سه شنبه, ۱۴ اسفند, ۱۴۰۳ / 4 March, 2025
فولادهای ضدزنگ در صنعت خودروسازی
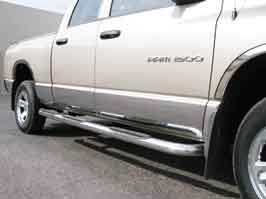
شواهد نشان میدهد كه فولاد ضدزنگ (Stainless Steel) به دلیل خواص مطلوبی چون نسبت استحكام به وزن بالا، مقاومت به خوردگی، قابلیت شكلپذیری و عملكرد مناسب در هنگام ضربه، بیش از پیش در قطعات مربوط به خودرو به كار خواهد رفت.
فولاد ضدزنگ، نام گروهی از آلیاژهای آهنی حاوی مقادیر كروم بالا بیش از ۵/۱۰ درصد و كربن به میزان حداكثر ۲/۱ درصد به علاوه عناصر دیگری مثل نیكل و مولیبدن، آلومینیوم، تیتانیم، سیلسیم، نایوبیم، نیتروژن، سولفور و سلنیوم است. این فولادها به اشكال مختلف از جمله ورق، فویل، میلگرد، سیم، لوله، و محصولات نیمهتمام و غیره تولید میشود. آلیاژ ۳۰۴ از آلیاژهای معروف این گروه با ۱۸ درصد كروم و ۸ درصد نیكل است.
▪ورق نازك (SHEET) : ورق نازك به محصولات نورد تخت گفته میشود كه عرضی معادل حداقل ۶۱۰ میلیمتر و ضخامت كمتر از ۷۶/۴ میلیمتر دارند. تقریبا همه فولادهای ضدزنگ بجز برخی انواع مارتنزیتی میتوانند بصورت ورق نازك تولید شوند. ابتدا شمش آنها از ریختهگری بدست آمده و بعد نورد میشود.
▪تسمه (STRIP) : تسمه محصول دیگر نورد تخت است كه پهنایی كمتر از ۶۱۰ میلیمتر و ضخامت بین ۱۳/۰ تا ۷۶/۴ میلیمتر دارد. تسمهها پس از نورد داغ، عملیات آنیل و سپس اسیدشویی ، نورد سرد میشوند و به این ترتیب تسمه فولاد ضدزنگ نورد سرد شده بدست میآید. بسته به میزان ضخامت درخواستی نورد سرد در چند مرحله انجام میشود.
▪صفحه (PLATE) : صفحه یك محصول نورد تخت یا آهنگری است كه بیش از ۲۵۰ میلیمتر عرض و حداقل ۷۶/۴ میلیمتر ضخامت دارد. فولادهای ضدزنگ فریتی پرآلیاژ، برخی فولادهای ضدزنگ مارتنزیتی و تعداد اندكی از انواع بینیاز از ماشینكاری از موارد استثنا در تولید این محصول هستند.
فویل یا كاغذ فلزی (FOIL) : فویل نیز محصول فرایند نورد تخت است؛ تا ۱۳/۰ میلیمتر ضخامت دارد و عرض آن كمتر از ۶۱۰ میلیمتر میباشد. فویلها از انواع ۲۰۱، ۲۰۲، ۳۰۱، ۳۰۲، ۳۰۴، ۳۰۵، ۳۱۶، ۳۲۱، ۳۴۷، ۴۳۰ و ۴۴۲ و همینطور از یك سری آلیاژهای خاص ساخته میشوند. خواص مكانیكی فویلها به ضخامت آنها بستگی دارد. با كاهش ضخامت، استحكام كششی آنها افزایش اما انعطافپذیری كاهش مییابد.
▪میلهگرد (BAR) : میلهگردها در انواع ضخامتها و اشكال وجود دارند. میلهگردهای با تمامكاری داغ، عموماً توسط نورد داغ، آهنگری یا پرش شمش شكل میگیرند كه البته بعد از آن، برای رسیدن به ابعاد نهایی دوباره نورد داغ، آهنگری یا اكسترود میشوند.
معمولا لایهای غیر فعال بر روی سطح آلیاژ تولید میشود؛ به دلیل تشكیل این لایه به ضخامت حدود ۱ تا ۲ نانومتر، این آلیاژ مقاومت بسیار خوبی به خوردگی دارد. این لایه غیر فعال خودترمیم بوده و بنابراین خسارات شیمیایی و مكانیكی در محیطهای اكسیدكننده دوباره التیام یافته و عامل افزایش خوردگی نخواهند شد.
