سه شنبه, ۷ اسفند, ۱۴۰۳ / 25 February, 2025
تكنولوژی تولید كامپوزیتها و كاربردهای روز افزون آنها در صنعت پیشرفته
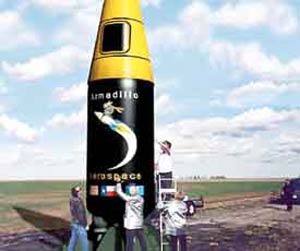
با نگاهی به طبیعت در مییابیم، موادی چون چوب، دندان، استخوان و چرم، همگی كامپوزیتهایی هستند با ساختار درونی پیچیده و خواص مكانیكی مطلوب كه بدست خالق متعال طراحی شدهاند. كامپوزیتها، یكی از مهمترین و گستردهترین مواد مهندسی هستند. تركیب مناسب، استحكام بالا و وزن كم، مواد كامپوزیت را بسوی عرصههای جدیدی سوق میدهد، اما خواص دیگر آنها نیز مورد توجه قرار گرفته است. ضریب انبساط حرارتی مواد كامپوزیت كوچك، قابلیت خفهكنندگی لرزش آنها مطلوب ومقاومت به خستگی آنها خوب است؛ انعطافپذیری در طراحی و ساخت این مواد بگونهای است كه تعداد قطعات مورد نیاز برای كاربردهای معین را كاهش داده و در نتیجه نیاز به مواد خام، اتصالات و بستها و همچنین زمان لازم برای مونتاژ را كم میكند.كامپوزیتها، به افزایش دما، خوردگی و سایش مقاوم هستند، خصوصاً در محیطهای صنعتی باعث كاهش هزینههای تعویض میشوند. تولید سالانه آنها در جهان بالغ بر ده میلیون تن بوده و در سالهای اخیر، میزان تقاضا برای این ماده، سالانه ۵ الی ۱۰ درصد افزایش یافته است. كامپوزیتها كاربردهای گستردهای دارند و ساختار آنها به گونهای است كه میتوانند برای شرایط كاربری مختلف، تنظیم شوند. انواع كامپوزیتها:گفتیم كه بسیاری از مواد خصوصاً مواد طبیعی، به نوعی كامپوزیت هستند. كامپوزیتها حداقل از دو جزء تشكیل شدهاند: یك بخش سخت با استحكام بالا و یك بخش نرمتر به نام زمینه. مثلاً چوب از فیبرهای سلولزی در زمینه لیگنین ساخته شده است یا دندان و استخوان هر دو، از كریستالهای سخت غیرآلی در یك زمینه كلاژنی (ماده آلی چقرمه) تشكیل شدهاند.در حقیقت، یكی از مهمترین مزایای تركیب زمینه و فیبر، ماهیت مكملی آن است. مثلاً رشتههای نازك شیشه، استحكام كششی نسبتاً بالایی دارند اما زود میشكنند؛ در مقابل، اكثر رزینهای پلیمری، استحكام كششی خوبی ندارند اما بسیار چقرمه، انعطافپذیر و چكشخوار هستند. با تركیب فیبر و زمینه، هر جزء ضعف دیگری را میپوشاند و ماده حاصل مفیدتر از هر جزء بتنهایی خواهد بود. استفاده از پلاستیكهایی كه با فیبر تقویت شدهاند، رو به افزایش است و طراحان و سازندگان متخصص به خواص منحصر بفرد كامپوزیتها پی بردهاند و میتوانند قطعاتی با كارایی بهینه طراحی كنند. ذكر این نكته لازم بنظر میرسد