پنجشنبه, ۱۱ بهمن, ۱۴۰۳ / 30 January, 2025
مراحل شستشو در بازیافت
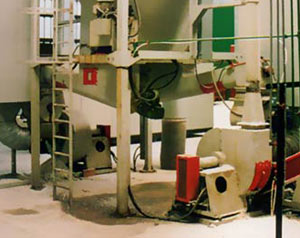
● مراحل کامل یک خط شستشو و پرک بطری های PET
پروسه تولید پرک از بطری های جمع آوری شده PET از راه های گوناگونی امکان پذیر است. امروزه شرکت های بسیاری در دنیا عنوان می کنند که تولید کننده و سازنده خط شستشو هستند اما انتخاب مناسب ترین خط شستشو مستلزم داشتن اطلاعات کافی از سازنده خط، دانش فنی او، سابقه و نوع تکنولوژِی به کار گرفته شده و همین طور نحوه کارکرد خط و طرز استفاده سازنده از آب و اینکه آیا صرفه جویی های لازم در ساخت دستگاه ها و همچنین تولید پرک انجام می شود یا خیر؟ علاوه بر این موارد بایستی اطلاع حاصل شود آیا سازنده از سیستم کنترل کیفیت پرک استفاده کرده است یا خیر؟
سیستم کنترل کیفیت پرک، فاکتور چشمگیر و قابل توجهی به حساب می آید که ارتباط مستقیم به نوع تجهیزات به کار رفته در مسیر و همچنین نیروی انسانی دارد. از این رو اغلب تولید کنندگان پرک سعی در استفاده از سیستم های کنترل کیفیت بسیار ارزان قیمت و فاقد کیفیت مناسب دارند. اما این سیاست چندان در بلند مدت قابل دوام نیست و دیر یا زود تولید کنندگان پرک با سیستم های کنترل کیفیت موثر و کار آمد آشنا می شوند و نسبت به استفاده از آنها ترغیب می شوند.
امروزه در دنیا تلاش های فراوانی در جهت تولید پرک با کیفیت ممتاز در حال شکل گیری است. به عنوان مثال در آلمان یک کنسرسیوم متشکل از اعضای داوطلبی از شرکت های خدماتی مرتبط به بازیافت PET گرد هم آمده اند تا کیفیت پرک را تضمین کنند و از این طریق رضایت مشتریان را با ارائه پرک با کیفیت مناسب، به دست آورند.
در بعضی نقاط دنیا حتی در کشور های پیشرفته دیده می شود خطوط خود ساخته شستشوی پرک به کار مشغول هستند. جاهایی که صاحبان کارخانه تجهیزات مختلف را از سازندگان گوناگون تهیه و خود آن ها را نصب کرده اند. اما دو موضوع مهم در این خط ها بسیار به چشم می خورد:
۱) آیا چنین خط هایی می توانند تولید کننده پرک با کیفیت قابل قبول باشند؟
۲) آیا در مصرف انرژی صرفه جویی لازم انجام می گیرد؟
تجربه نشان داده پاسخ هر دو سئوال منفی است.
یکی از شرکت های معتبر سازنده خطوط شستشوی پلاستیک که همواره در حال بهینه سازی خطوط خود و تولید پرک ممتاز است و با صرف هزینه های گوناگون افراد متخصص را در واحد R&D به کار می گیرد تا متناوباً خطوط شستشو با کیفیت ممتاز و صرف حد اقل انرژی مصرفی را به مشتریان خود عرضه نماید، شرکت SOREMA ایتالیا است.
شرکت SOREMA امروزه به عنوان معتبر ترین و بزرگترین سازنده خطوط تولید پرک در دنیا شناخته می شود که تا کنون بیش از ۷۵ نشان سبز محیط زیست کنترل کیفیت و نو آوری از مجامع صنعتی جهان برای خطوط خود دریافت نموده است. این شرکت با بیش از ۸۵ سال سابقه و با بهره گیری از ۲۷۰ پرسنل مجرب و واحد R&D بسیار فعال خود تا کنون موفق شده بیشترین خطوط تولید پرک و شستشوی پلاستیک را در بیش از ۹۵ کشور دنیا نصب و راه اندازی نماید.
