چهارشنبه, ۲۶ دی, ۱۴۰۳ / 15 January, 2025
مواد دیرگداز تاثیر مستقیمی بر صنایع مادر دارند ایران پیشتاز در صنعت مواد نسوز
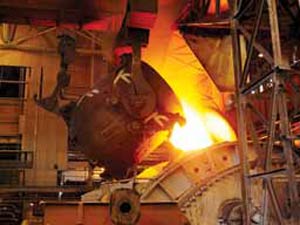
مواد دیرگداز یا نسوز موادی هستند که به عنوان لایه و آستر دیواره کورههای صنعتی به کار میروند. نقطه ذوب این مواد بالای ۱۵۰۰ درجه سانتیگراد است و در بعضی شرایط، موادی که بتوانند در محیطهای خورنده و شرایط حساس محیط از لحاظ دما و ترکیب شیمیایی تا ۱۰۰۰ درجه سانتیگراد تحمل داشته باشند، جزء مواد دیرگداز طبقهبندی میشوند. دیرگدازها عمدتا از مواد معدنی تهیه میشوند که نه تنها دارای درجه حرارت ذوب بالایی هستند، بلکه باید بتوانند در مقابل عوامل مخرب دیگری چون سایش، فشردگی، شوکهای حرارتی و تاثیر مواد سرباره کورهها در صنایعی چون ذوب آهن، فولاد، سرامیک، سیمان، شیشه و پتروشیمی مقاومت داشته باشند. مگنزیت و کرومیت مهمترین تامین کننده مواد معدنی موردنیاز صنایع دیرگداز محسوب میشوند که از اهمیت اقتصادی بسیار بالایی برخوردارند. علاوه بر ذخایر معدنی مگنزیت و کرومیت، ذخایر آلومینوسیلیکاتی (شاموتی)، بوکسیتی و آندالوزیتی نیز در صنعت مواد دیرگداز قابل ذکر هستند.
●تقسیمبندی از نظر میزان دانش لازم برای تولید
دیرگدازها از نظر میزان دانش لازم برای تولید به دو گروه دیرگدازهای سنتی و دیرگدازهای پیشرفته تقسیم میشوند. دیرگدازهای سنتی از نظر زمانی بر دیرگدازهای پیشرفته تقدم دارند ولی دیرگدازهای پیشرفته نسبت به دیرگدازهای سنتی به دلیل دانش محوری بودن از ارزش افزوده بالاتر و بازده عملکردی بیشتری برخوردار هستند. آجرهای آلومینوسیلیکاتی نمونهای از نسوزهای سنتی هستند و موادی چون دیرگدازهای حاوی کربن و جرمهای ریختنی حاوی مقادیر بسیار کم سیمان در گروه دیرگدازهای پیشرفته قرار میگیرند.
●تقسیمبندی از نظر ترکیب شیمیایی
از دیدگاه شیمیایی، مواد نسوز به سه گروه اسیدی، قلیایی و خنثی تقسیم میشوند و با توجه به اینکه حدود ۶۵ درصد کل محصولات در صنعت فولاد مورد استفاده قرار میگیرند و به دلیل این که ماهیت سرباره فولاد قلیایی است، میتوان گفت نسوزهای قلیایی از اهمیت بیشتری نسبت به سایر محصولات برخوردار هستند. تولید منیزیم که یکی از نیازهای اصلی کارخانههای فولاد، سیمان و صنایع معدنی کشور است، در سالهای گذشته رشد قابل توجهی داشته است. در سال ۵۷ فقط ۶۷ هزار تن مواد نسوز در داخل کشور تولید میشد اما در حال حاضر این میزان به حدود ۳۵۰ هزار تن رسیده و نیاز کشور به مواد نسوز وارداتی در ۱۰ سال گذشته، از ۱۲ درصد به ۸ درصد کاهش یافته است. نسوزهای قلیایی با نسبتهای مختلف از اکسید منیزیم و اکسید کلسیم عمدتا برپایه منیزیم و دولومیت ساخته میشوند و فرآوری آنها به صورتی انجام میشود که اجزاء نامناسب آن کاهش یابد. منظور از اجزاء نامناسب آن بخش از مواد اولیه هستند که بر اثر افزایش دما به فازها یا ماتریسهایی که از نسوزندگی پائینی برخوردار هستند تبدیل میشوند.