كه، خاصیت آنایزوتروپی (Anisotropy) در این مواد مشاهده میشود، یعنی در جهات مختلف، خواص متفاوتی دارند. این موضوع به دلیل آن است كه معمولاً جزء سختتر بصورت فیبری (رشتهای) وجود دارد. بعنوان مثال، چوب در جهت آوندها مستحكمتر است زیرا معمولاً آوندها موازی با محور شاخه یا تنه درخت قرار میگیرند، بنابراین، شاخه مثل یك میله معلق، وزنش را تحمل كرده و تنه درخت، باد و طوفان را به همین روش تحمل میكند. در ساخت مواد كامپوزیت غیر طبیعی، قابلیت كنترل آنایزوتروپی (غیر یكنواختی خواص در جهات متفاوت)، شرایط را برای طراحی اجزاء و فرایندهای تولید بصورت دلخواه، فراهم میآورد. یك مهندس باید اجزاء را بگونهای طراحی كند تا ماده ایزوتروپ (با خواص یكنواخت در جهات مختلف) شود. این موضوع بسیار مهمی است، زیرا احتمال دارد قطعه در سرویس دچار پارگی و شكستگی شود و باید در طراحی مورد توجه قرار گیرد. البته استثنائاتی هم وجود دارد: ورقهای فلزی بصورتی تولید میشوند كه خواص آنها در صفحه نسبت به خواص در جهت ضخامت متفاوت است كه البته بدلیل نوع بافت كریستالوگرافی است كه در حین نورد بوجود میآید.كامپوزیتها به سه دسته اصلی تقسیم میشوند: دسته اول، كامپوزیتهای زمینه پلیمری هستند كه بیشترین كاربرد را در صنعت دارند و معمولاً با فیبرهای سرامیكی مثل شیشه و كربن تقویت میشوند.دسته دوم، كامپوزیتهای زمینه فلزی هستند كه البته نسبت به كامپوزیتهای زمینه پلیمری، كاربرد تجاری كمتری دارند. دسته سوم، كامپوزیتهای زمینه سرامیكی هستند. هدف از مطالعه بر روی چنین موادی، بالا بردن چقرمگی ماده زمینه در اثر وارد كردن اجزاء دیگر است. بعلت مشكلات تولید، این مواد در مراحل اولیه توسعه قرار دارند. خواصی كه در طراحی و تولید كامپوزیتها باید مورد توجه قرار گیرند، عبارتند از: چقرمگی (تافنس)، استحكام، سفتی، چگالی و خواص حرارتی مثل هدایت و انبساط حرارتی. تفاوت بین ضریب انبساط حرارتی دو جزء، در هنگام حرارت منجر به باقی ماندن تنشهای درونی و در نتیجه تغییر خواص مكانیكی میشود. انتخاب تركیب و ساختار ماده كامپوزیت برای هر كاربرد خاص، كار سادهای نیست. وارد كردن ماده تقویت كننده به زمینه، كل خواص ماده را تغییر میدهد. توجه به تغییرات احتمالی ریزساختار زمینه ناشی از حضور ماده تقویت كننده، و همچنین تنشهای باقیمانده ناشی از ضریبهای حرارتی متفاوت، ضروری است. آنالیز توزیع بار نیز در تعیین رفتار مكانیكی ماده كامپوزیت لازم بنظر میرسد.