در این مقاله برای آشنایی هر چه بیشتر علاقه مندان به این صنعت تمام مراحل تولید پرک PET یکی از خطوط تولید پرک شرکت SOREMA به طور مشروح بیان شده است.
۱) باز کردن عدل ها
پس از جمع آوری بطری ها، روش متداول به منظور صرفه جویی در هزینه های حمل و نقل، استفاده از پرس های عدل بندی است. در این مرحله بسته به نوع، اندازه و قدرت پرس، عدل هایی با وزن و ابعاد متفاوت تولید می شود. پس از رسیدن عدل ها به کارخانه تولید پرک، در اولین اقدام بایستی عدل ها به دقت توسط اپراتور باز شوند و با استفاده از یک سیکلون تمام بطری ها بایستی کاملاً از یکدیگر جدا شوند و روی تسمه نقاله قرار گیرند تا به راحتی بتوان آن ها را به صورت اتوماتیک سورت کرد.
در بعضی کشور ها دیده شده با استفاده از دستگاه بلوک سازی، بطری ها را به صورت بلوک هایی بسیار فشرده در می آورند. اما این بلوک ها کار را بسیار دشوار می سازند زیرا به راحتی اجازه جدا شدن بطری ها از یکدیگر را نمی دهند و در مراحل بعدی که دما بالاتر می رود از این بطری های به هم چسبیده، یک توده سنگین و غیر قابل تفکیک ایجاد می گردد.
۲) دسته بندی رنگی ها جدا سازی پلیمر های دیگر
یکی از نکات بسیار مهم در تشخیص کیفیت پرک مورد ادعای شرکت های سازنده خط تولید پرک، میزان وجود PVC در پرک خروجی است. وجود PVC در پرک می تواند موجب آسیب رسانی به دستگاه و اپراتور خط گرانول شود و همچنین اگر میزان PVC بیشتر از PPM۲۰ باشد، پرک تولید شده فاقد کیفیت محسوب می شود و در بازار فروش تولید کننده را با مشکل مواجه می سازد. شرکت SOREMA در تمامی خطوط خود و با توجه به میزان PVC در بطری های ورودی همواره میزان کمتر از PPM۲۰ را تضمین نموده است. و با توجه به بکار گیری جدا کننده های فوق العاده حساس و نمونه برداری های مداوم در طول پروسه تولید به راحتی خاطر مشتری را از بابت مشکل PVC آسوده کرده است.
برای به دست آوردن پرک خالص و همچنین جدا سازی PVC (کمتر از PPM۲۰ )، فلزات (کمتر از PPM۱۰)، (چسب کمتر از PPM۵۰ ) و آلومینیم (کمتر از PPM۲۵ ) بایستی تکنولوژی جدا سازی مناسبی را در اختیار داشته باشیم.
میزان دقت باید بسیار بالا باشد زیرا در عدل هایی که قبلاً هم سورت شده اند و میزان مواد غیر پلی استر در آنها کمتر از ۵% باشد، بایستی پالایش دقیق و سورتینگ مناسبی انجام شود.
بایستی تاکید کنم که سورتینگ در واقع کلید به دست آوردن پرک تمیز نهایی است.
جدا سازی دستی کمک خوبی به شمار می آید اما نمی تواند از دقت بالا تری نسبت به جدا کننده های تکنولوژیکی برخوردار باشد. زیرا جدا از اینکه بطری های PET همواره می توانند همراه بطری هایی از مواد دیگر مانند: PE، PP ، بطری های چند لایه، بطری های پوشش دار، بطری های متشکل از مواد مخلوط و بطری هایی با نواع افزودنی ها که تعدادشان هم کم نیست، باشند لذا تنها از طریق جداکننده هایی با تکنولوژی بالا قابل سورت شدن هستند.
