شنبه, ۱۱ اسفند, ۱۴۰۳ / 1 March, 2025
مجله ویستا
برنامهریزی نگهداری و تعمیرات
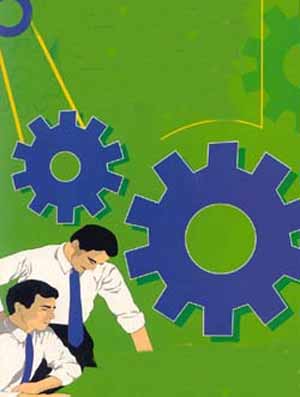
۱- دوره نخست و BM :
سیر تحولات در دوره نخست تحقیقات نشان میدهد که گامهای اولیه در پیادهسازی نت در سالهای قبل از جنگ جهانی دوم رخ داده است . در آن ایام صنایع به شکل امروزی مکانیزه نبوده و لذا خرابیها و توقف ناگهانی ماشینآلات مشکلی جدی را برای دست اندرکاران امر تولید ایجاد نمینمود ؛ به بیان دیگر ، جلوگیری از بروز عیب در ذهن اکثر مدیران و مهندسین مفهوم نداشته و یا حداقل ضرورتی از این نظر احساس نمیگردید . علاوه بر این اکثر ماشینآلات و تجهیزات تولیدی از طرح نسبتا سادهای برخوردار بوده و این ویژگی ، کار با آنها را ساده و تعمیرشان را آسان مینمود . نتیجه آنکه در آن زمان نیازی به استفاده از نت سیستماتیک احساس نمیگردیده و اکثر شرکتها و واحدهای تولیدی و صنعتی تنها در زمانی که دستگاه و یا تجهیزات از کار میافتادند ، بازبینی و یا تعمیر آنها را آغاز مینمودند ؛ در واقع سیستم نگهداری و تعمیرات به هنگام از کارافتادگی (Breakdown Maintenance) معمول بود .
۲- دوره دوم و TPM :
همه چیز در خلال جنگ جهانی دوم به صورتی انفجارآمیز دستخوش تحول گردید . فشارهای ناشی از زمان جنگ ، تقاضا برای انواع محصولات را افزایش داده و این در حالی بود که نیروی انسانی صنایع بشدت کاهش یافته بود ؛ این عامل سبب گردید تا مکانیزاسیون افزایش پیدا نماید . میتوان سال ۱۹۵۰ را سال رونق طراحی و ساخت ماشینآلات مکانیزه نامید و این ایام ، سرآغاز وابستگی صنایع به تجهیزات مکانیزه و اتوماسیون بوده است .
با افزایش روزافزون اتوماسیون مساله شکست و از کارافتادگی ماشینآلات نیز از اهمیت بیشتری برخوردار میگشت ؛ پس از گذشت چندی روند افزایش خرابیها به گونهای گردید که کمیت و کیفیت تولیدات را تحتالشعاع خود قرار داده و اسباب نارضایتی صاحبان صنایع را فراهم نمود . ادامه این روند ناخوشایند ، مدیران و کارشناسان را به فکر چاره و راهحلی مناسب برای جلوگیری از روند رو به رشد عیوب نمود .
در این رهگذر سیستم نگهداری و تعمیرات پیشگیرانه (Preventive Maintenance) بعنوان چاره درد و راهحلی مناسب در کشور امریکا پیشنهاد گردید و به اجرا درآمد . نیاز صنایع بر تولید محصولات با کیفیت بالا و قیمت مناسب جهت افزایش توانایی رقابت در بازار موجب گردید که استفاده از سیستم PM رونق یافته و در این راستا اجرای تعمیرات و تعویضهای پیشگیرانه دورهای بعنوان موثرترین راهحل جهت کاهش خرابیها مورد استفاده قرار گیرد .
در طول دهه ۱۹۵۰ نت پیشگیرانه به تدریج تکامل یافته تا پاسخگوی نیازهای جدید صنعت باشد . در این راستا سیستم نگهداری و تعمیرات بهرهور(Productive Maintenance) در سال ۱۹۵۴ به صنایع آمریکا معرفی گردید . در این سیستم ضمن تاکید بر روی اصلاح خرابیهای اتفاقی و از کار افتادن غیرمنتظره تجهیزات با بهرهگیری مناسب از علوم آمار و احتمالات و پژوهش عملیاتی ، شبیهسازی ، اقتصاد مهندسی ، تئوری صف و نگرشهای تحلیلی ، تکنیکها و مدلهایی برای حالات مختلف انواع دستگاهها و تجهیزات ابداع شد که متخصصین این رشته میتوانستند کلیه فعالیتها و عملیات نگهداری و تعمیرات را به نظم درآورده و خرابیها را پیشبینی نمایند تا جهت نگهداری و تعمیر آنها برنامهریزی انجام پذیرد .