فولادهای ضدزنگ معمولا میتوانند توسط بسیاری از فرایندهای شكلدهی سرد تغییر شكل یابند. این فرایندها عبارتند از: پولكزنی، خمكاری، سوراخكاری، نورد، ضربزنی، برجستهكاری، پرسكاری، شكلدهی چرخشی، و كشش عمیق. به طور كلی تمام تجهیزاتی كه برای شكلدهی فولاد كربنی ساده به كار میرود، برای فولاد ضدزنگ نیز مورد استفاده قرار میگیرد. چون نیروی بیشتری برای شكلدهی فولاد ضدزنگ لازم است، ظرفیت دستگاه كاهش خواهد یافت. علاوه بر آن نیاز به ابزارهای شكلدهی بهتر هم وجود دارد. فولادهای ضدزنگ نه تنها استحكام بالاتری نسبت به فولادهای كربنی ساده دارند، بلكه كارسختی بیشتری نیز داشته و درنتیجه موجب سایش بیشتر و حساسیت به جوش فشاری میشوند. بنابراین ابزار بكار گرفته شده در مورد این فولادها باید سختتر، صافتر و با طراحی بهتر باشد. فولاد ابزار با درجات بالاتر بكار میروند و اغلب كاربید تنگستن و برنز آلومینیوم هستند. در مواردی كه از همان ابزار مورد استفاده در فولادهای كربنی برای شكلدهی استفاده میشود، باید روانكارهایی با كیفیت بالاتر اعمال شود و كاهش عمر ابزار نیز در نظر گرفته شود. تقاضا برای فولادهای ضدزنگ روز به روز در حال افزایش است.
هم اكنون فولاد ضدزنگ در سیستم اگزوز خودروها بكار میرود. در اوایل دهه ۹۰ سیستمهای اگزوز خودروهای جدید از فولادهای كربنی ساده یا فولادهای كربنی پوششدار ساخته میشد. اما امروزه اكثر خودروهای جدید برای افزایش مقاومت و ماندگاری، سیستمهای اگزوزی از جنس فولادهای ضدزنگ دارند. تقریبا ۴۵ تا ۵۰ پوند از فولادهای ضدزنگ مصرفی در صنعت خودروسازی، در سیستم اگزوز استفاده میشود.
به علاوه اخیرا این فولاد در ساخت سیستمهای نگهداری، قطعات مربوط به ترمز و سوخت و در قابهای اتوبوس و كامیون به كار گرفته شدهاند.
قطعات دیگر ساخته شده از این فولادها كه در مرحله توسعه قرار دارند و سازندگان خودرو روی آنها كار میكنند عبارتند از: چهارچوب موتور، میلههای داخلی، مخازن سوخت در عقب خودرو، سپرها و میله سپرها، صفحات ترمز، اجزاء حساس به برخورد، واشر دهانه سیلندر، قطعات سیستم تعلیق و جاذب انرژی، چرخها و رویه چرخ.
در طول دهه گذشته، سازندگان و محققان برای تعیین فواید احتمالی شكلدهی این نوع فولاد بجای فولادهای كربنی یا آلومینیوم، بر روی كاربردهای مختلف فولادهای ضدزنگ در صنعت خودرو مطالعه كردهاند.
به طور كلی هزینه تولید فولادهای ضدزنگ بیشتر از فولاد كربنی و آلیاژهای آلومینیوم است و به همین دلیل در ظاهر مقرون به صرفه به نظر نمیرسد؛ اما وقتی نسبت استحكام به وزن بالای فولاد ضدزنگ را در نظر میگیریم، میتوان از فولاد ضدزنگ سبكتر و نازكتر استفاده كرد و آن را جانشین فولاد كربنی ضخیمتر یا آلیاژهای آلومینیوم با استحكام بالا (سری ۶۰۰۰) در قطعات خودرو قرار داد. علاوه بر آن، پتانسیل فولادهای ضدزنگ در ماندگاری و دوام طولانی می تواند منجر به صرفهجویی اقتصادی در چرخه عمر محصول شود.
در صورت در نظر گرفتن خواص این فولادها در طراحیهای اولیه، بهترین صرفهجویی اقتصادی و بیشترین كاهش حجم در ماده مصرفی به دست خواهد آمد. برای بهرهبرداری از مزیت كاهش وزن در فولادهای ضدزنگ، باید اشكال برخی قطعات خودرو و چگونگی روش ساخت آنها اصلاح شده و تغییر یابد. مثلا برای استفاده از مزیت شكلپذیری این فولادها، بهتر است برخی قطعات از لولههای هیدروفرم شده (Hydroformed) ساخته شوند.
محرك اولیه عمومیت یافتن هیدروفرم كردن (یا شكل دادن هیدرولیكی) بخصوص در صنعت خودروسازی صرفهجوییهای عمده در وزن، تعداد قطعات و ... در مقایسه با روشهای متداول مثل Stamping (به معنی پرسكاری و قالبزنی) میباشد.