در حالیکه حجم عظیمی از بطری ها، مانند سیل خروشان در ظرفیت هایی حد اقل از ۵۰۰ کیلوگرم در ساعت تا ۱۰ تن در ساعت روی نوار نقاله قرار می گیرند، جدا سازی بطری ها و تشخیص بطری های PET کار بسیار پیچیده و حساسی خواهد بود.
برای تشخیص انواع پلیمر های دیگر از PET و یا بطری های رنگی، مواد مخلوط دیگر، فرم ها و اجسام دیگر مانند کاغذ، شیشه و فلز، بایستی در ابتدای خط از سنسور های حساس استفاده شود تا کار جداسازی در مراحل بعدی به راحتی صورت پذیرد.
پایه و اساس تشخیص بطری ها بر مبنای ترکیب بطری های ورودی شکل می گیرد. شرکت SOREMA بر اساس آزمایش مقداری از بطری های ورودی که از هر مشتری دریافت می دارد و همچنین با تکیه بر تجربیات حرفه ای خود به شناخت کاملی از ترکیب بطری ها و میزان نسبتاً دقیق آلاینده ها می رسد. دست یابی به این شناخت یکی از ارزشمند ترین اطلاعات مورد نیاز SOREMA برای طراحی خط به شمار می رود. دو سازنده بسیار معتبر در دنیا به طور اختصاصی سامانه های تشخیص پلیمر ها از یکدیگر و یا تشخیص مواد دیگر از PET انجام می دهند و SOREMA همواره از این دو شرکت سامانه های تشخیص دهنده را تهیه می نماید.
با توجه به کیفیت تکنولوژی آنالیز و تشخیص مواد غیر از PET از بطری های PET این دو سازنده که یکی فرانسوی و دیگری ژاپنی می باشند، از تکنولوژی های بسیار به روز و کارآمدی در تجهیزات خود را استفاده می نمایند، اما همچنان دیده می شود تعدادی کارخانجات شستشو در دنیا که بی تفاوت نسبت به این تکنولوژی ها، هنوز کماکان از نیروی انسانی با تمام ضعفها در تشخیص و جداسازی مواد غیر از PET استفاده می کنند.
۳) پیش شستشو قبل از خرد کردن
بطری هایی که به طور مشخص کثیف هستند، زیرا از خیابان ها جمع آوری می شوند یا از مراکز تجمع شهرداری و یا از مراکز مشابه که عمدتاً آلوده به خاک- گل و شن (در بعضی کشور ها جمع کنندگان خیابانی متقلب برای نشان دادن وزن بیشتر عدل های بطری آنها را به خاک آلوده می کنند) بایستی در اولین مرحله حتماً شستشو شوند تا این آلودگی ها برطرف شوند.
در این مرحله ذرات شن و گل و لای روی سطح بطری ها گرفته و برطرف می شود که در مراحل خرد کردن باعث کندی تیغه ها و کوتاه شدن عمر تیغه ها نگردد.
۴) خرد کردن به اندازه های درشت - شستشو
در ادامه با قرار دادن یک خرد کن در مسیر، بطری ها در اندازه های نسبتاً درشت خرد می شوند. این کار به بر طرف نمودن لیبل بطری ها کمک فراوانی می کند. قبل از اینکه بطری ها با آب تماس داشته باشند به کمک دمش هوا اغلب لیبل ها در اثر فشار و مکش هوا الک می شوند. هدف اصلی از چنین عملکردی در واقع از بین بردن لیبل های کاغذی تا حد ممکن است، تا در مرحله تصفیه آب تبدیل به الیاف سلولزی نشوند و مشکلاتی را برای تصفیه بوجود نیاورند. این امکان وجود دارد که مرحله خرد کردن بطری ها با یک مرحله شستشو تلفیق شود. مزیت تلفیق این دو مرحله باعث می گردد ناخالصی ها به طور وسیع در آب حل و یا پراکنده شوند. در نتیجه این خرد و شستشو کردن اندازه پرک ها به طور متوسط بین ۱۰۰-۴۰ میلی متر خواهد بود.