دهه ۱۹۶۰ را میتوان دهه گسترش استفاده از نت بهرهور در صنایع نامید . معرفی نت بینیاز از تعمیر ، مهندسی قابلیت اطمینان و مهندسی قابلیت تعمیر (۱۹۶۲) از نتایج تحقیقات انجام شده در این دهه بوده که در تکامل سیستم نت بهرهور بسیار موثر بوده است .
معرفی سیستم نگهداری و تعمیرات بهرهور فراگیر (Total Productive Maintenance) در دهه ۱۹۷۰ از سوی صنایع ژاپنی را میتوان بعنوان آخرین دستاورد در دوره دوم تحولات نگهداری و تعمیرات نامید . سیستم TPM در حقیقت همان سیستم نت بهرهور به شیوه آمریکایی است که در جهت سازگاری با شرایط صنعتی ژاپن در آن بهبودهایی داده شده است ؛ ابتکار محوری و حساس در اصول TPM این است که اپراتورها خودشان به امور اصلی و اولیه نگهداری و تعمیرات ماشینهای خودشان میپردازند . در نت بهرهور فراگیر نتایج حاصل از فعالیتهای صنعتی و تجاری به صورت اعجابانگیزی بهبود یافته و سبب ایجاد یك محیط كاری با بهرهوری بالا ، شادیآفرین و ایمن با بهینهسازی روابط بین نیروی انسانی و تجهیزاتی كه با آن سر و كار دارند ، میگردد .
۳- دوره سوم و RCM :
میزان افزایش سرمایهگذاری بر روی ماشینآلات صنعتی و اتوماسیون از یکسو و افزایش ارزش مالی و اقتصادی آنها از سوی دیگر منجر به آن شد که مدیران و صاحبان صنایع به فکر راهکارهایی منطقی بیفتند که قادر به بیشینهسازی طول عمر مفید تجهیزات تولیدی و طولانی کردن چرخه عمر اقتصادی آنها باشد . افزایش میزان اثربخشی ماشینآلات ، بهبود کیفیت محصولات در کنار کاهش هزینههای نت و عدم خسارت به محیط زیست از جمله مواردی بود که باعث ایجاد تحولی جدید در زمینه نگهداری و تعمیرات گردید .
دستآوردهای جدید نت در این دوره عبارتند از :
۳-۱- معرفی سیستم نگهداری و تعمیرات بر پایه شرایط کارکرد ماشینآلات (Reliability Centered Maintenance) و ترویج استفاده از روشهای CM همچون آنالیز لرزش ، حرارتسنجی و ...
۳-۲- معرفی و بکارگیری انواع روشهای تجزیه و تحلیل خرابیهای ماشینآلات .
۳-۳- طراحی تجهیزات با تاکید بیشتر بر قابلیت اطمینان و قابلیت تعمیر .
۳-۴- تحول اساسی در تفکر سازمانی به سمت مشارکت و گروههای کاری .
۳-۵- معرفی سیستم نگهداری و تعمیرات موثر .
۳-۶- معرفی روش نت مبتنی بر قابلیت اطمینان به عنوان روشی جامع جهت تصمیمگیری در استفاده صحیح از انواع سیستمهای نگهداری و تعمیرات موجود ؛ RCM فرایندی است که اولا معین میکند چه کاری میبایست برای تداوم عمر هر گونه سرمایه فیزیکی انجام شود و دوم آنكه انتظارتی را که کاربران از تجهیزات دارند ، عملی مینماید .
●سیستم نگهداری و تعمیرات واكنشی (Reactive Maintenance)
در گام پیشین ، در بیان تاریخچه تحولات نت ، از سیستمهای گوناگون نت كه در دورههای زمانی متفاوت مورد استفاده قرار میگرفتهاند سخن گفتیم ؛ در این گام و گامهای آتی به تشریح بیشتر این استراتژیها خواهیم پرداخت .
از نگهداری و تعمیرات واكنشی (Reactive Maintenance)آغاز مینماییم :
این استراتژی میگوید :(Fix it after it Breaks)
در این روش بعد از وقوع خرابی نسبت به تعمیر ماشین و بازگشت وضعیت به حالت اولیه اقدام میگردد .
در استاندارد TPMاز این روش با عنوان (Breakdown Maintenance) یاد شده و در ایران نیز عنوان (Emergency Maintenance) برای این روش مورد استفاده قرار میگیرد .
همانگونه كه در گام پیشین بیان نمودیم این سیستم در سالهای آغازین تكامل نت مورد استفاده قرار میگرفته و بدین سبب با ساختار امروزین ماشینآلات و تجهیزات همخوانی چندانی نداشته و معایب زیر را با خود به همراه دارد :
۱- كاهش ایمنی کار با ماشینآلات .
