جمعه, ۱۲ بهمن, ۱۴۰۳ / 31 January, 2025
شهر تویوتا
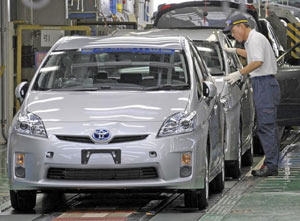
کارخانه تویوتا در جورجتاون کنتاکی، بزرگترین واحد در نوع خود در خارج از ژاپن و اولین آن در امریکا است. در این نوشتار، «مایک بوتکین» مدیر کارخانه/ لجستیک و کنترل تولید، در مورد لجستیک ناب، مدیریت خط تولید و حداکثرسازی بهرهوری با ایجاد جریان پرتناوب۱ مواد، اطلاعات مفیدی ارائه کرده است.
فرایند لجستیک رو به درون۲ ناظر به حفظ جریان هموار موادی است که پاسخگوی نیازمندیهای خط تولید باشد و اجرای آن در وضعیتی با هزینهکرد مؤثر، انجام گیرد. تویوتا یکی از پیشگامان صنعت در این نوع لجستیک ناب است؛ نوعی استراتژی که متأثر از نیاز به کاهش موجودی، زمان و هزینه در زنجیره تأمین خودروسازی است.
یکی از موضوعات کلیدی، استفاده از فضا در بالاترین بازدهی ممکن، با حداقلسازی موجودی و حداکثرسازی خروجی است. تویوتا طی چند سال گذشته در امریکای شمالی از مبحث کراس داکینگ۳ برای تجمیع۴ و یکپارچهسازی ظرفیتهای لجستیک رو به داخل استفاده کرد که به ایجاد جریان هموار و متناوب مواد با حداکثر بازدهی انجامید. در کارخانه تویوتا کنتاکی (TMMK)۵ بزرگترین کارخانه در شمال امریکا، موضوع کراس داکینگ در کنار دیگر فرایندهای صرفهجویی فضا از جمله بستهبندی و طبقهبندی قطعات وارده، مدنظر قرار گرفت. کارخانه جرج تاون، با جریان رو به داخل مواد سروکار داشت که شامل ۵۳۵ تریلر در روز میشد. نتایج حاصل از این کار، تویوتا را قادر میساخت تا به منظور کاهش زمان انتظار و موجودی، دفعات حمل را بهینه سازد.
● کنترل لجستیک
TMMK برای برخورداری از تحویلهای بموقع، از خدمات شرکتهای سرویسدهنده لجستیک معروف به ۳PL۶ استفاده میکرد. شرکتهای Ryder و Transfreight یکی از اولین خدمتدهندگان لجستیکی به تویوتا هستند. مایک بوتکین مدیر کارخانه، لجستیک و کنترل تولید در بخش تولید و مهندسی در شرکت تویوتای امریکای شمالی (TEMA)۷، عملیات لجستیک رو به داخل در TMMK را رهبری میکند. او میگوید شرکتهای ۳PL علاوه بر ایجاد شرایط مناسب برای تحویلهای بموقع، مسئولیت تایید سفارشات از طریق مقایسه اظهارنامه با مقدار واقعی را نیز بر عهده دارند. ۳PL میبایستی مطمئن شود که سفارش درخواستی مشتری، بارگیری شده و هرگونه عدم انطباقی را به کارخانه گزارش کند.
بوتکین میگوید: «تویوتا بهطور میانگین، ۴ ساعت موجودی نگه میدارد و برای حفظ این سطح موجودی، باید برنامهریزی بسیار دقیقی در خصوص مسیر و زمان ورود، داشته باشیم. تنها در این صورت است که میتوانیم از یک سو خدمتدهی را در شرایط مطلوب حفظ کنیم و از سوی دیگر هزینهها را کاهش دهیم».