۵) پاک کردن بطری ها از شن، شیشه و فلزات
بعد از مرحله خرد و شستشو کردن ضروری است بلافاصله تمام موادی مانند شن، شیشه و فلزات را بوسیله ترکیبی از سامانه فیلتراسیون صفحه ای و جداکننده گریز از مرکز که مجهز به جداکننده فلزات نیز هست، جدا کرد.
۶) جدا سازی فیلم- کاغذ و لیبل توسط یک الک با مکش هوا
جدا سازی از طریق مکش هوا بعد از اولین مرحله خردکردن و شستشو اولیه قرار می گیرد. در این مرحله سامانه های مختلفی مانند: الک زیگزاکی، چرخ های دوار و مرطوب سازی به کار می رود.
پروسه جدا سازی بدین صورت است که جریان هوا باعث می شود تکه های سنگین در اثر جاذبه به پایین می افتند و تکه های سبک تر بوسیله جریان هوای بسیار قوی به قسمت دیگری منتقل می شوند. موثرترین اقدام در زمانیکه جداسازی انجام می شود این است که ضربات پی در پی به سطح وارد شود تا در اثر تکان های مداوم قطعات سنگین و سبک کاغذ و پلیمر بهتر از یکدیگر جدا شوند.
اغلب خطوط شستشو به نحو بسیار مطلوبی از وجود دو الک یا تصفیه که با جریان هوا کار می کنند، سود می برند. یکی بعد از اولین خرد کن و دومی در انتهای خط به عنوان پاک سازی نهایی بعد از خشک کن.
۷) آسیاب خشک و مرطوب
در ادامه پروسه به دستگاه خردکن که قطعات خرد شده را تا اندازه ۳۰-۱۵ میلی متر برساند احتیاج است. عملکرد این خرد کن و آسیاب به صورت خشک و یا همراه آب صورت می پذیرد. اما با توجه به مزیت های کارکرد آسیاب مرطوب که باعث:
▪ حرکت عمیق و مواج پرک ها و آب در داخل آسیاب می شود؛
▪ افزایش عمر تیغه های آسیاب؛
▪ هدایت تمام آلودگی ها بوسیله جریان قوی آب در حرکت به سمت خروجی
لذا SOREMA همواره آسیاب مرطوب را به خاطر مزایای فوق و بهترین عملکرد در شستشو توصیه می نماید.
۸) جداسازی پلیمر های سبک تر (مثل درب های بطری و فیلم)
یکی از مهمترین مراحل کار تولید پرک، جداسازی پلیمرهای PP و PE است. وجود پلیمر PP به خاطر درب ها و درب بند های بطری های PET است و وجود پلیمر PE به خاطر فیلم های شرینک بسته بندی بطری ها است.
برای جدا سازی پلیمر های با چگالی سبک تر مثل PP وPE که چگالی آن ها ( ۹۵/۰-۸۵/۰ گرم / سانتی متر مکعب ) است از PET با چگالی سنگین تر ( ۱۰۴۴-۳۳/۱ گرم / سانتی متر مکعب) از روش شناور سازی در تانک آب استفاده می شود که بایستی در این قسمت قرار بگیرد.
پرک ها وارد تانک پر از آب می شوند به صورت پیوسته یا شاید به صورت بچ و پلیمر هایی با چگالی سبک تر بر روی آب شناور می مانند و بوسیله پره های دوار گردان از روی آب جمع می شوند. پلیمرهایی با چگالی سنگین تر رسوب کرده و ته نشین می شوند که بوسیله جریان آب خارج می شوند.
برای رسیدن به بالاترین حد اطمینان در جداسازی، می بایستی بوسیله افزودنی های مخصوص و یا با هم زدن متناوب با پارو تمام سطح پلیمر را مرطوب ساخت تا از چسبیدن احتمالی حباب های هوا به روی سطوح جلوگیری شود.
راه دیگری که برای جداسازی پلیمر های با چگالی سنگین از پلیمر های با چگالی سبک تر وجود دارد، به کار گیری هیدرو سیکلون است که می تواند گل و لای به جا مانده از آب را از پرک ها با حرکت دوار و سریع خود جدا نماید. اما به هر حال استفاده از تکنولوژی هیدرو سیکلون نمی تواند مناسب تر و موثر تر از جدا سازی از طریق تانک آب شناور باشد.