فرایند شكلدهی هیدرولیكی ورقها معمولا به دو گروه شكلدهی هیدروستاتیكی و شكلدهی هیدرومكانیكی تقسیم میشوند. به علاوه برخی از انواع روشهای مورد استفاده به عنوان اختراع به ثبت رسیده و Patent هستند مثل روش SMG یا شكلدهی پیچی.
روشهای هیدروفرمینگ مدتها مطرح بود اما شاید هیچگاه به اندازه ظرفیت آن از این روش در صنعت استفاده نشد. به نظر میرسد كه كم كم زمان فراگیر شدن این روش رسیده باشد. خواص كششی خوب فولادهای ضدزنگ آستنیتی در هنگام شكلدهی هیدرولیكی بعنوان فرایندی كه كنترل مناسبی بر میزان كاهش ضخامت ورق دارد،مزیت بزرگی محسوب میشود. مزیت اصلی شكلدهی مكانیكی در مقایسه با كشش عمیق آن است كه در هیدروفرمینگ قطعات عمیقتر میتوانند كشیده شوند (به عنوان مثال نسبت كشش در فولاد ضدزنگ میتواند از ۲ به بیش از ۵/۲ افزایش یابد). مشكل اصلی شكلدهی هیدرولیكی نیز آن است كه سوددهی ساخت را به میزان زیادی كم میكند.
عوامل مختلفی بر موفقیت فرایند شكلدهی هیدرولیكی موثرند؛ از جمله: اصطكاك و روانكاری، تجهیزات، سرعت تولید و زمان چرخه تولید و خواص شكلپذیری ماده.
روانكار خوب باید بتواند ۱. فشار زیاد را تحمل كند، ۲. از روانكاری مطلوبی برخوردار بوده به نحوی كه از اطلاعات لغزشی بین قالب و قطعه كار جلوگیری كند، ۳. ناخالصی نداشته باشد، ۴. هزینه فرایند را بالا نبرده و قیمت معقولی داشته باشد، ۵. كار كردن با آن راحت باشد و به راحتی از قالب و قطعه كار جدا شود، ۶. سایش قالب را كاهش دهد. هیچ روانكاری تمام موارد فوق را بطور كامل در بر ندارد بنابراین باید در انتخاب روانكار شرایط عملیات شكلدهی در نظر گرفته شود.
تحقیقات گسترده انجام گرفته در پنج سال گذشته منجر به تحول عظیم در روش هیدروفرمینگ در صنعت شده است و دیگر اجازه تولید انبوه اشكال مختلف را به سازندگان میدهد. اما در هر حال این فرایند، جدید بوده و نیاز به تحقیق و توسعه بیشتردارد. به دلیل فشار بالایی كه در این فرایند به كار میرود، ابزارهای مورد استفاده نمیتوانند نرم باشند، قالبها باید از فولادهایی با سختی مشخص و پوششهای خاص ساخته شوند كه تمام آنها هزینهبر است.
بنابراین برای افزایش بهرهوری این فرایند باید مطالعات گستردهای در زمینه كاهش هزینههای تحمیلی در حین تولید در دستور كار محققین و صنعتگران قرار گیرد.
یكی از زمینههای تحقیق بررسی میزان كاهش وزن در صورت استفاده از فولاد ضدزنگ به ویژه در صورت بهكارگیری فرایند شكلدهی هیدرولیكی است. برای محاسبه پتانسیل كاهش وزن فولاد ضدزنگ در ساختارهای بدنه خودرو كه مسئول جذب انرژی هستند از قبیل اجزاء كناری، آزمایش مقایسهای انجام شد. ابتدا ساختار جانبی خودرو كه معمولا از جنس فولاد كربنی ساخته میشود، بدون اصلاح شكل در آن، از فولاد ضدزنگ سبكتر و نازكتر ساخته شد. در مرحله بعد، ساختار جانبی فوق از فولاد ضدزنگ ساخته شد اما با طراحی دوباره و استفاده از هیدروفرمینگ برای استفاده بهینه از خواص شكلپذیری مطلوب این فولاد. این ساختار جانبی كه از فولاد كربنی ساده تولید میشود، یك ساختار چند جزئی بوده و از سه جزئی كه از روش كشش عمیق تولید شدهاند و یك قسمت تقویتكننده تشكیل شده است كه به وسیله جوش نقطهای به هم متصل میشوند. وزن كلی این ساختار بدون در نظر گرفتن قطعه اتصال، ۱۶/۲۸ كیلوگرم بود.
با تغییر ماده اولیه، با جذب انرژی یكسان جایگزینی فولاد ضدزنگ ۲B ، نوع C۶۰۰ و C۱۰۰۰ به ترتیب ۳/۹، ۱۴ و ۲/۲۸ درصد كاهش وزن را به همراه داشت.