● یکپارچگی از طریق کراس داکینگ
TMMK از ۲ روش لجستیک رو به داخل کمک میگیرد که هر یک برای نیمی از حجم قطعات مورد استفاده قرار میگیرد. اولین روش، شبکه یکپارچه است. شبکهای شامل یک سیستم کراسداک که در کارخانه جرج تاون واقع شده و در آن، قطعات تولیدی مورد نیاز کارخانههای متعدد تویوتا در امریکا، تحت مدیریت قرار میگیرند.
بوتکین میگوید یکی از تغییرات اصلی در TMMK، پیادهسازی کراسداکها بوده که از آنها برای ایجاد جریانی هموارتر استفاده شده است. او میگوید: «از جمله مزایای مهم کراس داکینگ، کاهش هزینههای موجود و نیروی کار، و توانایی برای حفظ جریان هموار و متناوب مواد است. بر مبنای چنین کاربردی، حدود ۲ تا ۳ سال است که از کراس داکینگ استفاده میکنیم. همچنین ۱۰ سال است که از شبکه یکپارچه و کراسداک، برای تجمیع محمولههای کمحجم استفاده میکنیم».
سیستم کراسداک در TMMK برای تحویل محمولهها به کارخانهها، از برنامهریزی مبتنی بر سفارش استفاده میکند و سفارشات بر مبنای برنامه زمانبندی تولید، از کراسداک کشیده میشوند.
بوتکین توضیح میدهد: «برخی قطعات، مستقیماً به کنار خط میروند. ما آن دسته از قطعاتی را که مستقیماً به کنار خط نمیروند، جداسازی و انبارش کرده و آنها را در قالب اندازه دستههایی کوچکتر، به کنار خط تولید میآوریم. ما، سفارش قطعات در شبکه یکپارچه را در اندازه دستههایی در حجم پالت جدا کرده و آنها را مطابق با چرخه تحویل، جداسازی و انبارش میکنیم. مبنای اولویتبندی، ظرفیت فضای کنار خط است».
● اهداف لجستیک رو به داخل
TMMK علاوه بر سازماندهی مستقیم میلکرانها، تمامی محمولههای لجستیک رو به داخل را با کامیون به کارخانه انتقال میدهد. با اینکه قطعات از طریق شبکهای یکپارچه حمل میشوند، شرکت برای بهینهسازی جریان کنار خط، از میلکران نیز استفاده میکند.
تأمینکنندگان کارخانه در ۳ گروه کالا تقسیمبندی میشوند: لاستیک خودرو و چرخها، تزئینات درب و صندلیها، بوتکین میگوید اکثر محمولههایی که مستقیماً به کنار خط میروند، حجیم هستند. او توضیح میدهد که ذخیره موجودی، یا مستقیماً فضایی را در کنار خط تولید اشغال میکنند و یا محمولههایی هستند که قبل از ایستگاه مونتاژ، به محموله با اندازه دستههای کوچکتر تقسیم میشوند و تویوتا آنها را بر حسب خودرو وارده به خط مونتاژ آماده کرده و به ترتیب، به کنار خط میآورد.
مایک بوتکین درباره استراتژی لجستیک رو به داخل میگوید: « TMMK اهداف لجستیک رو به داخل خود را بر مرحلهای خاص از توسعه خودرو، بنا مینهد. در تغییرات مدل اصلی، اهداف ما درگیر شدن در تحقیقات اولیه، برنامهریزی رویدادهای اصلی، شناخت فرایندها و تعیین نوع پالتها برای بهینهسازی کارایی است.»