پروسه های متفاوت دیگر جداسازی از قبیل افزودن افزودنی- شناور سازی- جداسازی از طریق حلال های جذبی و یا ..... کمتر و به ندرت استفاده می شود، زیرا برطرف کردن افزودنی ها به افزایش هزینه پروسه می انجامد.
۹) شستشوی گرم- شستشو با کاستیک
یکی از آلودگی های استثنایی که به سطح پرک ها چسبیده، چسب لیبل ها است. جدا از تلاش مجدانه صنایع بسته بندی دنیا برای تعویض لیبل های چسبدار با فیلم های شرینک لیبل به خاطر مضرات چسب در پروسه شستشو، همچنان خیل عظیمی از بطری های دنیا با لیبل های چسب دار عرضه می شوند. آنچه موضوع چسب را در بحث شستشو مهم جلوه می دهد این است که ترکیب ساختار شیمیایی چسب ها بسیار متنوع و چند کاره هستند. شرکت SOREMA تا کنون با نمونه گیری های مختلف و تنوع مشتریان خود در سراسر جهان افزون بر ۱۱۰ نوع چسب لیبل بطری را شناسایی نموده که ساختار شیمیایی اغلب این چسب ها با یکدیگر متفاوت است. بنابر این برای برطرف کردن چسب های مختلف با ساختار شیمیایی متفاوت، بایستی از حلال های مناسب و مخصوص استفاده گردد.
تاثیر منفی وجود چسب در مراحل بعدی که تبدیل پرک به گرانول است، می تواند خود را نشان دهد. جایی که تخریب و نابودی پلیمرو رنگ را به همراه دارد. در نهایت به عنوان مواد غیر قابل حل در بین پرک ها باقی می مانند که باعث می گردد به شکل توده هایی در پشت فیلتر ها راه عبور از فیلتر ها را مسدود نمایند و باعث تجزیه و تخریب پلیمر ها شده و پدیده زرد رنگی پرک ها را باعث شوند. بنابراین برطرف کردن و زدودن چسب ها در خلال پروسه بسیار ضروری و اجتناب ناپذیر است.
بر اساس تجارب به دست آمده شرکت SOREMA به اثبات رسیده که شستشوی گرم پرک ها در دمای بین۹۰-۸۰ درجه سانتی گراد با استفاده از مواد پاک کننده و اسید های ارگانیک مانند اسید سیتریک و یا آلکالی مانند سدیم هیدروکسید، چسب تماماً از بین خواهد رفت.
گفتنی است شرکت های شیمی- مهندسی همواره بهترین توصیه را در خصوص مناسب ترین ترکیب شستشوی شیمیایی برای برطرف نمودن چسب ارائه می دهند.
شستشوی گرم همراه با کاستیک سودا که غلظت هیدروکسید سدیم در حدود ۵/۰% باشد و همینطور بعضی از پاک کننده ها نیز در آب مخلوط باشند، محلول بسیار مناسبی برای زدودن آرام و ملایم آلودگی ها از سطح پرک می باشد. شستشوی گرم به طور معمول به صورت بچ بچ انجام می شود و برای جداسازی محلول شستشو که حاوی مواد شوینده و آلاینده های جدا شده است از پرک ها، از وجود سانتریفیوژ های جدا کننده و یا روش های مبتنی بر وزن مخصوص استفاده می شود.