مواد تقویت كننده: مواد تقویتكننده بسیاری وجود دارد و همگی دارای سختی زیاد و چگالی نسبتاً كم هستند. فیبرهای كربن و شیشه امروزه كاربرد گستردهای در كامپوزیتهای زمینه پلیمری دارند. فیبرها، ذرات و ویسكرزهای سرامیكی میتوانند در تقویت استحكام زمینههای فلزی و سرامیكی مورد استفاده قرار گیرند.فیبرهای كربنی: فیبرهای كربنی با قطر ۸ میكرومتر، شامل كریستالهای كوچك از رافیتهای " توربوستراتیك" (یكی از آلوتروپهای كربن) هستند. این گرافیت شبیه تك كریستال گرافیتی بوده و دارای صفحات اصلی موازی است. بهترین استحكام محوری موقعی وجود خواهد داشت كه ترتیب قرارگیری صفحات اصلی فیبر كربنی، موازی محور فیبر باشد. قرارگیری صفحات اصلی در مقطع عرضی فیبر نیز مهم است. سه روش اصلی برای تولید فیبرهای كربنی وجود دارد:
الف) كشش و حرارت فیبرهای پلیاكریلونیتریل: این روش در انگلیس توسعه یافته است و امروزه یكی از روشهای مطلوب برای تولید فیبرهای كربنی با استحكام بالا محسوب میشود. ماده اولیه این فرایند، پلیمر پلیاكریلونیتریل (PAN) میباشد. این پلیمر آن قدر كشیده میشود تا ردیف زنجیرهای مولكولی تشكیل شوند. سپس ماده را حرارت میدهیم تا گروههای فعال نیتریل واكنش داده و مولكولهای پلیمر بصورت پلهای درآیند كه شامل ردیفی از حلقههای شش ضلعی خواهند بود. در حالی كه فیبر تحت تنش قرار دارد، در محیط اكسیژندار حرارت میبیند و پیوندهای شیمیایی عرضی بین مولكولهای هر پله ایجاد میشود. سپس، فیبر با حرارت دهی در دمای بالاتر، ساختار حلقهای مییابدكه بعد به گرافیت توربوستراتیك تبدیل میشود.ب) حرارت و اكستروژن قیر میانفاز: این فرایند اولین بار توسط فردی به نام "اُتانی" پیشنهاد شد.قیر، تركیبی پیچیده از هزاران مولكول مختلف هیدروكربن است. در این روش، قیر در دمایی بالاتر از ۳۵۰ درجه سانتیگراد حرارت دیده و مولكولهایی بزرگتر تشكیل میدهد كه تمایل دارند بصورت موازی هم، قرار گیرند كه در این حالت به آن قیر "میانفاز" گویند و بصورت كریستال مایع میباشد. این مایع سریعاً اكسترود شده و نخ خام تولید میشود. سپس نخها در دمای ۲۰۰۰ درجه سانتیگراد حرارت میبینند تا ساختار نهایی بسیار گرافیتیتر از فیبرهای بدست آمده از روش قبل باشد. این نخها، خواص ترموپلاستیك خاصی دارند، بعنوان مثال هدایت حرارتی فوقالعاده زیادی داشته و میتوانند در ترمزهای هواپیما از جنس كامپوزیتهای كربن/كربن بكار روند.
ج) رسوب تفكافتی (Pyrolytic): كه به دلیل تجاری نبودن، از توضیح در مورد این فرایند صرف نظر میكنیم.فیبرهای شیشهای: این فیبرها بر پایه سیلیكا (اكسید سیلیسیم) ساخته شده و كمی هم اكسیدهای كلسیم، بور، سدیم، آلومینیم و آهن دارند. این شیشهها غیر بلوری هستند. سه نوع فیبر مختلف از لحاظ تركیب و خواص وجود دارد: متداولترین آن، E_glass (E به الكتریسیته [Electricity] اشاره دارد) نام دارد كه خواص الكتریكی و استحكام مطلوبی داشته و خوب كشیده میشود. نوع دیگر، C_glass بوده و مقاومت به خوردگی خوبی دارد. حرف C از خوردگی [Corrosion] میآید. نوع سوم، S_glass میباشد كه حرف s در آن نشاندهنده استحكام [Strength] بوده و مقاومت به دما و استحكام و البته قیمت بالایی دارد. بر خلاف فیبرهای كربنی، فیبرهای شیشهای خواص ایزوتروپیك (در جهات مختلف یكنواخت) دارند.