بعد از شروع به کار تولید خودرو، تمرکز کار معطوف به برنامهریزی مسیر خواهد بود. اگر قطعاتی منحصر بفرد و یا بزرگ وجود داشته باشند، سعی میشود تا آنها را از منبعی نزدیک، تأمین کنیم. هدف از این کار، حداکثرسازی تعداد دفعات ارسال محموله است. با این کار، کارامدی لجستیک داخلی نیز مورد پشتیبانی قرار میگیرد. برای انجام این کار، تویوتا باید توجه خود را به یکپارچگی فرایند معطوف کند. بوتکین میگوید: «ما ۱۲ سفارش تولید ماهانه داریم و نیاز به تغییرات برنامهریزی مسیر را بهطور ماهانه مورد ارزیابی قرار میدهیم. تغییرات دورهای ممکن است شامل تغییر در مسیر لجستیکی گروهی از تأمینکنندگان باشد که از مسیری در حال خدمتدهی به مسیری دیگر منتقل میشوند.» هدف از این کار مدیریت کارایی ناوگان حمل و از این مهمتر، مدیریت تغییرات ناشی از نوسانات در حجم تولید است».
هماهنگیهای داخلی در تویوتا نیز مهم است. بوتکین میگوید: «دفاتر مرکزی، برنامهریزی را انجام میدهند و TMMK با هدف یکپارچهسازی ارسال بارها، لجستیک خود را با دیگر کارخانههای تویوتا به اشتراک گذاشته است. تویوتا با هدف شناخت بهترین فعالیت در هر کارخانه، افراد را از دیگر کارخانههای خود به اینجا میآورد. نفرات تیم، شامل افرادی ماهر در حوزههایی همچون بستهبندی و برنامهریزی مسیر هستند. با هر پروژه جدید، بهبودهای لازم برای سرپرستی و نظارت در کارخانه انجام میگیرد».
بوتکین ادامه میدهد که: «ما سعی داریم به وضعیتی ساده برای لجستیک رو به داخل دست یابیم. دیگر شرکتها بر هزینه، تمرکز کردهاند و تویوتا این تلاش را برای مدلهای جدید، معطوف به شناسایی فرایند، بستهبندی، لجستیک داخلی و لجستیک خارجی کرده است. هدف این است که برای دستیابی به شرایط بهینه کنار خط و حداکثرسازی کارایی هزینه، تلاش کنیم.»
ویژگی TMMK در عواملی همچون کاراسازی سیستمهای خود برای بهینهسازی دفعات حمل و پشتیبانی از زمانهای انتظار داخلی و شرایط کنار خط است. بر اساس اظهارات بوتکین، تعداد دفعات حمل برای تویوتا مهم است. زیرا این شرکت، موجودی زیادی را نگه نمیدارد. «اساساً، ما قطعات را ابتدا از تأمینکنندگان به کراسداک جورجتاون حمل میکنیم و سپس به کنار خط میبریم».
وضعیت جدید، بیانگر بهبود سیستم قبلی است. بوتکین میگوید تویوتا در گذشته، دریافتهایی مستقیم از سازنده داشت که بهطور میانگین، ۴ بار در روز انجام میشد. در کارخانه، این قطعات در فلوراکها۸ ذخیره میشدند. سپس، سیستم کانبان۹ قطعات را انتخاب میکرد و آنها را به کنار خط میآورد.
تویوتا بهطور میانگین، چهار ساعت موجودی نگه میدارد. برای حفظ این سطح موجودی، میبایست برنامهریزی بسیار دقیقی برای مسیر و زمان ورود داشته باشیم. با انجام این کار، میتوانیم در حالی که خدمتدهی را در همان شرایط مطلوب حفظ کردهایم هزینهها را نیز حداقل کنیم. مایک بوتکین - تویوتا مشکل این بود که کم بودن دفعات ارسال، شرایطی را ایجاد میکرد که نیاز به ذخیرهسازی موجودی بود. هماکنون و مطابق با سیستم کایزن فعال در کارخانه، TMMK از یک کراسداک در سایت کارخانه استفاده میکند که دفعات ارسال آن ۲۴ بار در روز است.
در کراسداک، TMMK از طریق مسیر تحویلهای داخلی که در نظر گرفته، قطعات را در خطوط جداگانه، تفکیک و انبارش میکند. هر خط، بیانگر تولید برای تعدادی مشخص شده از خودروی نهایی است. در کارخانه و طی هر نوبت، حجمی از مواد به ارزش ۴۰ دقیقه تولید، به خطوط تغذیه میشود. ۴۰ دقیقه ضربدر ۲۴ نوبت تغذیه در روز برابر است با ۱۶ ساعت کاری یا دو نوبت کاری کامل.