اهمیت برطرف کردن و از بین بردن چسب به قدری است که پرک شسته شده با وجود PPM۱۰ چسب به عنوان پرک ممتاز و تمیز در بازار شناخته می شود ولی حتی پرک شسته شده با داشتن PPM۴۰ چسب ، پرک خوبی به حساب نمی آید و به عنوان درجه دوم دسته بندی می شود. نحوه آزمایش نمونه پرک ها به منظور اطلاع از میزان وجود چسب بدین صورت است که نمونه ها را در دمای هوای گرم ۲۲۰ درجه سانتی گراد به مدت یک ساعت قرار می دهند. گرایش رنگ نمونه ها به زردی حاکی از وجود چسب بیشتر در پرک ها است که به همین علت در پروسه بعدی که تهیه گرانول است مشکلات فراوانی را به همراه خواهد داشت و همانطور که بیان شد حتی و جود PPM۳۰ چسب بیشتر باعث می شود پرک خوبی تولید نشود و کارکرد این پرک بسیار ضعیف قلمداد می شود. به طوریکه مصرف کنندگان رغبت خاصی برای خرید آن نشان نمی دهند.
۱۰) مرحله آبکشی
پس از پروسه جدا سازی چسب از سطح پرک ها احتیاج است با آبگیری مناسب نسبت به جداسازی کامل محلول حاوی شوینده هایی مثل: اسید ها و آلکالی ها از پرک ها اقدام شود. همچنین در این مرحله بایستی تا سرحد امکان نسبت به صرفه جویی در مصرف آب در هنگام آبگیری توجه کافی صورت پذیرد.
۱۱) آبکشی با آب تمیز
مصرف آب تمیز (سختی گیری آب) یون زدایی و بالاخره تجزیه ذرات آلی و طبیعی مانند: الیاف سلولزی پیش از هر چیز یک مساله کاملا اقتصادی قلمداد می شود.
زیرا تصفیه آب با استفاده از روش های مرسوم مانند: روش اسمزی یا روش عرق گیری به انرژی مصرفی فراوان نیازمند است. از سوی دیگر آب تمیزی که در اثر پروسه آبکشی و زدودن ناخالصی هایی یونی و ذرات بسیار ریز شناور به دست می آید از کیفیت و خلوص فوق العاده بالایی برخوردار خواهد بود. در هر صورت استفاده از سیستم تصفیه آب از سوی SOREMA برای داشتن آب تصفیه شده مناسب به صورت متعلقات خط شستشو و به عنوان تجهیزاتی که خرید و اضافه کردن آن به خط شستشوی اصلی کاملاً اختیاری می باشد، پیشنهاد می شود.
۱۲) خشک کن
خشک کردن پرک ها پس از مراحل آبکشی در دو مرحله انجام می شود. مرحله اول خشک کردن مکانیکی که توسط سانتریفیوژ انجام می شود و در مرحله دوم متعاقب آن خشک کردن حرارتی توسط هوای گرم و خشک.
۱۳) الک کردن پرک ها توسط هوا
به منظور بر طرف کردن ذرات غبار پرک ها و بقایای ذرات ریز لیبل های کاغذی و آلومینیمی و یا ذراتی از این قبیل، به الک ثانویه که با استفاده از دمش هوا کار می کند احتیاج است.
۱۴) سورت کردن اتوماتیک پرک ها
بسته به نوع مواد ورودی و با توجه به نیاز و کاربرد ثانویه پرک و همچنین با توجه به طراحی خط و بالا بردن کیفیت پرک ها، گاهاً احتیاج به نصب سیستم سورتینگ در محل خروجی خط شستشو می باشد. اخیراً سیستم های سورتینگ بسیار پر سرعتی توسط چندین شرکت اروپایی به عنوان ابزاری بسیار کار آمد و مکمل خطوط شستشو به دنیا عرضه شده که با استفاده از این سیستم ها می توان تا بالاترین درجه ممکن ذرات ریز آلودگی را برطرف نمود و پلیمر های غیر از PET را از PET به سرعت باز شناخت.
۱۵) سیستم تصفیه آب
مهمترین بخش تمام خطوط شستشو در دنیا نحوه طراحی گردش مسیر آب در طول خط و همچنین نحوه تصفیه آب مصرفی است.
از منظری دیگر باید گفت این بخش از خطوط شستشو نقشی سرنوشت ساز و تعیین کننده را ایفا می کند و فاکتور بسیار مهمی در اقتصادی بودن پروژه و همینطور در کیفیت پرک به شمار می آید. در اولین فاز طراحی پروژه سازنده می کوشد تا اطلاعات صحیح و موثق در مورد امکان پذیری استفاده طولانی مدت از آب مصرفی مورد نیاز، شرایط آب و مقدار و همچنین قیمت آب به دست آورد.