فیبرهای شیشهای با ذوب مواد خام در یك محفظه و سپس ریختن آن بدرون یك سری پوسته پلاتینی كه هر كدام سوراخهای متعدد دارد و اكسترود مذاب شیشه و بعد پیچیده شدن فیبرها دور یك غلتك با سرعت چند هزار متر در دقیقه، تهیه میشوند. فیبرهای دیگری نیز چون فیبر آلی، كاربید سیلیكون و اكسید آلومینیم وجود دارند كه بنا بر كاربردهای خاص در موارد گوناگون بكار میروند.جهتگیری فیبرها قابل كنترل است و این فاكتوری است كه فواید فراوان در كاربردهای مختلف دارد. مثلاً در دسته چوب گلف، فیبرهای كربن و بور در جهات مختلف با زاویههای مختلف قرار گرفتهاند و استحكام و سفتی آنها باعث میشود تا دسته چوب بتواند انواع نیروهای كششی، فشاری، پیچشی و خمشی را تحمل كند. زمینه: بر اساس روش تولید، كاربرد و خواص مورد نیاز، زمینه انتخاب میشود، این انتخاب از اهمیت زیادی برخوردار است. خواص زمینه به ریزساختار بستگی دارد و آن نیز به روش تولید، عملیات حرارتی و مكانیكی بعدی وابسته است. زمینه در كامپوزیت پلیمری، فلزی یا سرامیكی است. زمینههای پلیمری دو دسته هستند:گرماسخت و گرمانرم. به پلیمرهای گرماسخت پس از تولید حرارت داده شده و شكل مناسبی به آنها داده میشود. پس از سرد شدن، تعدادی پیوند عرضی بین زنجیرههای پلیمر تشكیل میشود كه باعث افزایش استحكام میشود. برای افزایش استحكام بیشتر این اتصالات، مواد در دمای پایین عملیات حرارتی میشوند. نمونههایی از پلیمرهای گرماسخت عبارتند از: اپكسی، استروفیل و پلیمرهای غیراشباع. در پلیمرهای گرمانرم، پیوندهای عرضی تشكیل نمیشود؛ در این پلیمرها، شبكه پیچیدهای از پلیمرها در جهات مختلف تشكیل میشود كه هنگام حرارت، باز و هنگام سرد شدن، دوباره بسته میشود. گرمانرمها، سبكتر، مقاومتر به خوردگی شیمیایی، با استحكام كششی بیشتر و انعطافپذیری قبل از شكست خیلی بیشتر هستند. نایلون و پلیپروپین، نمونههایی از پلیمرهای گرمانرم میباشند. سالها فلزات، فیبرها و پر كنندههای معدنی به زمینههای گرماسخت و گرمانرم اضافه شده و كامپوزیتها را ساختهاند، اما همواره مواد گرمانرم حجم بیشتری را بخود اختصاص دادهاند. متداولترین زمینههای فلزی نیز، آلومینیم، منیزیم و تیتانیم هستند. مشكل عمده این زمینهها آن است كه فعالیت شیمیایی زیادی دارند و ممكن است با فیبرهایی كه در آنها قرار میگیرند، واكنش دهند، محصولات واكنش معمولاً ترد هستند. زمینههای سرامیكی را نیز میتوان به چهار دسته اصلی تقسیمبندی كرد: دسته اول، سرامیكهای شیشهای كه غیربلوری بوده، به راحتی تولید میشوند و دمای نرمی آنها كمتر از سرامیكهای بلوری است. دسته دوم، سرامیكهای معمولی و متداول از قبیل كاربید سیلیسیم و اكسید آلومینیم كه بلوری بوده و دانههای بلوری در جهات مختلف بطور تصادفی قرار گرفتهاند. دسته سوم، ورقهای لایهای سرامیك كه با لایه نازكی از گرافیت نرم از هم جدا میشوند؛ و دسته چهارم، كامپوزیتهای