وقتی این سه نوع فولاد در طراحی دوباره، تحت فرایند هیدروفرمینگ قرار گرفتند، نتایج ۴/۱۹، ۲/۳۰و ۸/۳۳ درصد كاهش وزن را نشان میداد. اما مطالعات فرمپذیری نشان داد كه اصلاح طراحی برای تولید اجزاء كناری از فولادهای ضدزنگ در فولاد C۱۰۰۰ تحت شرایط كار سرد، حتی لازم و ضروری بوده است.
بیشترین كاهش وزن در فولادهای ضدزنگ تنها هنگامی بدست میآید كه با طراحی جدید از مزیت شكلپذیری این فولادها استفاده كرده و فرایند هیدروفرمینگ را روی آنها انجام دهیم. یكی دیگر از فواید هیدروفرمینگ آن است كه تعداد قطعات مورد نیاز برای تولید قطعه جانبی با حذف جوش، از چهار به یك كاهش خواهد یافت. به دلیل آنكه دیگر به لبه احتیاجی نیست، سطح مقطع میله میتواند بزرگتر شده و پروفیل راستتر و مستقیمتر طراحی شود.
مطالعهای كه بر روی شكلپذیری آنها انجام گرفته، نشان میدهد كه طراحی جدید جزء جانبی با فولاد كربنی ساده نمیتواند هیدروفرم شود. برای شناسایی فولادهای كربنی دیگر با استحكام بالا كه بتوانند در طراحی جدید این جزء جانبی، هیدروفرم شوند، شبیهسازیهای مختلفی انجام شده است و نتایج نشان میدهد كه طراحی هیدروفرم نمیتواند با فولادهای كربنی استفاده بالا به كار رود و بنابراین برای رسیدن به كاهش وزن موثر حتما فولاد ضدزنگ مورد نیاز است.
به علاوه، هیدروفرمینگ اجزاء جانبی عملكرد آنها در حین برخورد را نیز بهبود میبخشد. شكل خمیده جزء جانبی از جنس فولاد كربنی باعث میشود تا به جای له شدن و خرد شدن (Crushing) در حین تصادف از جلو، قطعه چین بخورد یا به عبارتی بصورت آكاردئونی دربیاید (Buckling) و این ویژگی در تستهای تصادف به اثبات رسیده است. در تستهای ایمنی عموما له شدن نتایج بهتری را نسبت به چین خوردن نشان میدهد.
آیا روزی فراخواهد رسید كه تمام قطعات استوانهای خودرو كه اكنون از فولادهای كربنی ساده یا فولادهای آلیاژی ساخته میشوند مثل لوله پمپ آب، لوله روغن، قطعات تهویه هوا، لوله خروج آب سیستم خنككننده موتور و لوله فرعی خنككننده، از جنس فولاد ضدزنگ باشند؟ این سوالی است كه هنوز توسط مهندسان بطور قطعی پاسخ داده نشده است.
شیوا اسلامی
منابع:
www.thefabricator.com
www.key-to-steel.com
www.outokumpu.com
ایران مسعود پزشکیان دولت چهاردهم پزشکیان مجلس شورای اسلامی محمدرضا عارف دولت مجلس کابینه دولت چهاردهم اسماعیل هنیه کابینه پزشکیان محمدجواد ظریف
پیاده روی اربعین تهران عراق پلیس تصادف هواشناسی شهرداری تهران سرقت بازنشستگان قتل آموزش و پرورش دستگیری
ایران خودرو خودرو وام قیمت طلا قیمت دلار قیمت خودرو بانک مرکزی برق بازار خودرو بورس بازار سرمایه قیمت سکه
میراث فرهنگی میدان آزادی سینما رهبر انقلاب بیتا فرهی وزارت فرهنگ و ارشاد اسلامی سینمای ایران تلویزیون کتاب تئاتر موسیقی
وزارت علوم تحقیقات و فناوری آزمون
رژیم صهیونیستی غزه روسیه حماس آمریکا فلسطین جنگ غزه اوکراین حزب الله لبنان دونالد ترامپ طوفان الاقصی ترکیه
پرسپولیس فوتبال ذوب آهن لیگ برتر استقلال لیگ برتر ایران المپیک المپیک 2024 پاریس رئال مادرید لیگ برتر فوتبال ایران مهدی تاج باشگاه پرسپولیس
هوش مصنوعی فناوری سامسونگ ایلان ماسک گوگل تلگرام گوشی ستار هاشمی مریخ روزنامه
فشار خون آلزایمر رژیم غذایی مغز دیابت چاقی افسردگی سلامت پوست