی. جمعهها، تاكاهشی به مرور كارهای دالیس میپرداخت و عملكرد واقعی را با برنامهها و انتظاراتی مقایسه میكرد كه دوشنبه قبل به مباحثه در مورد آنها پرداخته بودند. در شش هفته اول، ۲۵ تغییر در ارتباط با وظایفی منفرد بهاجرا درآمد. بهطور مثال، تعدادی از قفسههای قطعات برای دسترسی هر چه آسانتر بازآرایی شدند و جای دستگیره یك ماشین تغییر داده شد تا كشش مچ دست كاهش یافته و ایمنی ارگونومیك افزایش یابد. دالیس و سایر اعضای گروه، ۷۵ توصیه برای توزیع مجدد كار خود ارائه كردند. این تغییرات به اندازهای بودند كه بازآرایی محیط كار را الزامی كنند. بهطور مثال، تغییر در محل نصب یك قطعه خاص مستلزم تغییر مكان انبار مواد و جابهجا كردن پرده پنجرهها و نیز نحوه ارتباط افراد و كدبندی كامپیوتر بود. این تغییرات به كمك متخصصان فنی بخشهای نگهداری و مهندسی در زمان تعطیلی آخر هفته كارخانه و بعد از هفته پنجم از شش هفته صورت گرفت. دالیس و تاكاهاشی، هفته ششم را به بررسی خط مونتاژ و بررسی این نكته اختصاص دادند كه آیا آن ۷۵ تغییر اثر مطلوبی داشتهاند یا خیر. آنها دریافتند بهرهوری كارگران و ایمنی ارگونومیك بهبود قابلتوجهی یافته است.
متاسفانه، تغییرات موجب كاهش دسترسی عملیاتی به ماشینآلات هم شدند. این بدان معناست كه تغییراتی كه بهبود بهرهوری و ارگونومی را حاصل آوردند، ماشینآلات را دچار سوءكاركرد كردند. در عوض، قبل از اعمال تغییرات آنقدر زمان بیهوده در كار بود كه اگر ماشینی هم دچار نقص میشد، عواقب یا دردسری برای هیچكس نداشت. اما با اعمال تغییرات مورد نظر دالیس، گروه توانست به جای ۱۹ نفر از ۱۵ نفر برای انجام همان میزان كار بهره گیرد. همچنین، امكان كاهش زمان لازم برای انجام هر وظیفه و بهبود توازن حجم كار ایجاد شد. با وجود سیستمی با حسابوكتابتر، مشكلات پیشین مرتبط با ماشینآلات كه پیامد منفی نداشتند، اكنون تاثیر قابلتوجهی برجا میگذاشتند. پس از آنكه دالیس وظایف انسانی را در خط مونتاژ بهبود بخشید، تاكاهاشی وی را به بررسی چگونگی عملكرد ماشینآلات مشغول ساخت.
ترجمه: مهندس محمدرضا دلجو
نمایندگی زیمنس ایران فروش PLC S71200/300/400/1500 | درایو …
دریافت خدمات پرستاری در منزل
پیچ و مهره پارس سهند
تعمیر جک پارکینگ
خرید بلیط هواپیما
سید ابراهیم رئیسی رئیس جمهور شهدای خدمت ابراهیم رئیسی سقوط بالگرد رئیسی رئیسی سیدابراهیم رئیسی ایران شهادت بالگرد حسین امیرعبداللهیان تبریز
تهران هواشناسی کنکور امتحانات نهایی شهرداری تهران شورای شهر تهران هلال احمر سانحه بالگرد رئیسی بارش باران مشهد سیل قوه قضاییه
قیمت دلار قیمت خودرو بورس قیمت طلا خودرو بازار خودرو یارانه دلار یارانه نقدی حقوق بازنشستگان سایپا بازنشستگان
سینمای ایران سینما تسلیت تلویزیون جشنواره کن لیلا حاتمی آیت الله سید ابراهیم رئیسی هنرمندان شعر رسانه ملی سریال قرآن کریم
کنکور ۱۴۰۳ تجهیزات پزشکی دانش بنیان تلسکوپ فضایی هابل
رژیم صهیونیستی غزه روسیه اسرائیل امیرعبداللهیان ترکیه جنگ غزه فلسطین آمریکا چین ولادیمیر پوتین اوکراین
فوتبال پرسپولیس استقلال رئال مادرید والیبال لیگ برتر لیگ برتر ایران باشگاه پرسپولیس فدراسیون فوتبال لیگ برتر انگلیس باشگاه استقلال منچسترسیتی
هوش مصنوعی مایکروسافت اپل گوگل سامسونگ ناسا تبلیغات موبایل فناوری
سلامت نوشیدن آب قهوه مغز کاهش وزن رژیم غذایی خواب طول عمر آلزایمر مغز انسان افسردگی