● استانداردها و انتظارات
بوتیکن میگوید واحد سفارشات و سیستم لجستیک TMMK، ارتباط کاری نزدیکی با یکدیگر دارند. وی میگوید: «این مهم است که استانداردها و انتظارات کاری روشن و واضحی داشته باشیم. وظیفه مدیریت مواد، استانداردسازی و کنترل عملیات است. ما در این زمینه، بهبودهای بسیار زیادی در کنار خط داشتهایم. TMMK با تبعیت از شیوه «Plan, Do, Check»، از شاخصهای عملکرد کلیدی (KPIs) برای اندازهگیری رخدادهای غیرعادی در فرایند استفاده میکند.
وجود کراسداک در سایت، به این معناست که TMMK انبار ندارد. TMMK قطعات کراسداک را حداکثر به مدت ۱۲ ساعت نگه میدارد و آنها را دو بار در روز تحویل میدهد.
● ایجاد یک شبکه تأمین
یکی از بزرگترین چالشهای TMMK برخورداری از حمل بهینه است. مورد دیگر، جبران هزینههای سوخت حملونقل است. بوتکین میگوید: «سوال این است که چه عواملی میتوانند باعث کاهش هزینهها شوند، به این شرط که اهداف خدمتدهی خود را زیر پا نگذاریم. در عین حال باید مطمئن باشیم که شرکای زنجیره تامین ما نیز از کارایی لازم برخوردارند. این بخشی از هدف ما در بهبود مستمر است.»
رشد تولید خودرو در امریکای جنوبی و مکزیک، بر سیستم لجستیک رو به داخل تویوتا تأثیر گذاشته است. بوتکین به این نکته اشاره دارد که وضعیت تأمینکننده در ژاپن، در مقایسه با امریکا متفاوت است. در ژاپن، تأمینکنندگان در مکانی نزدیکتر به کارخانه مستقر هستند.
موقعیت و وضعیت تأمینکنندگان در میان کارخانههای تویوتا در امریکای شمالی نیز با هم متفاوت است. او توضیح میدهد: «پایگاههای تأمین، از مرکز امریکا دور شدهاند. کارخانه ما در سن آنتونیو، یک پارک تأمین دارند. کارخانه ما در «تی جوانای» مکزیک، دچار چالشهایی در خصوص لجستیک رو به خارج پالتهای برگشتپذیر دارد که ناشی از محدودیتهای ساختاری است».
دیگر کارخانه تویوتا به نام NUMMI۱۰، که همکاری مشترک تویوتا و جنرال موتور در فرمونت کالیفرنیاست، از راهآهن برای حمل رو به داخل استفاده میکند. بوتکین میگوید: «تویوتا به دنبال استفاده بیشتر از حملونقل ریلی برای مکزیک است، اما دسترسی به زیرساختار در خارج، بسادگی اینجا نیست. بعلاوه، کارخانههای NUMMI و کانادا، نیازهای بستهبندی منحصربفردی برای تأمینکنندگان خود دارند.»
وی ادامه میدهد: کارخانه TUPELO لایه پیچیده دیگری را به سیستم لجستیک اضافه کرده است. ما برای کارخانه جدید خود، بهترین عملکردها را بررسی کرده و احتمالاتی شامل تأمینکنندگان در محل یا کراسداکهای در درون سایت را مدنظر قرار میدهیم. در نظر گرفتن امکانات در درون سایت، میتواند بهترین انتخاب برای بهینهسازی لجستیک رو به درون باشد.