كربن/ كربن كه با عبور فیبرهای كربنی از بخار مواد خاص ساخته میشوند و كاربرد گستردهای در صنعت دارند. سرامیكها معمولاً بسیار ترد هستند؛ اضافه كردن فیبر، انعطافپذیری زمینههای سرامیكی را افزایش داده، از گسترش ترك در مرز بین زمینه و فیبر جلوگیری كرده و شكست نهایی را به تاخیر میاندازد. روشهای تولید: یكی از جنبههای مهم مواد كامپوزیت، تكنولوژی تولید آنها است. بسته به ماهیت زمینه و فیبر و همچنین چگونگی توزیع فیبر، تولید با قیمت مناسب و كیفیت مطلوب به روشهای مختلفی انجام میشود. اغلب فرایندهای گفته شده برای كامپوزیتهای زمینه پلیمری، جنبه تجاری داشته و بطور گسترده استفاده میشوند؛ اما در مورد كامپوزیتهای فلزی و سرامیكی، روشها اغلب در مرحله تحقیق و توسعه قرار دارند. سه روش عمده برای تولید كامپوزیتهای پلیمری گرماسخت و دو روش اصلی برای كامپوزیتهای پلیمری گرمانرم وجود دارد. ابتدا در مورد كامپوزیتهای گرماسخت، توضیح میدهیم: ۱. دور قرقرههایی، فیبرها را پیچانده و از هر قرقره، فیبرها را وارد حمام حاوی رزین گرماسخت میكنیم. یك لایه رزین روی فیبر تشكیل میشود. فیبرها حول یك استوانه میپیچند؛ زاویه پیچش در این مرحله بسیار مهم است، باید آن را بگونهای تغییر داد كه استحكام همه جا یكسان شود. این روش برای ساخت مقاطع منظم بكار میرود. در روشهای مشابه، پس از عبور از حمام، فیبرها اكسترود میشوند تا به شكل معینی درآیند. در انتها، بمنظور افزایش استحكام، عملیات حرارتی و پخت روی كامپوزیت انجام میشود. ۲. در این روش، فیبرها در محفظه قالب بصورت تكه لایههای پارچهای متقاطع قرار میگیرند و سپس مذاب با فشار وارد محفظه میشود، چون مذاب گرماسخت است بسرعت همه گوشهها را پر میكند. در آخر، عملیات حرارتی اعمال میشود. ۳. در این روش ذرات و فیبرهای كوتاه با رزین مخلوط شده و سپس در قالب تزریق میشوند. به دلیل آنكه زمینههای گرمانرم مشكل گرانروی دارند، باید فرایندهایی استفاده شوند كه از پر شدن قالب در آنهااطمینان داریم.
ایران مسعود پزشکیان دولت چهاردهم پزشکیان مجلس شورای اسلامی محمدرضا عارف دولت مجلس کابینه دولت چهاردهم اسماعیل هنیه کابینه پزشکیان محمدجواد ظریف
پیاده روی اربعین تهران عراق پلیس تصادف هواشناسی شهرداری تهران سرقت بازنشستگان قتل آموزش و پرورش دستگیری
ایران خودرو خودرو وام قیمت طلا قیمت دلار قیمت خودرو بانک مرکزی برق بازار خودرو بورس بازار سرمایه قیمت سکه
میراث فرهنگی میدان آزادی سینما رهبر انقلاب بیتا فرهی وزارت فرهنگ و ارشاد اسلامی سینمای ایران تلویزیون کتاب تئاتر موسیقی
وزارت علوم تحقیقات و فناوری آزمون
رژیم صهیونیستی غزه روسیه حماس آمریکا فلسطین جنگ غزه اوکراین حزب الله لبنان دونالد ترامپ طوفان الاقصی ترکیه
پرسپولیس فوتبال ذوب آهن لیگ برتر استقلال لیگ برتر ایران المپیک المپیک 2024 پاریس رئال مادرید لیگ برتر فوتبال ایران مهدی تاج باشگاه پرسپولیس
هوش مصنوعی فناوری سامسونگ ایلان ماسک گوگل تلگرام گوشی ستار هاشمی مریخ روزنامه
فشار خون آلزایمر رژیم غذایی مغز دیابت چاقی افسردگی سلامت پوست