۲- عدم برنامهریزی دقیق تولید به علت بروز مشکلات کمی و کیفی .
۳- نیاز به گروه تعمیراتی قوی و آماده به کار .
۴- افزایش زمان تعمیرات بعلت مشاهده خرابیهای فرعی .
۵- نیاز به ذخیره و انبار کردن وسیع قطعات .●نهداری و تعمیرات پیشگیرانه (Preventive Maintenance)
این استراتژی میگوید :(Fix it before it breaks)
Maintain based upon calendar or running time
نگهداری و تعمیرات پیشگیرانه عبارتست از یك روش سیستماتیک برنامهریزی و زمانبندی شده جهت انجام کارهای نگهداری مورد نیاز بر طبق برنامه تنظیمی با هدف جلوگیری از فرسایش غیرعادی اجزا ماشین و کاهش توقفات اضطراری ماشینآلات .نت پیشگیرانه بر اساس تناوب اجرای فعالیتها برنامهریزی و اجرا گردیده و به همین دلیل عبارت Time Based Maintenance نیز به این دسته از فعالیتها اطلاق میگردد .
فعالیتهای نت پیشگیرانه عبارتند از :
۱- جلوگیری از فرسایش غیرعادی اجزاء ماشین : نظافت ، آچارکشی و روانسازی (روغنکاری و گریسکاری)
۲- کاهش توقفات اضطراری : تعمیر و تعویضهای دورهای مطابق با برنامه زمانی از پیش تعیین شده .
●نگهداری و تعمیرات پیشگویانه(Predictive Maintenance)
Maintain based upon known condition
نت پیشگویانه به مجموعه فعالیتهایی اطلاق میگردد که جهت تعیین شرایط فنی کارکرد اجزاء ماشین (اندازهگیری میزان فرسایش اجزاء) در حین بهرهبرداری انجام گردیده و بر اساس نتایج حاصله از آن ، زمان و نوع فعالیت نت مورد نیاز تعیین میگردد .
نت پیشگویانه بر اساس شرایط کارکرد اجزاء ماشین برنامهریزی و اجرا گردیده و به همین دلیل عبارت Condition Based Maintenance نیز به این دسته از فعالیتها اطلاق میگردد .
فعالیتهای نت پیشگویانه(PdM) عبارتند از :
۱- بازرسی فنی توسط حواس انسانی : انجام بازرسی فنی توسط پرسنل ماهر نت با استفاده از حواس انسانی (همچون بازرسی سر و صدای غیرعادی یا گرم شدن بیش از حد اجزاء)
۲- اندازهگیری فرسایش با استفاده از ابزار توسط انسان : بازرسی فنی اجزاء ماشین و اندازهگیری فرسایش با استفاده از ابزارهایی همچون ارتعاشسنج ، حرارتسنج ، آنالایزر روغن . در این روش بازرس PM در فواصل زمانی مشخص و در حین کارکرد ماشین با استفاده از ابزار نسبت به اندازهگیری میزان فرسایش اجزاء اقدام و نتایج به دست آمده را با محدوده کارکرد مجاز اجزاء مقایسه مینماید . تصمیم جهت ادامه کار ماشین و یا توقف آن جهت انجام فعالیتهای نت بر اساس نتایج حاصله از این تحلیل خواهد بود . در این روش هیچ فعالیت اضافی نت انجام نمیگیرد و برهمین اساس عبارت نت اقتصادی نیز به این گروه از فعالیتهای نت اطلاق میگردد .
۳- بازرسی و اندازهگیری پیوسته توسط ابزار : امروزه استفاده از روش کنترل پیوسته توسط طراحان ماشینهای صنعتی به عنوان روشی جهت جلوگیری از خطاهای برنامهریزی نت مورد توجه قرار گرفته است . فیلترهای هوا مجهز به سنسور هایی جهت تعیین زمان دقیق تعویض فیلتر شدهاند ؛ برای یاتاقانها سنسورهای حرارتی طراحی گردیده تا زمان دقیق روانسازی آنها مشخص و به اپراتورها اعلام گردد و ... .
●نگهداری و تعمیرات موثر (Proactive Maintenance)
این استراتژی میگوید :(Don’t just fix it, improve it)
Eliminate defects from all sources; Maximize equipment uptime
نت موثر به مجموعه فعالیتهایی اطلاق میگردد که با هدف بهبود وضعیت کارکرد ماشینآلات ، کاهش میزان نیاز آنها به اجرای نت و حذف کامل علل وقوع خرابیها انجام میگیرد .
در استاندارد نگهداری و تعمیرات بهرهور فراگیر (TPM) که از سوی انجمن مهندسین نت ژاپن تدوین گردیده عبارت (Maintenance Prevention) برای نت موثر استفاده گردیده است .