●تقسیمبندی دیرگدازها از نظر شکل ظاهری
دیرگدازها از نظر شکل ظاهری به سه گروه شکلدار، بی شکل و فیبری تقسیمبندی میشوند. شکلدارها همان آجرهای نسوز هستند که در ابعاد و اشکال متنوعی ساخته میشوند و در محل آجرچینی میشوند. در حالی که دیرگدازهای بی شکل به صورت پودر یا گرانول عرضه شده و قابلیت پذیرش هر شکلی را به طور یکپارچه دارا هستند. دیرگدازهای بی شکل را بر اساس نوع کاربرد یا نحوه تبدیلشان به ملات، جرمهای ریختی، پلاستیک، کوبیدنی و پاشیدنی تقسیمبندی میکنند. دیرگدازهای فیبری هم به صورتهای مختلف به شکل پتو، تخته، نمد، کاغذ، پارچه و حتی ریسمان وجود دارند و عمدتا جهت عایقکاری و آببندی در دمای بالا به کار میروند.
●فرایند عمومی تولید
در فرایند تولید مواد نسوز یا دیرگداز مواد اولیه را در کورههای دوار قائم یا تونلی حرارت داده که اصطلاحا به این فرایند سینترینگ یا تفوجشی گفته میشود و هدف از آن رسیدن به دانههای محکم و پایدار است که برای ساخت محصولات دیرگداز مورد استفاده قرار میگیرند. برای تولید مواد سنتزی ابتدا مواد اولیه تکلیس، سپس پودر شده و به صورت خشته پاپلت درآمده و در دمای بالا سنتز میشوند. کلینکر منیزیا دولوما که حاصل رسوبات آواری ساحلی که بناتها در دوره پالئوزوئیک میباشند به علت قلیائیت بالا یک نسوز بسیار مطلوب خصوصا برای جرمهای تعمیر گرم و کوبیدنی در کف کورههای قوس الکتریکی تلقی میشود. به دلیل وجود ذخایر فراوان، مرغوب و ارزان دولومیت در کشور، ایده تولید این محصول از طریق ایجاد مخلوط همگون منیزیت دولومیت به صورت مصنوعی در کشور به وجود آمده است. به این ترتیب ماتریسهای ثانویه سیلیکاته موجود در منیزیتها در کنار اکسید کلسیم به ماتریسهای ثانوی با نسوزندگی بالاتر تبدیل شده و درجه نسوزندگی کل محصول را افزایش میدهند.
●ضرورت توجه به صنعت دیرگداز
شاید در نگاه اول صنعت دیرگداز به خودی خود کم اهمیت جلوه نماید. برای درک بهتر جایگاه این صنعت کافی است کاربرد دیرگدازها را در صنایع بزرگ و استراتژیک مانند ذوب آهن، سیمان، پتروشیمی، شیشه و سرامیک و تاثیر مستقیم این مواد بر محصولات تولیدی در این صنایع را مدنظر قرار دهیم. در حال حاضر یکی از مشکلات مهم صنایع بزرگی چون فولاد، پائین بودن کیفیت در عین حال بالا بودن قیمت تمام شده محصولات آن است. یکی از راهها برای رسیدن به کیفیت مناسب در این صنایع استفاده از دیرگدازهای با کیفیت و پربازده است. دلایل زیر اهمیت و ضرورت رویکرد کشور به تولید مواد دیرگداز پیشرفته را نشان میدهد:
۱) استراتژیک بودن: استفاده از این مواد در صنایع نظامی، بعدی استراتژیک به این مواد داده است.
۲) بازار مصرف: با توجه به توسعه صنایع فولاد، سیمان و پتروشیمی در کشور بازار مصرف بسیار خوبی برای این مواد در کشور وجود دارد و در آینده نیز با توجه به توسعه صنایع فوق بازار گسترده و رو به رشدی وجود خواهد داشت.