سیستم آب در گردش به ۶ بخش زیر تقسیم می شود.
۱) مشخصات آب ورودی
۲) واحد های تصفیه آب در طول خط
۳) مقدار و مشخصات آب به ازا هر مرحله از پروسه
۴) انرژی مصرفی مورد نیاز در تصفیه آب برای گرم کردن و سرد کردن
۵) مشخصات آبی که نهایتاً از خروجی به فاضلاب وارد می شود.
۶) آنالیز شیمیایی آب
برخی از نکات کلیدی برای طراحی تصفیه خانه به شرح زیر است:
▪ مقدار جریان آب ورودی به آب تصفیه شده و ورودی به مرحله آبکشی نهایی
▪ آب با سختی بسیار کم برای شستشوی پرک با کیفیت بالا مناسب است.
واکنش های پلی استر در برابر یون و برطرف کردن ترکیبات سختی آب مانند یون های Mg++، Ca++ و یا Fe++ که ممکن است خصوصاً برای تولید محصولات ثانویه چون: الیاف POY ریسندگی، فیلم بسته بندی و یا تولید بطری، بر کیفیت پرک تاثیر متقابل بگذارد.
▪ سیستم سیکل در گردش و یا به صورت بچ با نسبت عرق گیری ملایم
▪ استفاده مجدد و یا چند باره از گرما با نصب سیستم های مبدل حرارتی به دلیل صرف اقتصادی
▪ استفاده از تصفیه آب مناسب در بین هر مرحله به منظور پایین آوردن حجم کلی آب مصرفی
▪ آنالیز مناسب آب برای شناخت سختی ها، شفافیت، PH و قابلیت انتقال
معضلات و مشکلات فراوان زیست محیطی جهان، باعث شده امروز دولت ها از کارخانجات شستشو انتظار بهترین سیستم تصفیه آب را داشته باشند تا در غیر این صورت به مشکلات زیست محیطی جوامع بشری مشکل دیگری اضافه نشود. به عنوان مثال دولت چین در همین راستا اجازه ورود بطری های پرس شده را به خاک این کشور را نمی دهد بلکه فقط بطری هایی که یکبار شستشوی اولیه شده باشند و یا یک مرحله آسیاب شده باشند، اجازه ورود دارند.
ایران مسعود پزشکیان دولت چهاردهم پزشکیان مجلس شورای اسلامی محمدرضا عارف دولت مجلس کابینه دولت چهاردهم اسماعیل هنیه کابینه پزشکیان محمدجواد ظریف
پیاده روی اربعین تهران عراق پلیس تصادف هواشناسی شهرداری تهران سرقت بازنشستگان قتل آموزش و پرورش دستگیری
ایران خودرو خودرو وام قیمت طلا قیمت دلار قیمت خودرو بانک مرکزی برق بازار خودرو بورس بازار سرمایه قیمت سکه
میراث فرهنگی میدان آزادی سینما رهبر انقلاب بیتا فرهی وزارت فرهنگ و ارشاد اسلامی سینمای ایران تلویزیون کتاب تئاتر موسیقی
وزارت علوم تحقیقات و فناوری آزمون
رژیم صهیونیستی غزه روسیه حماس آمریکا فلسطین جنگ غزه اوکراین حزب الله لبنان دونالد ترامپ طوفان الاقصی ترکیه
پرسپولیس فوتبال ذوب آهن لیگ برتر استقلال لیگ برتر ایران المپیک المپیک 2024 پاریس رئال مادرید لیگ برتر فوتبال ایران مهدی تاج باشگاه پرسپولیس
هوش مصنوعی فناوری سامسونگ ایلان ماسک گوگل تلگرام گوشی ستار هاشمی مریخ روزنامه
فشار خون آلزایمر رژیم غذایی مغز دیابت چاقی افسردگی سلامت پوست