● راهحلهای انبارش
توسعه کراسداکینگ در تویوتا، با هدف پشتیبانی از منطق استفاده هرچه بهتر از فضای کارخانه، صورت میگرفت. بوتکین میگوید: «فضا به چیزی کمیاب تبدیل شده است. لذا تویوتا به دنبال گزینههایی برای انبارش بارهای حجیم است. این همان منطقی است که از آن برای پالتبندی قطعات استفاده میشد؛ طبقهبندی بر اساس سفارش و کنترل روند تحویل. ما نسبت به روش قبلی، در فضای مورد نیاز صرفهجویی کردهایم چون هر قفسهای دارای آدرسدهی انبارش منحصربفردی است.»
تویوتا برای استفاده بهتر از فضا، بهبود در بستهبندی را مدنظر دارد. بوتکین میگوید با اینکه بستهبندی تویوتا سبکتر شده، اما هنوز هم مستحکم و بادوام است: «ما برای بهبود قابلیت شکلپذیری و حداقل کردن هزینه بستهبندی، سرگرم استانداردسازی بستهبندی هستیم».
بوتکین به این موضوع اشاره میکند که با توجه به دفعات بالای ارسال محموله، پالتها دیگر پر نیستند. لذا، سوال این است که چگونه کاربری پالت را به حداکثر برسانیم و هنوز هم از دفعات حمل کنار خط مطمئن باشیم.
بهبود کارایی لجستیک در TMMK امری تدریجی است. بوتکین میگوید: «در هر ۵ سال، تغییرات بزرگی رخ میدهد، اما تغییرات کوچک از فلسفه کایزن تبعیت کرده و طی این مدت، تجمیع میشوند».
تغییری دیگر در TMMK، مربوط به میلههای تقویت پالت بود. بوتکین میگوید مشکلی در بستهبندی وجود داشت که ناشی از شکل خاص آنها بود. در وضعیت اولیه، قرارگیری ۶ قطعه در هر پالت مدنظر بود. با این وجود، تویوتا قطعات را بهگونهای منظم کرد که بدون تغییر در شکل اولیه پالت، میشد تا ۱۲ قطعه را در پالت قرار داد. بهبود دیگر، ناشی از نیازمندیهای فضای کنار خط بود. بوتکین میگوید جعبههای قطعات کوچک، فضای کنار خط را اشغال میکردند. لذا، سال گذشته قفسههای خود تغذیه را نصب کردیم و قطعات را روی آنها قرار دادیم. به این ترتیب، دیگر نیازی به قرار دادن جعبهها در پشت قفسه نبود.
هدف کارخانه تویوتا در میسیسیپی، کاربری بهتر از تسهیلات درون سایت است. این پروژه در تابستان سال جاری اجرا میشود و تویوتا در نظر دارد با بررسی شرایط موجود مسیر لجستیکی کراسداک تا کارخانه، حملونقل را حذف کند.
TMMK با حفظ جریان کارای مواد، کماکان بر بهینهسازی کارایی خطوط تولید تمرکز دارد. این کار به حفظ جریان متناوب رو به داخل و کاهش موجودی از طریق سیستم کراسداک کمک میکند. تویوتا به واسطه کراسداک و دیگر بهبودهای تدریجی، در صدد حداکثر کردن استفاده از فضا و دستیابی به یک شبکه لجستیک رو به داخل کارامد است.
● کارخانه تویوتا موتور در کنتاکی (TMMK)
کل فضای سایت: ۷.۵ میلیون فوت مربع. بزرگترین کارخانه تویوتا در خارج از ژاپن
سرمایه فعلی: ۵.۴۹ میلیارد دلار با پرداخت حقوق سالانه ۵۲۶ میلیون دلار برای چیزی نزدیک به ۷۰۰۰ نفر نیروی تحت استخدام
عملیات اجرایی در این کارخانه شامل پرسکاری، قالبسازی، جوشکاری بدنه، رنگ، پلاستیک، مونتاژ، ماشینکاری اکسل و مونتاژ است.