۳) مزیتهای کشور: با توجه به مزیتهایی که در زمینه تولید در کشور وجود دارد، مانند مواد اولیه ارزان، نیروی متخصص ارزان و ارزان بودن انرژی کشور میتواند پیشرفت خوبی در این زمینه داشته باشد. از مشکلات صنایع دیرگداز استفاده از استانداردهای ابعاد قدیمی در تولید محصولات جدید است که کاربرد مصرفکنندگان را محدود میکند و همچنین میزان بالای مواد دورریختنی به کار برده شده در صنایع مربوطه است. بحثی که در دیرگدازها بسیار اهمیت دارد مسئله بازیافت مواد نسوز است که به این منظور بازیافت ۵۰ درصد از ذخایر منیزیت کشور که به دلیل نداشتن مرغوبیت غیرقابل استفاده تشخیص داده شده در کشور انجام شده است. از دیگر دلایل اهمیت بازیافت مواد دیرگداز میتوان به جنبه اقتصادی و جنبه زیستمحیطی اشاره کرد. از جنبه اقتصادی در اکثر کشورها این مواد دور ریخته شده را بازیافت کرده و دوباره مورد استفاده قرار میدهند که باعث صرفهجوییهای کلان در بعد اقتصادی خواهد شد. از جنبه زیست محیطی مواد دیرگداز مصرف شدهای که دور ریخته میشود میتواند آلودگی محیطزیست را به دنبال داشته باشد. این ماده در اثر نزول باران به کروم ۶ مثبت تبدیل میشود که بسیار سمی است و با وارد شدن به سفرههای زیرزمینی و آلوده کردن آبهای شهری بسیار خطرناک خواهد بود.
●نگاهی به وضعیت تولید مواد دیرگداز
براساس آمار جهانی در سال ۲۰۰۰ میزان مصرف مواد دیرگداز در صنعت فولاد، ۲۵ کیلوگرم به ازای تولید هر تن فولاد بود که این مقدار روز به روز کاهش مییابد. در عین حال از ۲۰ سال گذشته تاکنون تولید فولاد در جهان سالانه بین ۸۲۰ تا ۸۷۰ میلیون تن بوده است و طبق پیشبینیهای انجام شده تا سال ۲۰۱۰ مقدار تولید تفاوت بسیاری نخواهد کرد. در حال حاضر در کشور حدود ۹ میلیون تن فولاد تولید میشود که این میزان، نیازمند ۱۴۰ هزار تن مواد نسوز قلیایی است و با توجه به افزایش تولید فولاد در برنامه چهارم توسعه و در نظر گرفتن تولید ۲۰ تا ۳۰ میلیون تنی فولاد در کشور تا سال ۸۸ برای تولید هر تن فولاد ۲۸۰ هزار تن مواد نسوز قلیایی نیاز است. با توجه به این که به طور متوسط ۹۰ درصد فراوردههای نسوز قلایی از منیزیا یا دولوما تشکیل میشود، تا پایان سال ۱۳۸۸ میزان تقاضا برای این ماده به ۳۲۰ هزار تن خواهد رسید. ذخیره قطعی معادن منیزیت کشور ۳/۵ میلیون تن برآورد شده است که به دلیل وجود ناخالصیها فقط نیمی از منیزیت موجود در کشور بدون نیاز به فراوری به عنوان ماده اولیه منیزیای نسوز مورد استفاده قرار میگیرد. ایران با توجه به پیشینه و نیز معادن و ظرفیتهای قوی میتواند پیشتاز صنعت مواد دیرگداز در منطقه باشد.
مژگان میرزایی
ایران مسعود پزشکیان دولت چهاردهم پزشکیان مجلس شورای اسلامی محمدرضا عارف دولت مجلس کابینه دولت چهاردهم اسماعیل هنیه کابینه پزشکیان محمدجواد ظریف
پیاده روی اربعین تهران عراق پلیس تصادف هواشناسی شهرداری تهران سرقت بازنشستگان قتل آموزش و پرورش دستگیری
ایران خودرو خودرو وام قیمت طلا قیمت دلار قیمت خودرو بانک مرکزی برق بازار خودرو بورس بازار سرمایه قیمت سکه
میراث فرهنگی میدان آزادی سینما رهبر انقلاب بیتا فرهی وزارت فرهنگ و ارشاد اسلامی سینمای ایران تلویزیون کتاب تئاتر موسیقی
وزارت علوم تحقیقات و فناوری آزمون
رژیم صهیونیستی غزه روسیه حماس آمریکا فلسطین جنگ غزه اوکراین حزب الله لبنان دونالد ترامپ طوفان الاقصی ترکیه
پرسپولیس فوتبال ذوب آهن لیگ برتر استقلال لیگ برتر ایران المپیک المپیک 2024 پاریس رئال مادرید لیگ برتر فوتبال ایران مهدی تاج باشگاه پرسپولیس
هوش مصنوعی فناوری سامسونگ ایلان ماسک گوگل تلگرام گوشی ستار هاشمی مریخ روزنامه
فشار خون آلزایمر رژیم غذایی مغز دیابت چاقی افسردگی سلامت پوست