مهمترین روشهای تحلیلی مورد استفاده در سیستم نگهداری و تعمیرات موثر عبارتند از :
RCA : Root Cause Analysis &MFMEA : Machine Failure Mode and Effects Analysis
فعالیتهای نت موثر عبارتند از :
۱- انتخاب ماشینآلات و تجهیزات و یا تغییر در نحوه استفاده از آنها بر اساس سوابق نت وتجربیات پرسنل نت و تولید .
۲- طراحی مجدد اجزاء ماشین با هدف حذف علل وقوع خرابیها .
۳- بازنگری در طراحی ، نصب و نحوه بهرهبرداری از تجهیزات .
●نگهداری و تعمیرات بهرهور فراگیر (Total Productive Maintenance)
همانگونه كه در گامهای پیشین اشاره نمودیم سیستم TPM در حقیقت همان سیستم نت بهرهور به شیوه آمریکایی (كه در سال ۱۹۵۴ معرفی شد) است که در جهت سازگاری با شرایط صنعتی ژاپن در آن بهبودهایی داده شده است ؛ ابتکار محوری و حساس در اصول TPM این است که اپراتورها خودشان به امور اصلی و اولیه نگهداری و تعمیرات ماشینهای خودشان میپردازند . در نت بهرهور فراگیر نتایج حاصل از فعالیتهای صنعتی و تجاری به صورت اعجابانگیزی بهبود یافته و سبب ایجاد یك محیط كاری با بهرهوری بالا ، شادیآفرین و ایمن با بهینهسازی روابط بین نیروی انسانی و تجهیزاتی كه با آن سر و كار دارند ، میگردد .
از زمانیکه اولین اسناد در زمینه سیستم نت بهرهور جامع (TPM) ارائه گردید بیش از سی سال میگذرد . نسخه اول سیستم TPM به مدل Nakajima (از بنیانگذارانTPM ) مشهور بوده و تا سال ۱۹۸۹ نیز در اصول پنجگانه آن تغییری داده نشد .
با تغییر نگرش در سیاستهای کلان TPM ، ویرایش دوم و سوم سیستم مذکور در طول سالهای ۱۹۸۹ تا ۱۹۹۴ توسطT. Suzuki ارائه گردیده که یکی از ویژگیهای مهم ویرایش سوم افزایش اصول سیستم به هشت اصل زیر میباشد :
۱- افزایش میزان اثربخشی کلی ماشینآلات .
۲- اجرای نت خودکنترلی توسط پرسنل خطوط تولید .
۳- اجرای نت برنامهریزی شده توسط بخش نگهداری و تعمیرات .
۴- برگزاری دورههای آموزش تئوری و عملی برای کلیه پرسنل .
۵- مدیریت زودهنگام بر روی ماشینآلات .
۶- استقرار سیستم نت کیفیتی با ایجاد ارتباط بین واحدهای نت و کنترل کیفیت .
۷- استقرار نت بهرهور فراگیر در واحدهای پشتیبانی و ستادی نت .
۸- مدیریت ایمنی و محیط زیست .
منبع : پایگاه جامع مهندسی صنایع ایران
ایران مسعود پزشکیان دولت چهاردهم پزشکیان مجلس شورای اسلامی محمدرضا عارف دولت مجلس کابینه دولت چهاردهم اسماعیل هنیه کابینه پزشکیان محمدجواد ظریف
پیاده روی اربعین تهران عراق پلیس تصادف هواشناسی شهرداری تهران سرقت بازنشستگان قتل آموزش و پرورش دستگیری
ایران خودرو خودرو وام قیمت طلا قیمت دلار قیمت خودرو بانک مرکزی برق بازار خودرو بورس بازار سرمایه قیمت سکه
میراث فرهنگی میدان آزادی سینما رهبر انقلاب بیتا فرهی وزارت فرهنگ و ارشاد اسلامی سینمای ایران تلویزیون کتاب تئاتر موسیقی
وزارت علوم تحقیقات و فناوری آزمون
رژیم صهیونیستی غزه روسیه حماس آمریکا فلسطین جنگ غزه اوکراین حزب الله لبنان دونالد ترامپ طوفان الاقصی ترکیه
پرسپولیس فوتبال ذوب آهن لیگ برتر استقلال لیگ برتر ایران المپیک المپیک 2024 پاریس رئال مادرید لیگ برتر فوتبال ایران مهدی تاج باشگاه پرسپولیس
هوش مصنوعی فناوری سامسونگ ایلان ماسک گوگل تلگرام گوشی ستار هاشمی مریخ روزنامه
فشار خون آلزایمر رژیم غذایی مغز دیابت چاقی افسردگی سلامت پوست