این کارخانه در سال ۲۰۰۶ در حدود ۵۰۰ هزار خودرو شامل مدلهای کمری، آوالون، کمری سولارا و کمری هیبرید، تولید کرده است. همچنین، موتورهای ۴ و ۶ سیلندر خطی V۶ (۵۰۰.۰۰۰ عدد در سال)، اکسل، اجزای فرمان، بلوک سیلندرهای ماشینکاری شده، سرسیلندر، میللنگ، میلبادامک را نیز تولید میکند.
قطعات داخلی چیزی در حدود ۹۷ درصد از حجم لجستیک رو به داخل این کارخانه را شامل میشوند. این کارخانه روزانه حدود ۲۴ هزار مترمکعب قطعات داخلی و حدود ۱۰۰۰ مترمکعب قطعات تحت عنوان محمولههای بینالمللی از ژاپن دریافت میکند.
شرکت تویوتا موتور در سال ۲۰۰۶، حدود ۲.۹۴ میلیون خودرو در امریکای شمالی فروخته که نشاندهنده افزایش ۳۸۶ هزار عددی (یا بیش از ۱۳ درصدی) نسبت به سال ۲۰۰۵ است.
واحد مهندسی و تولید تویوتا در امریکا شمالی (TEMA) واقع در شهر ارلنگر ایالت کنتاکی، دفتر منطقهای است برای تولید، توسعه خودرو، طراحی مهندسی و تحقیقات پیشرفته.
سیدعبدالرضا عظیمی (امور لجستیک شرکت ساپکو)
پانوشت
۱ . در جریان متناوب مواد، سعی میگردد تا مواد و قطعات در دفعات بالا (Hight-Frequency) و در اندازه دستههای کم به ایستگاههای تولید انتقال یابند.
۲ . Inbound Logistics
۳. Cross Docking نوعی انبار که معمولاً اقلام بیشتر از ۱۲ ساعت در آنجا منتظر نمیمانند و بسرعت برای ارسال به مقاصد آماده میگردند.
۴ . Consolidate
۵ . Toyota Motor Manufacturing Kentucky
۶ .Third Party Logistics (۳PLs)
۷ . Toyota Motor Engineering & Manufacturing North America (TEMA)
۸ . نوعی قفسهبندی که با توجه به شیب آن، قطعات از یک سمت تغذیه میشوند و از سمت دیگر برداشته میشوند. مشابه قفسههای خود تغذیه در خطوط تولید که متضمن اجرای FIFO نیز هستند.
۹. KANBAN
۱۰ . New United Motor Manufacturing
منبع
Automotive Logestics Magazine
ایران مسعود پزشکیان دولت چهاردهم پزشکیان مجلس شورای اسلامی محمدرضا عارف دولت مجلس کابینه دولت چهاردهم اسماعیل هنیه کابینه پزشکیان محمدجواد ظریف
پیاده روی اربعین تهران عراق پلیس تصادف هواشناسی شهرداری تهران سرقت بازنشستگان قتل آموزش و پرورش دستگیری
ایران خودرو خودرو وام قیمت طلا قیمت دلار قیمت خودرو بانک مرکزی برق بازار خودرو بورس بازار سرمایه قیمت سکه
میراث فرهنگی میدان آزادی سینما رهبر انقلاب بیتا فرهی وزارت فرهنگ و ارشاد اسلامی سینمای ایران تلویزیون کتاب تئاتر موسیقی
وزارت علوم تحقیقات و فناوری آزمون
رژیم صهیونیستی غزه روسیه حماس آمریکا فلسطین جنگ غزه اوکراین حزب الله لبنان دونالد ترامپ طوفان الاقصی ترکیه
پرسپولیس فوتبال ذوب آهن لیگ برتر استقلال لیگ برتر ایران المپیک المپیک 2024 پاریس رئال مادرید لیگ برتر فوتبال ایران مهدی تاج باشگاه پرسپولیس
هوش مصنوعی فناوری سامسونگ ایلان ماسک گوگل تلگرام گوشی ستار هاشمی مریخ روزنامه
فشار خون آلزایمر رژیم غذایی مغز دیابت چاقی افسردگی سلامت پوست